Abstract
This paper discusses the effects of poor installations on orifice measurement and the best practices to achieve highest accuracy and performance. Flow disturbances are everywhere in pipelines and industrial applications. Knowing the types of disturbances, their effect on orifice measurement and how to correct those errors is valuable for anyone interested in accurate orifice flow measurement.
What is “Good” Flow
Most flowmeters are affected by the flow that they are trying to measure, orifice plate flowmeters included. Orifice plates measure best in “good” flow conditions and lose accuracy in “bad” conditions. There are several methods to describe and characterize good vs. bad flow conditions. When asked to describe good flow conditions, many users will use the term Laminar. This is a common yet minor misconception in flow engineering.
Laminar vs. Turbulent Flow
Laminar is a flow regime where the flow follows relatively straight lines down a pipe, Figure 1. If you were to follow a particle in the flow, it would go in a straight path and not cross paths with other particles flowing next to it. This is a regime with no turbulence. Laminar flow will happen in low flow and/or high viscous applications. In other words, the momentum forces are low and/or the viscous forces are high. Inherently this makes sense as higher velocities will encourage turbulence and higher viscosities will do the opposite.
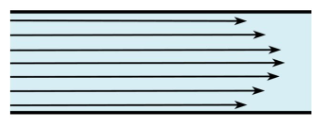
As useful tool is the Reynolds number, which is a dimensionless number used to quantify whether a flow application is in laminar flow. The Reynolds number equations is a follows:
Re=VρD/μ
Re = Reynolds number, dimensionless
V = flow velocity, ft/s
ρ = density, lbm/ft3
μ = dynamic viscosity, lbm/s·ft
The numerator of this equation combines the momentum forces in the flow, velocity, density and size. While the denominator are the inertial forces, viscosity. This follows the logic described earlier. The lower the Reynolds number, the more likely the flow regime is in a laminar state. Laminar flow is more likely to exist where the velocity, density or size is small, and/or where the viscosity is high. The commonly accepted value of laminar flow is Re < 4000. As the Reynolds number increases, the flow regime enters a transition phase between 4000 and 10,000. Above 10,000, the flow regime is considered to be turbulent.
Reynolds number - Flow regime
0 – 4,000 - Laminar
4000 – 10,000 - Transition
>10,000 - Turbulent
Turbulent flow, Figure 2, is the opposite of laminar flow in that the flow streams do not follow a straight or regular pattern. In turbulent flow the flow streams cross, small eddies occur, and mixing is more common. The word “turbulent” rightfully has negative connotations. No one wants to be on an airplane and fly through turbulence.
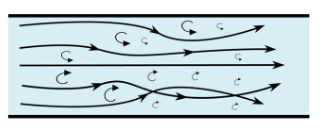
So why is Laminar the incorrect term to describe good flow? It’s not. It’s just not the world in which our flowmeters live. The vast majority of industrial pipelines are in the turbulent flow regime. Virtually all gas flows are turbulent due to the high velocities and low viscosities. Even most liquid flows are turbulent, except for some high viscosity products such as crude oil. Turbulent flow is better for orifice measurement because orifice plates were designed to measure it and their performance is well understood in those conditions.
A side note: Reynolds number is a very helpful in flow measurement. Since it is a dimensionless number, Reynolds can use a single number to describe a flow application. And that number can be used across applications. If the Reynolds number for an application is below 4000, that application is in the laminar flow regime, regardless of the size for example. Reynolds number is used when calibrating a flowmeter. Since the Reynolds number describes the flow in a single number, users can calibrate on one fluid and use the flowmeter in another fluid, knowing the performance will match at equal Reynolds numbers.
Flow profile
A better way to describe understand good vs. bad flow is the presence or absence of flow disturbances. Long, straight, unobstructed pipe will create undisturbed flow. The addition of common pipe elements will create disturbances. Common pipe elements can include single elbows, tees, two elbows in series, partially closed valves, pipe reductions or expansions, thermowells, and many more.
Just like the Reynolds number is a tool to understand the flow regime, the flow profile is a tool to visualize whether flow is disturbed or not. The flow profile attempts to show the velocity at difference points across the diameter of a flowing pipe. This can be physically measured in several ways such as with a single point Pitot tube sensor or with more complex tools such as laser doppler velocimetry. Typically, the view is across a full diameter, crossing through the midpoint of the pipe. A typical flow profile looks like Figure 3 for turbulent flow. Each arrow represents the velocity at points across a diameter of the pipe. The velocities are higher in the center of the pipe and lower near the pipe walls.
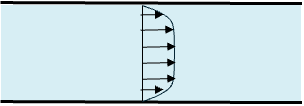
The friction on the pipe walls causes drag which slows down the fluid flow nearest to it. As the flow continues down the pipe, the next layer away from the pipe wall is slowed down slightly less. And so on until the effect of the pipe wall friction no longer affects the velocity. This is called the boundary layer effect and is created whenever flow passes over a surface. Notice the shape of the Figure 3 profile in turbulent flow is different than the shape in Figure 1. Laminar flow has a characteristic “bullet” shaped profile and turbulent has a flatter shape.
Well-developed flow is created when the boundary layer is fully established without disturbances. Put another way, well developed flow will not change its profile as it moves down the pipe. In the industrial flow measurement world, it’s also the definition of good flow and is very important in understanding flow through an orifice.
Power law estimation
When comparing whether a flow profile is well developed or not, a useful tool is the power law estimation. The power law gives a numerical estimation of a well-developed profile. The power law equation is:
u/umax = (1-r/R)1/n
u = velocity at measurement point
umax = max velocity in pipe
r = radius at measurement point
R = pipe radius
n = power
A value of n = 7 is typically used to fit the velocity profile for fully developed, turbulent flows. A higher value of n creates a flatter profile. A lower value creates a more bullet shape profile associated with laminar flow. A power law curve where
n = 7 is shown in Figure 4.
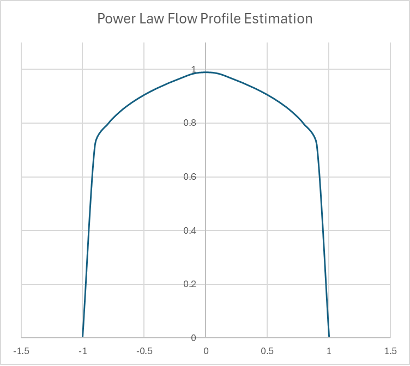
As flow is disturbed with the addition of pipe elements, the flow profile will change. For example, flow through a single elbow creates a skewed profile. The high velocity “core” of the pipe will be pushed to the opposite wall of the pipe, creating an asymmetry where the maximum velocity is no longer in the middle of the pipe. Single elbows and other elements can create asymmetry in the flow profile which is shown well in Figure 5.
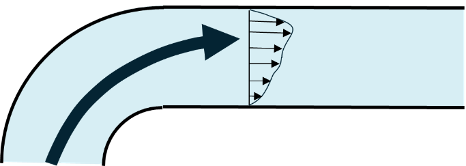
Swirling flow
The flow profile does not capture another type of flow disturbance called swirling flow. Swirling flow is when the flow has a crossflow element. Without swirl the flow will run straight down the pipe, with 0° in relation to the centerline of the pipe. If crossflow is present, the flow streams can have a swirl angle, up to 20° in severe cases.
There are two general types of swirl disturbances, Type 1 and Type 2 swirls. Type 1 swirl moves in one directional rotation across the pipe. This is also known as whole body swirl, Figure 6. Close coupled double elbows out of plane are a common cause of Type 1 swirl, along with headers, pumps and compressors. Type 2 swirl introduces two counter rotating swirls rotating in opposite directions, Figure 7. This is usually created after single elbows.
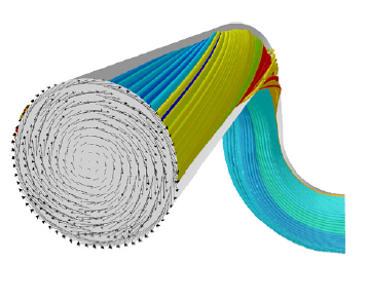
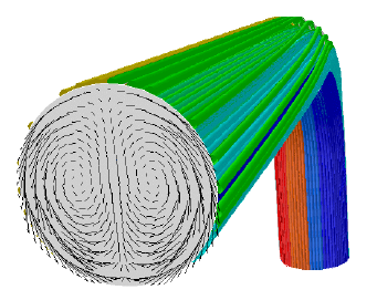
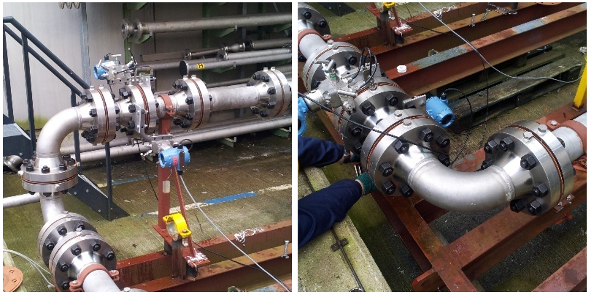
Orifice plate flow measurements
Orifice plates measurement have a century-long track record of continuous use and improvement in industrial applications. No other flow technology has the international volume of understanding and acceptance as orifice plates. Orifice plates are often described as “a hole in a plate” and often ridiculed for that simplicity. Yet it is the simplicity of an orifice plate that makes it so elegant. Leonardo da Vinci once said, “Simplicity is the ultimate sophistication”. The design of the orifice plate makes it possible to manufacture with precision and repeatability. Making one orifice plate measure the same as the next one with matching dimensions. A dimensional inspection is all that is needed to “calibrate” an orifice plate.
Knowing that two identical orifice plates will measure the same (within known uncertainties) is one of the reasons why they are the most widely used industrial flow technology even after 100 years. In today’s world, a user can replace an orifice plate and know the uncertainty of the measurement will not change, even without a flow calibration – something no other flow technology can match!
This also means that a flow calibration once done on a known orifice plate size, can be applied to all other matching orifice plates. Over the decades a massive database of traceable orifice calibrations was completed and used to create the de facto standards for orifice flow measurement. The American standards are the AGA Report No 3 and API 14.3 standards for natural measurement using an orifice plate. The international standard for orifice plates is ISO 5167.
The orifice performance in that technical database (which includes over 30,000 data points!) was tested in well-developed flow conditions. The standards confirm that measurement in matching conditions and dimensions will perform at custody transfer levels of accuracy. And since all the data points were tested in well-developed flow conditions, the standards require the same for accurate measurement.
Effect of flow disturbances on orifice measurement
If a user’s flow conditions are not well developed, with asymmetric or swirling flow, the accuracy will be affected. The effect on accuracy will depend on several factors, including the type of disturbance and the relative distance of the disturbance to the orifice location.
As the distance from the disturbance to the orifice plate increases, the flow will naturally return to a well-developed state due to the turbulence in the flow (turbulence helps us here). The distance needed to return to well-developed flow depends mostly on the type of disturbance. The AGA/API standards recommend up to 44 pipe diameters of straight pipe after double elbow to achieve well developed flow.
Shown below are two sets of flow calibration data from Mattingly and Yeh measuring three different orifice bore sizes (beta ratios) at various distances from a disturbance. Figure 8 shows single elbow effects.Figure 9 shows effects from close coupled, double elbows out of plane.
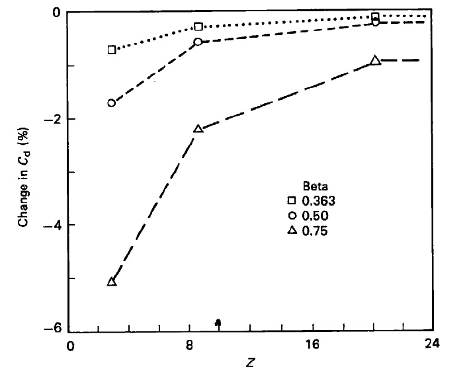
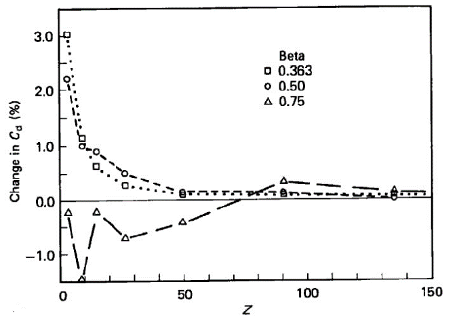
The effect of the disturbance diminishes with distance, approaching zero effect. Notice the effects on accuracy of the orifice plate measurement can be up to 5% after a single elbow using a high beta ratio. The effect lessens using smaller beta ratios. Also notice the x-axis scale of the double elbows chart is much larger than the single elbow chart. This confirms that Type 1 swirl has a much longer lasting impact on flow measurement than Type 2 swirl.
Improving flow conditions
A user can make a determination about their installation knowing the above information. They have three options available to them:
- The user could plan the measurement point as far as possible from the disturbance. The more distance means the more likely the flow is well developed at that point. Some users may have plenty of straight pipe in their system and can meet the minimum requirements in the standards. For most users, creating the necessary straight inlet piping will come with additional expense.
- The user can accept the additional uncertainty that comes with a bad installation. This might be a fine solution in applications with low accuracy requirements. But most industrial applications cannot accept accuracy shifts on the order of ±5%.
- The user could follow the most common practice in the industry: use a flow conditioner.
Flow conditioners
The user of flow conditioners is an industry best practice for ensuring optimal flow measurement with an orifice plate. Flow conditioners come in a variety of designs but have one common goal: to condition the flow to well-developed conditions ahead of an orifice flow measurement point regardless of the disturbance ahead of it.
In the AGA Report No. 3, Section 2.3.1.7 “Flow Conditioners” classifies flow conditioners into two categories: straighteners and isolating flow conditioners.
“Flow straighteners are devices that effectively remove or reduce the swirl component of a flowing stream but may have limited ability to produce the flow conditions necessary to accurately replicate the orifice plate coefficient of discharge database values. Isolating flow conditioners are devices that effectively remove the swirl component from the flowing stream while redistributing the stream to produce the flow conditions that accurately replicate the orifice plate coefficient of discharge database values.”
Flow straighteners
Flow straighteners are low blockage, swirling reducing flow conditioners. Common examples of flow straighteners are tube bundles, example shown in Figure 10 and fin-type straightening vanes, example shown in Figure 11. Tube bundles can be designed with 19 or 7 tubes concentrically grouped in the pipe. The terminology around these can be confusing as tube bundles are sometimes sold as straightening vanes, but both fall into the category of flow straightener as described in AGA 3.
These types of flow conditioners are designed to remove swirl with their elongated dimensions. But since they are low blockages, they do very little to correct he asymmetry in the flow profile. In fact, Mattingly and Yeh also showed that flow straighteners can actually make asymmetry a more persistent flow disturbance, lasting much longer in terms of distance. This is because the flow straighteners will capture the asymmetry entering each tube and reduce the type 2 swirl. By reducing the type 2 swirl, the natural turbulence is diminished and the asymmetry does not break down as quickly.
In short, flow straighteners are not recommended for orifice plate measurement.
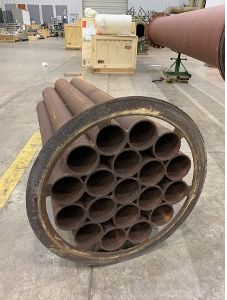

Isolating flow conditioners
Isolating flow conditioners have a blockage factor that forces the flow profile to redistribute as it passes through. This redistribution controls both the asymmetry and swirl disturbances. The design is typically a perforated plate with multiple holes designed to create a well-developed flow profile as soon as possible after the plate.
The search for the ideal pattern of holes to do this job was the subject of much research in the 1990’s as the need for flow conditioning became more and more relevant. A summary of the research from researchers such as Laws, Karnik, Zanker, Gallagher and others is fascinating but outside the scope of this paper. The most widely accepted design of this research was developed by Laws and has become known as the NOVA 50E design.
The NOVA 50E design, Figure 12, is a multi-hole flow conditioner with concentric rings of openings. 16 smaller holes around 8 midsized holes around one large central opening. The size and position of each hole is meant to stimulate the formation of a well-developed flow profile regardless of upstream disturbances. The “50” designation indicates that the plate has approximately a 50% blockage area in the flow path. The success of this design is the balance of three factors: 1) enough blockage to redistribute the flow profile, 2) large enough holes to allow passage of particles and 3) enough opening to reduce the pressure loss across the plate as much as possible. The NOVA design meets the requirements of AGA 3 Section 2.5.5 and APPENDIX 2-D.
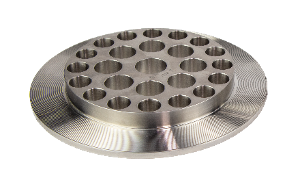
The design is universal for all flow conditions and disturbances. This advantage means a user can have one design flow conditioner for various pipeline installations and conditions. And it gives the user the assurance that most flow disturbances will be removed prior to flow measurement. For as much testing and research has been done of the effects of flow disturbances in a pipe, a user does not know the flow regime and development of their flow profile. Having a flow conditioner improves orifice plate measurement in all standard applications.
Conclusion
The use of a flow conditioner is recommended for all high accuracy orifice plate measurements. The recommended type of flow conditioner is the NOVA 50E design to remove most flow disturbances such as asymmetry and swirl. And users will benefit from the assurance that a well-designed flow conditioner will remove any unknown flow disturbances and problems that could diminish their measurement accuracy.
[1] Effects of pipe elbows and tube bundles onselected types of flowmeters, G.E. Mattingly, T.T. Yeh, Flow Measurement Instrumentation, Vol 2, January 1991
[2] US Patent 5,341,848 “Flow Conditioner”, 1994
Abstract
This paper discusses the effects of poor installations on orifice measurement and the best practices to achieve highest accuracy and performance. Flow disturbances are everywhere in pipelines and industrial applications. Knowing the types of disturbances, their effect on orifice measurement and how to correct those errors is valuable for anyone interested in accurate orifice flow measurement.
What is “Good” Flow
Most flowmeters are affected by the flow that they are trying to measure, orifice plate flowmeters included. Orifice plates measure best in “good” flow conditions and lose accuracy in “bad” conditions. There are several methods to describe and characterize good vs. bad flow conditions. When asked to describe good flow conditions, many users will use the term Laminar. This is a common yet minor misconception in flow engineering.
Laminar vs. Turbulent Flow
Laminar is a flow regime where the flow follows relatively straight lines down a pipe, Figure 1. If you were to follow a particle in the flow, it would go in a straight path and not cross paths with other particles flowing next to it. This is a regime with no turbulence. Laminar flow will happen in low flow and/or high viscous applications. In other words, the momentum forces are low and/or the viscous forces are high. Inherently this makes sense as higher velocities will encourage turbulence and higher viscosities will do the opposite.
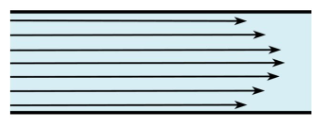
As useful tool is the Reynolds number, which is a dimensionless number used to quantify whether a flow application is in laminar flow. The Reynolds number equations is a follows:
Re=VρD/μ
Re = Reynolds number, dimensionless
V = flow velocity, ft/s
ρ = density, lbm/ft3
μ = dynamic viscosity, lbm/s·ft
The numerator of this equation combines the momentum forces in the flow, velocity, density and size. While the denominator are the inertial forces, viscosity. This follows the logic described earlier. The lower the Reynolds number, the more likely the flow regime is in a laminar state. Laminar flow is more likely to exist where the velocity, density or size is small, and/or where the viscosity is high. The commonly accepted value of laminar flow is Re < 4000. As the Reynolds number increases, the flow regime enters a transition phase between 4000 and 10,000. Above 10,000, the flow regime is considered to be turbulent.
Reynolds number - Flow regime
0 – 4,000 - Laminar
4000 – 10,000 - Transition
>10,000 - Turbulent
Turbulent flow, Figure 2, is the opposite of laminar flow in that the flow streams do not follow a straight or regular pattern. In turbulent flow the flow streams cross, small eddies occur, and mixing is more common. The word “turbulent” rightfully has negative connotations. No one wants to be on an airplane and fly through turbulence.
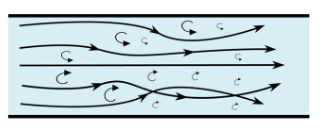
So why is Laminar the incorrect term to describe good flow? It’s not. It’s just not the world in which our flowmeters live. The vast majority of industrial pipelines are in the turbulent flow regime. Virtually all gas flows are turbulent due to the high velocities and low viscosities. Even most liquid flows are turbulent, except for some high viscosity products such as crude oil. Turbulent flow is better for orifice measurement because orifice plates were designed to measure it and their performance is well understood in those conditions.
A side note: Reynolds number is a very helpful in flow measurement. Since it is a dimensionless number, Reynolds can use a single number to describe a flow application. And that number can be used across applications. If the Reynolds number for an application is below 4000, that application is in the laminar flow regime, regardless of the size for example. Reynolds number is used when calibrating a flowmeter. Since the Reynolds number describes the flow in a single number, users can calibrate on one fluid and use the flowmeter in another fluid, knowing the performance will match at equal Reynolds numbers.
Flow profile
A better way to describe understand good vs. bad flow is the presence or absence of flow disturbances. Long, straight, unobstructed pipe will create undisturbed flow. The addition of common pipe elements will create disturbances. Common pipe elements can include single elbows, tees, two elbows in series, partially closed valves, pipe reductions or expansions, thermowells, and many more.
Just like the Reynolds number is a tool to understand the flow regime, the flow profile is a tool to visualize whether flow is disturbed or not. The flow profile attempts to show the velocity at difference points across the diameter of a flowing pipe. This can be physically measured in several ways such as with a single point Pitot tube sensor or with more complex tools such as laser doppler velocimetry. Typically, the view is across a full diameter, crossing through the midpoint of the pipe. A typical flow profile looks like Figure 3 for turbulent flow. Each arrow represents the velocity at points across a diameter of the pipe. The velocities are higher in the center of the pipe and lower near the pipe walls.
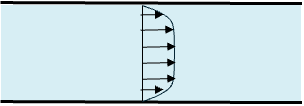
The friction on the pipe walls causes drag which slows down the fluid flow nearest to it. As the flow continues down the pipe, the next layer away from the pipe wall is slowed down slightly less. And so on until the effect of the pipe wall friction no longer affects the velocity. This is called the boundary layer effect and is created whenever flow passes over a surface. Notice the shape of the Figure 3 profile in turbulent flow is different than the shape in Figure 1. Laminar flow has a characteristic “bullet” shaped profile and turbulent has a flatter shape.
Well-developed flow is created when the boundary layer is fully established without disturbances. Put another way, well developed flow will not change its profile as it moves down the pipe. In the industrial flow measurement world, it’s also the definition of good flow and is very important in understanding flow through an orifice.
Power law estimation
When comparing whether a flow profile is well developed or not, a useful tool is the power law estimation. The power law gives a numerical estimation of a well-developed profile. The power law equation is:
u/umax = (1-r/R)1/n
u = velocity at measurement point
umax = max velocity in pipe
r = radius at measurement point
R = pipe radius
n = power
A value of n = 7 is typically used to fit the velocity profile for fully developed, turbulent flows. A higher value of n creates a flatter profile. A lower value creates a more bullet shape profile associated with laminar flow. A power law curve where
n = 7 is shown in Figure 4.
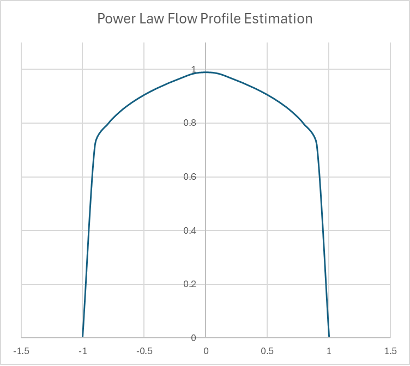
As flow is disturbed with the addition of pipe elements, the flow profile will change. For example, flow through a single elbow creates a skewed profile. The high velocity “core” of the pipe will be pushed to the opposite wall of the pipe, creating an asymmetry where the maximum velocity is no longer in the middle of the pipe. Single elbows and other elements can create asymmetry in the flow profile which is shown well in Figure 5.
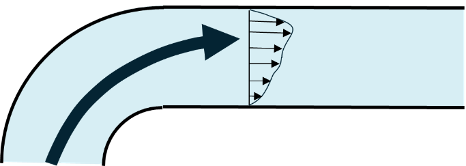
Swirling flow
The flow profile does not capture another type of flow disturbance called swirling flow. Swirling flow is when the flow has a crossflow element. Without swirl the flow will run straight down the pipe, with 0° in relation to the centerline of the pipe. If crossflow is present, the flow streams can have a swirl angle, up to 20° in severe cases.
There are two general types of swirl disturbances, Type 1 and Type 2 swirls. Type 1 swirl moves in one directional rotation across the pipe. This is also known as whole body swirl, Figure 6. Close coupled double elbows out of plane are a common cause of Type 1 swirl, along with headers, pumps and compressors. Type 2 swirl introduces two counter rotating swirls rotating in opposite directions, Figure 7. This is usually created after single elbows.
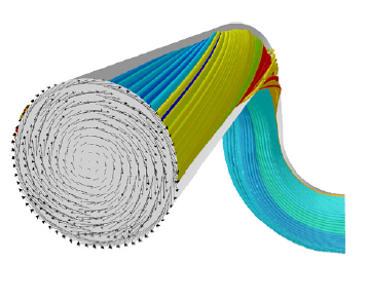
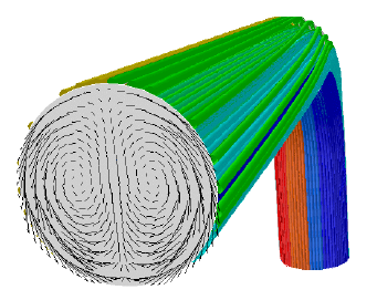
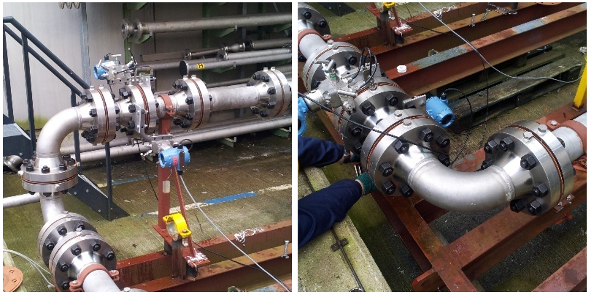
Orifice plate flow measurements
Orifice plates measurement have a century-long track record of continuous use and improvement in industrial applications. No other flow technology has the international volume of understanding and acceptance as orifice plates. Orifice plates are often described as “a hole in a plate” and often ridiculed for that simplicity. Yet it is the simplicity of an orifice plate that makes it so elegant. Leonardo da Vinci once said, “Simplicity is the ultimate sophistication”. The design of the orifice plate makes it possible to manufacture with precision and repeatability. Making one orifice plate measure the same as the next one with matching dimensions. A dimensional inspection is all that is needed to “calibrate” an orifice plate.
Knowing that two identical orifice plates will measure the same (within known uncertainties) is one of the reasons why they are the most widely used industrial flow technology even after 100 years. In today’s world, a user can replace an orifice plate and know the uncertainty of the measurement will not change, even without a flow calibration – something no other flow technology can match!
This also means that a flow calibration once done on a known orifice plate size, can be applied to all other matching orifice plates. Over the decades a massive database of traceable orifice calibrations was completed and used to create the de facto standards for orifice flow measurement. The American standards are the AGA Report No 3 and API 14.3 standards for natural measurement using an orifice plate. The international standard for orifice plates is ISO 5167.
The orifice performance in that technical database (which includes over 30,000 data points!) was tested in well-developed flow conditions. The standards confirm that measurement in matching conditions and dimensions will perform at custody transfer levels of accuracy. And since all the data points were tested in well-developed flow conditions, the standards require the same for accurate measurement.
Effect of flow disturbances on orifice measurement
If a user’s flow conditions are not well developed, with asymmetric or swirling flow, the accuracy will be affected. The effect on accuracy will depend on several factors, including the type of disturbance and the relative distance of the disturbance to the orifice location.
As the distance from the disturbance to the orifice plate increases, the flow will naturally return to a well-developed state due to the turbulence in the flow (turbulence helps us here). The distance needed to return to well-developed flow depends mostly on the type of disturbance. The AGA/API standards recommend up to 44 pipe diameters of straight pipe after double elbow to achieve well developed flow.
Shown below are two sets of flow calibration data from Mattingly and Yeh measuring three different orifice bore sizes (beta ratios) at various distances from a disturbance. Figure 8 shows single elbow effects.Figure 9 shows effects from close coupled, double elbows out of plane.
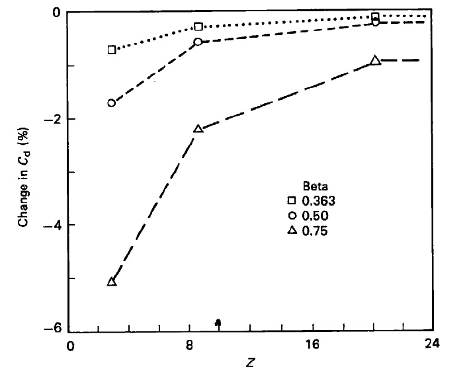
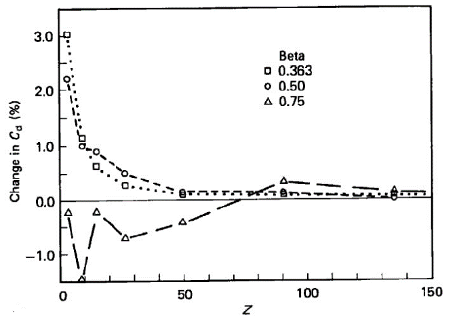
The effect of the disturbance diminishes with distance, approaching zero effect. Notice the effects on accuracy of the orifice plate measurement can be up to 5% after a single elbow using a high beta ratio. The effect lessens using smaller beta ratios. Also notice the x-axis scale of the double elbows chart is much larger than the single elbow chart. This confirms that Type 1 swirl has a much longer lasting impact on flow measurement than Type 2 swirl.
Improving flow conditions
A user can make a determination about their installation knowing the above information. They have three options available to them:
- The user could plan the measurement point as far as possible from the disturbance. The more distance means the more likely the flow is well developed at that point. Some users may have plenty of straight pipe in their system and can meet the minimum requirements in the standards. For most users, creating the necessary straight inlet piping will come with additional expense.
- The user can accept the additional uncertainty that comes with a bad installation. This might be a fine solution in applications with low accuracy requirements. But most industrial applications cannot accept accuracy shifts on the order of ±5%.
- The user could follow the most common practice in the industry: use a flow conditioner.
Flow conditioners
The user of flow conditioners is an industry best practice for ensuring optimal flow measurement with an orifice plate. Flow conditioners come in a variety of designs but have one common goal: to condition the flow to well-developed conditions ahead of an orifice flow measurement point regardless of the disturbance ahead of it.
In the AGA Report No. 3, Section 2.3.1.7 “Flow Conditioners” classifies flow conditioners into two categories: straighteners and isolating flow conditioners.
“Flow straighteners are devices that effectively remove or reduce the swirl component of a flowing stream but may have limited ability to produce the flow conditions necessary to accurately replicate the orifice plate coefficient of discharge database values. Isolating flow conditioners are devices that effectively remove the swirl component from the flowing stream while redistributing the stream to produce the flow conditions that accurately replicate the orifice plate coefficient of discharge database values.”
Flow straighteners
Flow straighteners are low blockage, swirling reducing flow conditioners. Common examples of flow straighteners are tube bundles, example shown in Figure 10 and fin-type straightening vanes, example shown in Figure 11. Tube bundles can be designed with 19 or 7 tubes concentrically grouped in the pipe. The terminology around these can be confusing as tube bundles are sometimes sold as straightening vanes, but both fall into the category of flow straightener as described in AGA 3.
These types of flow conditioners are designed to remove swirl with their elongated dimensions. But since they are low blockages, they do very little to correct he asymmetry in the flow profile. In fact, Mattingly and Yeh also showed that flow straighteners can actually make asymmetry a more persistent flow disturbance, lasting much longer in terms of distance. This is because the flow straighteners will capture the asymmetry entering each tube and reduce the type 2 swirl. By reducing the type 2 swirl, the natural turbulence is diminished and the asymmetry does not break down as quickly.
In short, flow straighteners are not recommended for orifice plate measurement.
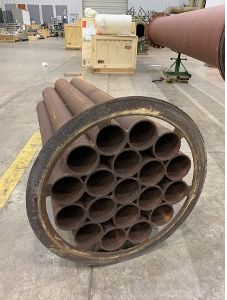

Isolating flow conditioners
Isolating flow conditioners have a blockage factor that forces the flow profile to redistribute as it passes through. This redistribution controls both the asymmetry and swirl disturbances. The design is typically a perforated plate with multiple holes designed to create a well-developed flow profile as soon as possible after the plate.
The search for the ideal pattern of holes to do this job was the subject of much research in the 1990’s as the need for flow conditioning became more and more relevant. A summary of the research from researchers such as Laws, Karnik, Zanker, Gallagher and others is fascinating but outside the scope of this paper. The most widely accepted design of this research was developed by Laws and has become known as the NOVA 50E design.
The NOVA 50E design, Figure 12, is a multi-hole flow conditioner with concentric rings of openings. 16 smaller holes around 8 midsized holes around one large central opening. The size and position of each hole is meant to stimulate the formation of a well-developed flow profile regardless of upstream disturbances. The “50” designation indicates that the plate has approximately a 50% blockage area in the flow path. The success of this design is the balance of three factors: 1) enough blockage to redistribute the flow profile, 2) large enough holes to allow passage of particles and 3) enough opening to reduce the pressure loss across the plate as much as possible. The NOVA design meets the requirements of AGA 3 Section 2.5.5 and APPENDIX 2-D.
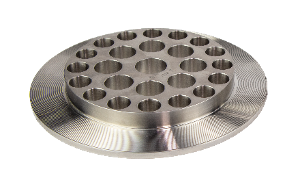
The design is universal for all flow conditions and disturbances. This advantage means a user can have one design flow conditioner for various pipeline installations and conditions. And it gives the user the assurance that most flow disturbances will be removed prior to flow measurement. For as much testing and research has been done of the effects of flow disturbances in a pipe, a user does not know the flow regime and development of their flow profile. Having a flow conditioner improves orifice plate measurement in all standard applications.
Conclusion
The use of a flow conditioner is recommended for all high accuracy orifice plate measurements. The recommended type of flow conditioner is the NOVA 50E design to remove most flow disturbances such as asymmetry and swirl. And users will benefit from the assurance that a well-designed flow conditioner will remove any unknown flow disturbances and problems that could diminish their measurement accuracy.
[1] Effects of pipe elbows and tube bundles onselected types of flowmeters, G.E. Mattingly, T.T. Yeh, Flow Measurement Instrumentation, Vol 2, January 1991
[2] US Patent 5,341,848 “Flow Conditioner”, 1994
Abstract
This paper discusses the effects of poor installations on orifice measurement and the best practices to achieve highest accuracy and performance. Flow disturbances are everywhere in pipelines and industrial applications. Knowing the types of disturbances, their effect on orifice measurement and how to correct those errors is valuable for anyone interested in accurate orifice flow measurement.
What is “Good” Flow
Most flowmeters are affected by the flow that they are trying to measure, orifice plate flowmeters included. Orifice plates measure best in “good” flow conditions and lose accuracy in “bad” conditions. There are several methods to describe and characterize good vs. bad flow conditions. When asked to describe good flow conditions, many users will use the term Laminar. This is a common yet minor misconception in flow engineering.
Laminar vs. Turbulent Flow
Laminar is a flow regime where the flow follows relatively straight lines down a pipe, Figure 1. If you were to follow a particle in the flow, it would go in a straight path and not cross paths with other particles flowing next to it. This is a regime with no turbulence. Laminar flow will happen in low flow and/or high viscous applications. In other words, the momentum forces are low and/or the viscous forces are high. Inherently this makes sense as higher velocities will encourage turbulence and higher viscosities will do the opposite.
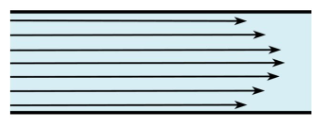
As useful tool is the Reynolds number, which is a dimensionless number used to quantify whether a flow application is in laminar flow. The Reynolds number equations is a follows:
Re=VρD/μ
Re = Reynolds number, dimensionless
V = flow velocity, ft/s
ρ = density, lbm/ft3
μ = dynamic viscosity, lbm/s·ft
The numerator of this equation combines the momentum forces in the flow, velocity, density and size. While the denominator are the inertial forces, viscosity. This follows the logic described earlier. The lower the Reynolds number, the more likely the flow regime is in a laminar state. Laminar flow is more likely to exist where the velocity, density or size is small, and/or where the viscosity is high. The commonly accepted value of laminar flow is Re < 4000. As the Reynolds number increases, the flow regime enters a transition phase between 4000 and 10,000. Above 10,000, the flow regime is considered to be turbulent.
Reynolds number - Flow regime
0 – 4,000 - Laminar
4000 – 10,000 - Transition
>10,000 - Turbulent
Turbulent flow, Figure 2, is the opposite of laminar flow in that the flow streams do not follow a straight or regular pattern. In turbulent flow the flow streams cross, small eddies occur, and mixing is more common. The word “turbulent” rightfully has negative connotations. No one wants to be on an airplane and fly through turbulence.
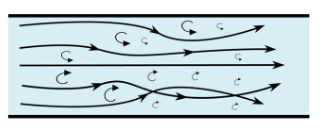
So why is Laminar the incorrect term to describe good flow? It’s not. It’s just not the world in which our flowmeters live. The vast majority of industrial pipelines are in the turbulent flow regime. Virtually all gas flows are turbulent due to the high velocities and low viscosities. Even most liquid flows are turbulent, except for some high viscosity products such as crude oil. Turbulent flow is better for orifice measurement because orifice plates were designed to measure it and their performance is well understood in those conditions.
A side note: Reynolds number is a very helpful in flow measurement. Since it is a dimensionless number, Reynolds can use a single number to describe a flow application. And that number can be used across applications. If the Reynolds number for an application is below 4000, that application is in the laminar flow regime, regardless of the size for example. Reynolds number is used when calibrating a flowmeter. Since the Reynolds number describes the flow in a single number, users can calibrate on one fluid and use the flowmeter in another fluid, knowing the performance will match at equal Reynolds numbers.
Flow profile
A better way to describe understand good vs. bad flow is the presence or absence of flow disturbances. Long, straight, unobstructed pipe will create undisturbed flow. The addition of common pipe elements will create disturbances. Common pipe elements can include single elbows, tees, two elbows in series, partially closed valves, pipe reductions or expansions, thermowells, and many more.
Just like the Reynolds number is a tool to understand the flow regime, the flow profile is a tool to visualize whether flow is disturbed or not. The flow profile attempts to show the velocity at difference points across the diameter of a flowing pipe. This can be physically measured in several ways such as with a single point Pitot tube sensor or with more complex tools such as laser doppler velocimetry. Typically, the view is across a full diameter, crossing through the midpoint of the pipe. A typical flow profile looks like Figure 3 for turbulent flow. Each arrow represents the velocity at points across a diameter of the pipe. The velocities are higher in the center of the pipe and lower near the pipe walls.
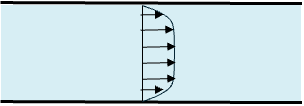
The friction on the pipe walls causes drag which slows down the fluid flow nearest to it. As the flow continues down the pipe, the next layer away from the pipe wall is slowed down slightly less. And so on until the effect of the pipe wall friction no longer affects the velocity. This is called the boundary layer effect and is created whenever flow passes over a surface. Notice the shape of the Figure 3 profile in turbulent flow is different than the shape in Figure 1. Laminar flow has a characteristic “bullet” shaped profile and turbulent has a flatter shape.
Well-developed flow is created when the boundary layer is fully established without disturbances. Put another way, well developed flow will not change its profile as it moves down the pipe. In the industrial flow measurement world, it’s also the definition of good flow and is very important in understanding flow through an orifice.
Power law estimation
When comparing whether a flow profile is well developed or not, a useful tool is the power law estimation. The power law gives a numerical estimation of a well-developed profile. The power law equation is:
u/umax = (1-r/R)1/n
u = velocity at measurement point
umax = max velocity in pipe
r = radius at measurement point
R = pipe radius
n = power
A value of n = 7 is typically used to fit the velocity profile for fully developed, turbulent flows. A higher value of n creates a flatter profile. A lower value creates a more bullet shape profile associated with laminar flow. A power law curve where
n = 7 is shown in Figure 4.
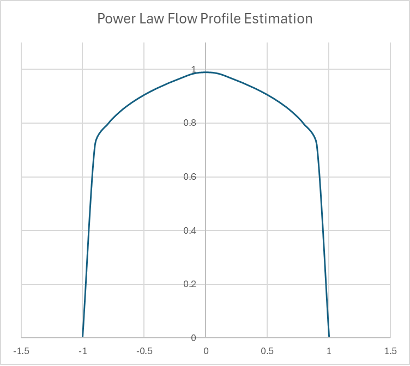
As flow is disturbed with the addition of pipe elements, the flow profile will change. For example, flow through a single elbow creates a skewed profile. The high velocity “core” of the pipe will be pushed to the opposite wall of the pipe, creating an asymmetry where the maximum velocity is no longer in the middle of the pipe. Single elbows and other elements can create asymmetry in the flow profile which is shown well in Figure 5.
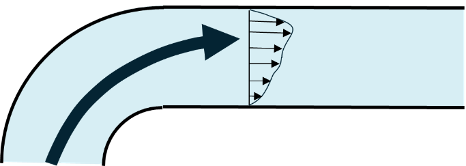
Swirling flow
The flow profile does not capture another type of flow disturbance called swirling flow. Swirling flow is when the flow has a crossflow element. Without swirl the flow will run straight down the pipe, with 0° in relation to the centerline of the pipe. If crossflow is present, the flow streams can have a swirl angle, up to 20° in severe cases.
There are two general types of swirl disturbances, Type 1 and Type 2 swirls. Type 1 swirl moves in one directional rotation across the pipe. This is also known as whole body swirl, Figure 6. Close coupled double elbows out of plane are a common cause of Type 1 swirl, along with headers, pumps and compressors. Type 2 swirl introduces two counter rotating swirls rotating in opposite directions, Figure 7. This is usually created after single elbows.
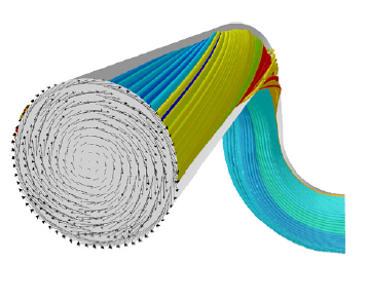
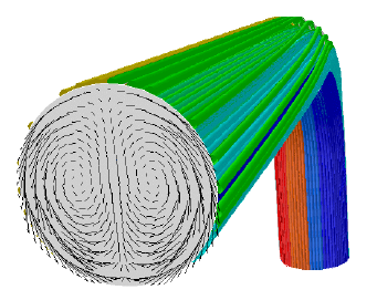
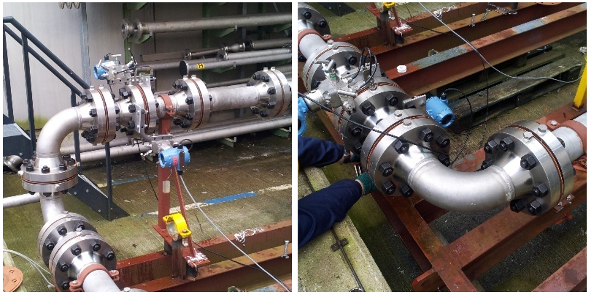
Orifice plate flow measurements
Orifice plates measurement have a century-long track record of continuous use and improvement in industrial applications. No other flow technology has the international volume of understanding and acceptance as orifice plates. Orifice plates are often described as “a hole in a plate” and often ridiculed for that simplicity. Yet it is the simplicity of an orifice plate that makes it so elegant. Leonardo da Vinci once said, “Simplicity is the ultimate sophistication”. The design of the orifice plate makes it possible to manufacture with precision and repeatability. Making one orifice plate measure the same as the next one with matching dimensions. A dimensional inspection is all that is needed to “calibrate” an orifice plate.
Knowing that two identical orifice plates will measure the same (within known uncertainties) is one of the reasons why they are the most widely used industrial flow technology even after 100 years. In today’s world, a user can replace an orifice plate and know the uncertainty of the measurement will not change, even without a flow calibration – something no other flow technology can match!
This also means that a flow calibration once done on a known orifice plate size, can be applied to all other matching orifice plates. Over the decades a massive database of traceable orifice calibrations was completed and used to create the de facto standards for orifice flow measurement. The American standards are the AGA Report No 3 and API 14.3 standards for natural measurement using an orifice plate. The international standard for orifice plates is ISO 5167.
The orifice performance in that technical database (which includes over 30,000 data points!) was tested in well-developed flow conditions. The standards confirm that measurement in matching conditions and dimensions will perform at custody transfer levels of accuracy. And since all the data points were tested in well-developed flow conditions, the standards require the same for accurate measurement.
Effect of flow disturbances on orifice measurement
If a user’s flow conditions are not well developed, with asymmetric or swirling flow, the accuracy will be affected. The effect on accuracy will depend on several factors, including the type of disturbance and the relative distance of the disturbance to the orifice location.
As the distance from the disturbance to the orifice plate increases, the flow will naturally return to a well-developed state due to the turbulence in the flow (turbulence helps us here). The distance needed to return to well-developed flow depends mostly on the type of disturbance. The AGA/API standards recommend up to 44 pipe diameters of straight pipe after double elbow to achieve well developed flow.
Shown below are two sets of flow calibration data from Mattingly and Yeh measuring three different orifice bore sizes (beta ratios) at various distances from a disturbance. Figure 8 shows single elbow effects.Figure 9 shows effects from close coupled, double elbows out of plane.
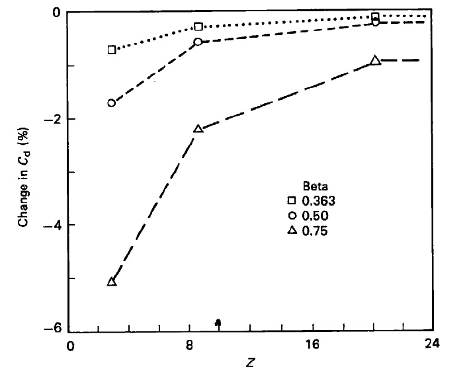
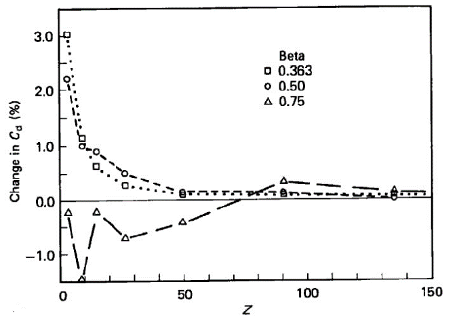
The effect of the disturbance diminishes with distance, approaching zero effect. Notice the effects on accuracy of the orifice plate measurement can be up to 5% after a single elbow using a high beta ratio. The effect lessens using smaller beta ratios. Also notice the x-axis scale of the double elbows chart is much larger than the single elbow chart. This confirms that Type 1 swirl has a much longer lasting impact on flow measurement than Type 2 swirl.
Improving flow conditions
A user can make a determination about their installation knowing the above information. They have three options available to them:
- The user could plan the measurement point as far as possible from the disturbance. The more distance means the more likely the flow is well developed at that point. Some users may have plenty of straight pipe in their system and can meet the minimum requirements in the standards. For most users, creating the necessary straight inlet piping will come with additional expense.
- The user can accept the additional uncertainty that comes with a bad installation. This might be a fine solution in applications with low accuracy requirements. But most industrial applications cannot accept accuracy shifts on the order of ±5%.
- The user could follow the most common practice in the industry: use a flow conditioner.
Flow conditioners
The user of flow conditioners is an industry best practice for ensuring optimal flow measurement with an orifice plate. Flow conditioners come in a variety of designs but have one common goal: to condition the flow to well-developed conditions ahead of an orifice flow measurement point regardless of the disturbance ahead of it.
In the AGA Report No. 3, Section 2.3.1.7 “Flow Conditioners” classifies flow conditioners into two categories: straighteners and isolating flow conditioners.
“Flow straighteners are devices that effectively remove or reduce the swirl component of a flowing stream but may have limited ability to produce the flow conditions necessary to accurately replicate the orifice plate coefficient of discharge database values. Isolating flow conditioners are devices that effectively remove the swirl component from the flowing stream while redistributing the stream to produce the flow conditions that accurately replicate the orifice plate coefficient of discharge database values.”
Flow straighteners
Flow straighteners are low blockage, swirling reducing flow conditioners. Common examples of flow straighteners are tube bundles, example shown in Figure 10 and fin-type straightening vanes, example shown in Figure 11. Tube bundles can be designed with 19 or 7 tubes concentrically grouped in the pipe. The terminology around these can be confusing as tube bundles are sometimes sold as straightening vanes, but both fall into the category of flow straightener as described in AGA 3.
These types of flow conditioners are designed to remove swirl with their elongated dimensions. But since they are low blockages, they do very little to correct he asymmetry in the flow profile. In fact, Mattingly and Yeh also showed that flow straighteners can actually make asymmetry a more persistent flow disturbance, lasting much longer in terms of distance. This is because the flow straighteners will capture the asymmetry entering each tube and reduce the type 2 swirl. By reducing the type 2 swirl, the natural turbulence is diminished and the asymmetry does not break down as quickly.
In short, flow straighteners are not recommended for orifice plate measurement.
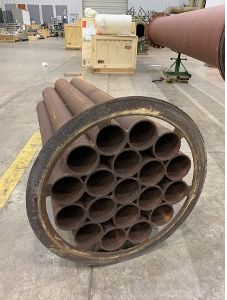

Isolating flow conditioners
Isolating flow conditioners have a blockage factor that forces the flow profile to redistribute as it passes through. This redistribution controls both the asymmetry and swirl disturbances. The design is typically a perforated plate with multiple holes designed to create a well-developed flow profile as soon as possible after the plate.
The search for the ideal pattern of holes to do this job was the subject of much research in the 1990’s as the need for flow conditioning became more and more relevant. A summary of the research from researchers such as Laws, Karnik, Zanker, Gallagher and others is fascinating but outside the scope of this paper. The most widely accepted design of this research was developed by Laws and has become known as the NOVA 50E design.
The NOVA 50E design, Figure 12, is a multi-hole flow conditioner with concentric rings of openings. 16 smaller holes around 8 midsized holes around one large central opening. The size and position of each hole is meant to stimulate the formation of a well-developed flow profile regardless of upstream disturbances. The “50” designation indicates that the plate has approximately a 50% blockage area in the flow path. The success of this design is the balance of three factors: 1) enough blockage to redistribute the flow profile, 2) large enough holes to allow passage of particles and 3) enough opening to reduce the pressure loss across the plate as much as possible. The NOVA design meets the requirements of AGA 3 Section 2.5.5 and APPENDIX 2-D.
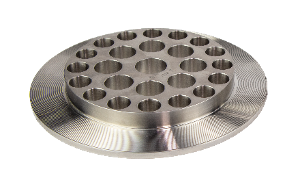
The design is universal for all flow conditions and disturbances. This advantage means a user can have one design flow conditioner for various pipeline installations and conditions. And it gives the user the assurance that most flow disturbances will be removed prior to flow measurement. For as much testing and research has been done of the effects of flow disturbances in a pipe, a user does not know the flow regime and development of their flow profile. Having a flow conditioner improves orifice plate measurement in all standard applications.
Conclusion
The use of a flow conditioner is recommended for all high accuracy orifice plate measurements. The recommended type of flow conditioner is the NOVA 50E design to remove most flow disturbances such as asymmetry and swirl. And users will benefit from the assurance that a well-designed flow conditioner will remove any unknown flow disturbances and problems that could diminish their measurement accuracy.
[1] Effects of pipe elbows and tube bundles onselected types of flowmeters, G.E. Mattingly, T.T. Yeh, Flow Measurement Instrumentation, Vol 2, January 1991
[2] US Patent 5,341,848 “Flow Conditioner”, 1994
Abstract
This paper discusses the effects of poor installations on orifice measurement and the best practices to achieve highest accuracy and performance. Flow disturbances are everywhere in pipelines and industrial applications. Knowing the types of disturbances, their effect on orifice measurement and how to correct those errors is valuable for anyone interested in accurate orifice flow measurement.
What is “Good” Flow
Most flowmeters are affected by the flow that they are trying to measure, orifice plate flowmeters included. Orifice plates measure best in “good” flow conditions and lose accuracy in “bad” conditions. There are several methods to describe and characterize good vs. bad flow conditions. When asked to describe good flow conditions, many users will use the term Laminar. This is a common yet minor misconception in flow engineering.
Laminar vs. Turbulent Flow
Laminar is a flow regime where the flow follows relatively straight lines down a pipe, Figure 1. If you were to follow a particle in the flow, it would go in a straight path and not cross paths with other particles flowing next to it. This is a regime with no turbulence. Laminar flow will happen in low flow and/or high viscous applications. In other words, the momentum forces are low and/or the viscous forces are high. Inherently this makes sense as higher velocities will encourage turbulence and higher viscosities will do the opposite.
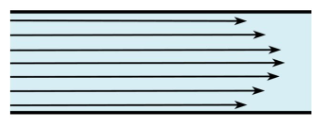
As useful tool is the Reynolds number, which is a dimensionless number used to quantify whether a flow application is in laminar flow. The Reynolds number equations is a follows:
Re=VρD/μ
Re = Reynolds number, dimensionless
V = flow velocity, ft/s
ρ = density, lbm/ft3
μ = dynamic viscosity, lbm/s·ft
The numerator of this equation combines the momentum forces in the flow, velocity, density and size. While the denominator are the inertial forces, viscosity. This follows the logic described earlier. The lower the Reynolds number, the more likely the flow regime is in a laminar state. Laminar flow is more likely to exist where the velocity, density or size is small, and/or where the viscosity is high. The commonly accepted value of laminar flow is Re < 4000. As the Reynolds number increases, the flow regime enters a transition phase between 4000 and 10,000. Above 10,000, the flow regime is considered to be turbulent.
Reynolds number - Flow regime
0 – 4,000 - Laminar
4000 – 10,000 - Transition
>10,000 - Turbulent
Turbulent flow, Figure 2, is the opposite of laminar flow in that the flow streams do not follow a straight or regular pattern. In turbulent flow the flow streams cross, small eddies occur, and mixing is more common. The word “turbulent” rightfully has negative connotations. No one wants to be on an airplane and fly through turbulence.
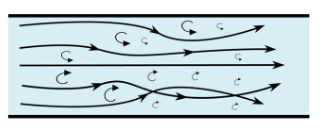
So why is Laminar the incorrect term to describe good flow? It’s not. It’s just not the world in which our flowmeters live. The vast majority of industrial pipelines are in the turbulent flow regime. Virtually all gas flows are turbulent due to the high velocities and low viscosities. Even most liquid flows are turbulent, except for some high viscosity products such as crude oil. Turbulent flow is better for orifice measurement because orifice plates were designed to measure it and their performance is well understood in those conditions.
A side note: Reynolds number is a very helpful in flow measurement. Since it is a dimensionless number, Reynolds can use a single number to describe a flow application. And that number can be used across applications. If the Reynolds number for an application is below 4000, that application is in the laminar flow regime, regardless of the size for example. Reynolds number is used when calibrating a flowmeter. Since the Reynolds number describes the flow in a single number, users can calibrate on one fluid and use the flowmeter in another fluid, knowing the performance will match at equal Reynolds numbers.
Flow profile
A better way to describe understand good vs. bad flow is the presence or absence of flow disturbances. Long, straight, unobstructed pipe will create undisturbed flow. The addition of common pipe elements will create disturbances. Common pipe elements can include single elbows, tees, two elbows in series, partially closed valves, pipe reductions or expansions, thermowells, and many more.
Just like the Reynolds number is a tool to understand the flow regime, the flow profile is a tool to visualize whether flow is disturbed or not. The flow profile attempts to show the velocity at difference points across the diameter of a flowing pipe. This can be physically measured in several ways such as with a single point Pitot tube sensor or with more complex tools such as laser doppler velocimetry. Typically, the view is across a full diameter, crossing through the midpoint of the pipe. A typical flow profile looks like Figure 3 for turbulent flow. Each arrow represents the velocity at points across a diameter of the pipe. The velocities are higher in the center of the pipe and lower near the pipe walls.
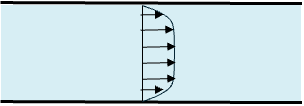
The friction on the pipe walls causes drag which slows down the fluid flow nearest to it. As the flow continues down the pipe, the next layer away from the pipe wall is slowed down slightly less. And so on until the effect of the pipe wall friction no longer affects the velocity. This is called the boundary layer effect and is created whenever flow passes over a surface. Notice the shape of the Figure 3 profile in turbulent flow is different than the shape in Figure 1. Laminar flow has a characteristic “bullet” shaped profile and turbulent has a flatter shape.
Well-developed flow is created when the boundary layer is fully established without disturbances. Put another way, well developed flow will not change its profile as it moves down the pipe. In the industrial flow measurement world, it’s also the definition of good flow and is very important in understanding flow through an orifice.
Power law estimation
When comparing whether a flow profile is well developed or not, a useful tool is the power law estimation. The power law gives a numerical estimation of a well-developed profile. The power law equation is:
u/umax = (1-r/R)1/n
u = velocity at measurement point
umax = max velocity in pipe
r = radius at measurement point
R = pipe radius
n = power
A value of n = 7 is typically used to fit the velocity profile for fully developed, turbulent flows. A higher value of n creates a flatter profile. A lower value creates a more bullet shape profile associated with laminar flow. A power law curve where
n = 7 is shown in Figure 4.
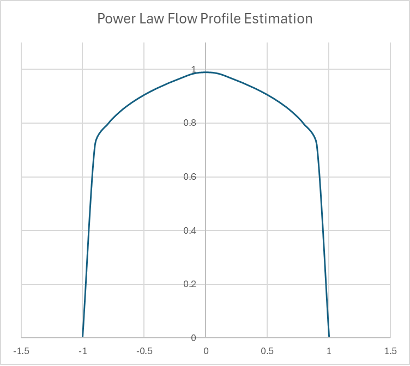
As flow is disturbed with the addition of pipe elements, the flow profile will change. For example, flow through a single elbow creates a skewed profile. The high velocity “core” of the pipe will be pushed to the opposite wall of the pipe, creating an asymmetry where the maximum velocity is no longer in the middle of the pipe. Single elbows and other elements can create asymmetry in the flow profile which is shown well in Figure 5.
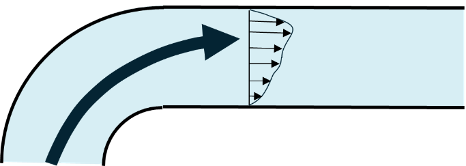
Swirling flow
The flow profile does not capture another type of flow disturbance called swirling flow. Swirling flow is when the flow has a crossflow element. Without swirl the flow will run straight down the pipe, with 0° in relation to the centerline of the pipe. If crossflow is present, the flow streams can have a swirl angle, up to 20° in severe cases.
There are two general types of swirl disturbances, Type 1 and Type 2 swirls. Type 1 swirl moves in one directional rotation across the pipe. This is also known as whole body swirl, Figure 6. Close coupled double elbows out of plane are a common cause of Type 1 swirl, along with headers, pumps and compressors. Type 2 swirl introduces two counter rotating swirls rotating in opposite directions, Figure 7. This is usually created after single elbows.
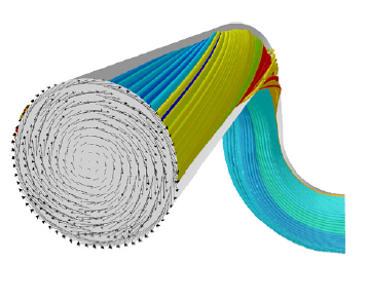
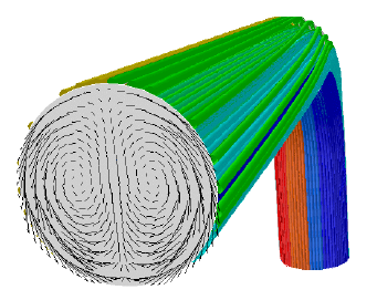
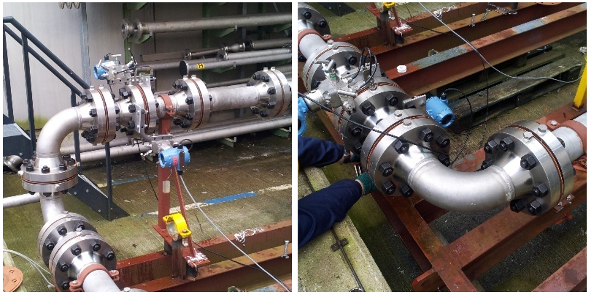
Orifice plate flow measurements
Orifice plates measurement have a century-long track record of continuous use and improvement in industrial applications. No other flow technology has the international volume of understanding and acceptance as orifice plates. Orifice plates are often described as “a hole in a plate” and often ridiculed for that simplicity. Yet it is the simplicity of an orifice plate that makes it so elegant. Leonardo da Vinci once said, “Simplicity is the ultimate sophistication”. The design of the orifice plate makes it possible to manufacture with precision and repeatability. Making one orifice plate measure the same as the next one with matching dimensions. A dimensional inspection is all that is needed to “calibrate” an orifice plate.
Knowing that two identical orifice plates will measure the same (within known uncertainties) is one of the reasons why they are the most widely used industrial flow technology even after 100 years. In today’s world, a user can replace an orifice plate and know the uncertainty of the measurement will not change, even without a flow calibration – something no other flow technology can match!
This also means that a flow calibration once done on a known orifice plate size, can be applied to all other matching orifice plates. Over the decades a massive database of traceable orifice calibrations was completed and used to create the de facto standards for orifice flow measurement. The American standards are the AGA Report No 3 and API 14.3 standards for natural measurement using an orifice plate. The international standard for orifice plates is ISO 5167.
The orifice performance in that technical database (which includes over 30,000 data points!) was tested in well-developed flow conditions. The standards confirm that measurement in matching conditions and dimensions will perform at custody transfer levels of accuracy. And since all the data points were tested in well-developed flow conditions, the standards require the same for accurate measurement.
Effect of flow disturbances on orifice measurement
If a user’s flow conditions are not well developed, with asymmetric or swirling flow, the accuracy will be affected. The effect on accuracy will depend on several factors, including the type of disturbance and the relative distance of the disturbance to the orifice location.
As the distance from the disturbance to the orifice plate increases, the flow will naturally return to a well-developed state due to the turbulence in the flow (turbulence helps us here). The distance needed to return to well-developed flow depends mostly on the type of disturbance. The AGA/API standards recommend up to 44 pipe diameters of straight pipe after double elbow to achieve well developed flow.
Shown below are two sets of flow calibration data from Mattingly and Yeh measuring three different orifice bore sizes (beta ratios) at various distances from a disturbance. Figure 8 shows single elbow effects.Figure 9 shows effects from close coupled, double elbows out of plane.
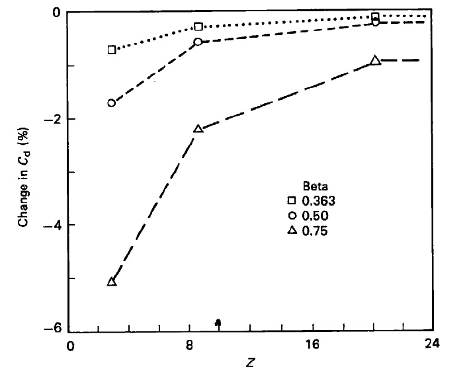
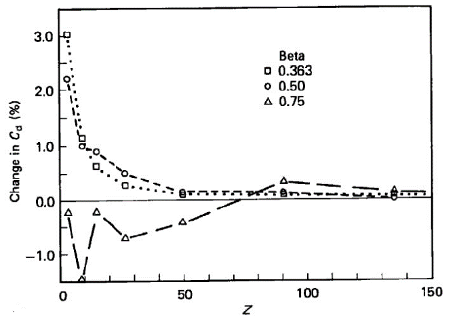
The effect of the disturbance diminishes with distance, approaching zero effect. Notice the effects on accuracy of the orifice plate measurement can be up to 5% after a single elbow using a high beta ratio. The effect lessens using smaller beta ratios. Also notice the x-axis scale of the double elbows chart is much larger than the single elbow chart. This confirms that Type 1 swirl has a much longer lasting impact on flow measurement than Type 2 swirl.
Improving flow conditions
A user can make a determination about their installation knowing the above information. They have three options available to them:
- The user could plan the measurement point as far as possible from the disturbance. The more distance means the more likely the flow is well developed at that point. Some users may have plenty of straight pipe in their system and can meet the minimum requirements in the standards. For most users, creating the necessary straight inlet piping will come with additional expense.
- The user can accept the additional uncertainty that comes with a bad installation. This might be a fine solution in applications with low accuracy requirements. But most industrial applications cannot accept accuracy shifts on the order of ±5%.
- The user could follow the most common practice in the industry: use a flow conditioner.
Flow conditioners
The user of flow conditioners is an industry best practice for ensuring optimal flow measurement with an orifice plate. Flow conditioners come in a variety of designs but have one common goal: to condition the flow to well-developed conditions ahead of an orifice flow measurement point regardless of the disturbance ahead of it.
In the AGA Report No. 3, Section 2.3.1.7 “Flow Conditioners” classifies flow conditioners into two categories: straighteners and isolating flow conditioners.
“Flow straighteners are devices that effectively remove or reduce the swirl component of a flowing stream but may have limited ability to produce the flow conditions necessary to accurately replicate the orifice plate coefficient of discharge database values. Isolating flow conditioners are devices that effectively remove the swirl component from the flowing stream while redistributing the stream to produce the flow conditions that accurately replicate the orifice plate coefficient of discharge database values.”
Flow straighteners
Flow straighteners are low blockage, swirling reducing flow conditioners. Common examples of flow straighteners are tube bundles, example shown in Figure 10 and fin-type straightening vanes, example shown in Figure 11. Tube bundles can be designed with 19 or 7 tubes concentrically grouped in the pipe. The terminology around these can be confusing as tube bundles are sometimes sold as straightening vanes, but both fall into the category of flow straightener as described in AGA 3.
These types of flow conditioners are designed to remove swirl with their elongated dimensions. But since they are low blockages, they do very little to correct he asymmetry in the flow profile. In fact, Mattingly and Yeh also showed that flow straighteners can actually make asymmetry a more persistent flow disturbance, lasting much longer in terms of distance. This is because the flow straighteners will capture the asymmetry entering each tube and reduce the type 2 swirl. By reducing the type 2 swirl, the natural turbulence is diminished and the asymmetry does not break down as quickly.
In short, flow straighteners are not recommended for orifice plate measurement.
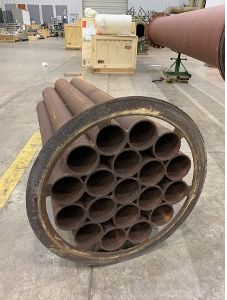

Isolating flow conditioners
Isolating flow conditioners have a blockage factor that forces the flow profile to redistribute as it passes through. This redistribution controls both the asymmetry and swirl disturbances. The design is typically a perforated plate with multiple holes designed to create a well-developed flow profile as soon as possible after the plate.
The search for the ideal pattern of holes to do this job was the subject of much research in the 1990’s as the need for flow conditioning became more and more relevant. A summary of the research from researchers such as Laws, Karnik, Zanker, Gallagher and others is fascinating but outside the scope of this paper. The most widely accepted design of this research was developed by Laws and has become known as the NOVA 50E design.
The NOVA 50E design, Figure 12, is a multi-hole flow conditioner with concentric rings of openings. 16 smaller holes around 8 midsized holes around one large central opening. The size and position of each hole is meant to stimulate the formation of a well-developed flow profile regardless of upstream disturbances. The “50” designation indicates that the plate has approximately a 50% blockage area in the flow path. The success of this design is the balance of three factors: 1) enough blockage to redistribute the flow profile, 2) large enough holes to allow passage of particles and 3) enough opening to reduce the pressure loss across the plate as much as possible. The NOVA design meets the requirements of AGA 3 Section 2.5.5 and APPENDIX 2-D.
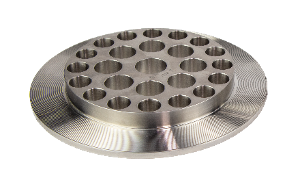
The design is universal for all flow conditions and disturbances. This advantage means a user can have one design flow conditioner for various pipeline installations and conditions. And it gives the user the assurance that most flow disturbances will be removed prior to flow measurement. For as much testing and research has been done of the effects of flow disturbances in a pipe, a user does not know the flow regime and development of their flow profile. Having a flow conditioner improves orifice plate measurement in all standard applications.
Conclusion
The use of a flow conditioner is recommended for all high accuracy orifice plate measurements. The recommended type of flow conditioner is the NOVA 50E design to remove most flow disturbances such as asymmetry and swirl. And users will benefit from the assurance that a well-designed flow conditioner will remove any unknown flow disturbances and problems that could diminish their measurement accuracy.
[1] Effects of pipe elbows and tube bundles onselected types of flowmeters, G.E. Mattingly, T.T. Yeh, Flow Measurement Instrumentation, Vol 2, January 1991
[2] US Patent 5,341,848 “Flow Conditioner”, 1994
Abstract
This paper discusses the effects of poor installations on orifice measurement and the best practices to achieve highest accuracy and performance. Flow disturbances are everywhere in pipelines and industrial applications. Knowing the types of disturbances, their effect on orifice measurement and how to correct those errors is valuable for anyone interested in accurate orifice flow measurement.
What is “Good” Flow
Most flowmeters are affected by the flow that they are trying to measure, orifice plate flowmeters included. Orifice plates measure best in “good” flow conditions and lose accuracy in “bad” conditions. There are several methods to describe and characterize good vs. bad flow conditions. When asked to describe good flow conditions, many users will use the term Laminar. This is a common yet minor misconception in flow engineering.
Laminar vs. Turbulent Flow
Laminar is a flow regime where the flow follows relatively straight lines down a pipe, Figure 1. If you were to follow a particle in the flow, it would go in a straight path and not cross paths with other particles flowing next to it. This is a regime with no turbulence. Laminar flow will happen in low flow and/or high viscous applications. In other words, the momentum forces are low and/or the viscous forces are high. Inherently this makes sense as higher velocities will encourage turbulence and higher viscosities will do the opposite.
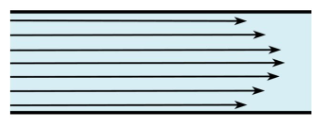
As useful tool is the Reynolds number, which is a dimensionless number used to quantify whether a flow application is in laminar flow. The Reynolds number equations is a follows:
Re=VρD/μ
Re = Reynolds number, dimensionless
V = flow velocity, ft/s
ρ = density, lbm/ft3
μ = dynamic viscosity, lbm/s·ft
The numerator of this equation combines the momentum forces in the flow, velocity, density and size. While the denominator are the inertial forces, viscosity. This follows the logic described earlier. The lower the Reynolds number, the more likely the flow regime is in a laminar state. Laminar flow is more likely to exist where the velocity, density or size is small, and/or where the viscosity is high. The commonly accepted value of laminar flow is Re < 4000. As the Reynolds number increases, the flow regime enters a transition phase between 4000 and 10,000. Above 10,000, the flow regime is considered to be turbulent.
Reynolds number - Flow regime
0 – 4,000 - Laminar
4000 – 10,000 - Transition
>10,000 - Turbulent
Turbulent flow, Figure 2, is the opposite of laminar flow in that the flow streams do not follow a straight or regular pattern. In turbulent flow the flow streams cross, small eddies occur, and mixing is more common. The word “turbulent” rightfully has negative connotations. No one wants to be on an airplane and fly through turbulence.
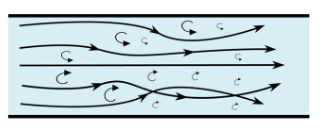
So why is Laminar the incorrect term to describe good flow? It’s not. It’s just not the world in which our flowmeters live. The vast majority of industrial pipelines are in the turbulent flow regime. Virtually all gas flows are turbulent due to the high velocities and low viscosities. Even most liquid flows are turbulent, except for some high viscosity products such as crude oil. Turbulent flow is better for orifice measurement because orifice plates were designed to measure it and their performance is well understood in those conditions.
A side note: Reynolds number is a very helpful in flow measurement. Since it is a dimensionless number, Reynolds can use a single number to describe a flow application. And that number can be used across applications. If the Reynolds number for an application is below 4000, that application is in the laminar flow regime, regardless of the size for example. Reynolds number is used when calibrating a flowmeter. Since the Reynolds number describes the flow in a single number, users can calibrate on one fluid and use the flowmeter in another fluid, knowing the performance will match at equal Reynolds numbers.
Flow profile
A better way to describe understand good vs. bad flow is the presence or absence of flow disturbances. Long, straight, unobstructed pipe will create undisturbed flow. The addition of common pipe elements will create disturbances. Common pipe elements can include single elbows, tees, two elbows in series, partially closed valves, pipe reductions or expansions, thermowells, and many more.
Just like the Reynolds number is a tool to understand the flow regime, the flow profile is a tool to visualize whether flow is disturbed or not. The flow profile attempts to show the velocity at difference points across the diameter of a flowing pipe. This can be physically measured in several ways such as with a single point Pitot tube sensor or with more complex tools such as laser doppler velocimetry. Typically, the view is across a full diameter, crossing through the midpoint of the pipe. A typical flow profile looks like Figure 3 for turbulent flow. Each arrow represents the velocity at points across a diameter of the pipe. The velocities are higher in the center of the pipe and lower near the pipe walls.
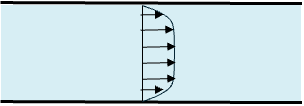
The friction on the pipe walls causes drag which slows down the fluid flow nearest to it. As the flow continues down the pipe, the next layer away from the pipe wall is slowed down slightly less. And so on until the effect of the pipe wall friction no longer affects the velocity. This is called the boundary layer effect and is created whenever flow passes over a surface. Notice the shape of the Figure 3 profile in turbulent flow is different than the shape in Figure 1. Laminar flow has a characteristic “bullet” shaped profile and turbulent has a flatter shape.
Well-developed flow is created when the boundary layer is fully established without disturbances. Put another way, well developed flow will not change its profile as it moves down the pipe. In the industrial flow measurement world, it’s also the definition of good flow and is very important in understanding flow through an orifice.
Power law estimation
When comparing whether a flow profile is well developed or not, a useful tool is the power law estimation. The power law gives a numerical estimation of a well-developed profile. The power law equation is:
u/umax = (1-r/R)1/n
u = velocity at measurement point
umax = max velocity in pipe
r = radius at measurement point
R = pipe radius
n = power
A value of n = 7 is typically used to fit the velocity profile for fully developed, turbulent flows. A higher value of n creates a flatter profile. A lower value creates a more bullet shape profile associated with laminar flow. A power law curve where
n = 7 is shown in Figure 4.
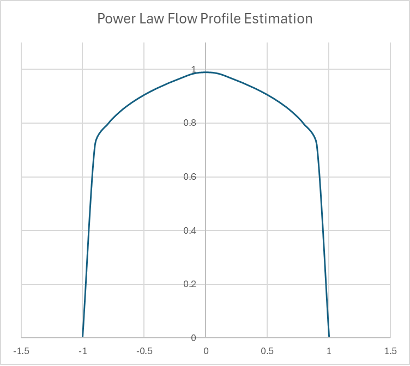
As flow is disturbed with the addition of pipe elements, the flow profile will change. For example, flow through a single elbow creates a skewed profile. The high velocity “core” of the pipe will be pushed to the opposite wall of the pipe, creating an asymmetry where the maximum velocity is no longer in the middle of the pipe. Single elbows and other elements can create asymmetry in the flow profile which is shown well in Figure 5.
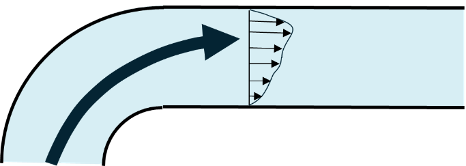
Swirling flow
The flow profile does not capture another type of flow disturbance called swirling flow. Swirling flow is when the flow has a crossflow element. Without swirl the flow will run straight down the pipe, with 0° in relation to the centerline of the pipe. If crossflow is present, the flow streams can have a swirl angle, up to 20° in severe cases.
There are two general types of swirl disturbances, Type 1 and Type 2 swirls. Type 1 swirl moves in one directional rotation across the pipe. This is also known as whole body swirl, Figure 6. Close coupled double elbows out of plane are a common cause of Type 1 swirl, along with headers, pumps and compressors. Type 2 swirl introduces two counter rotating swirls rotating in opposite directions, Figure 7. This is usually created after single elbows.
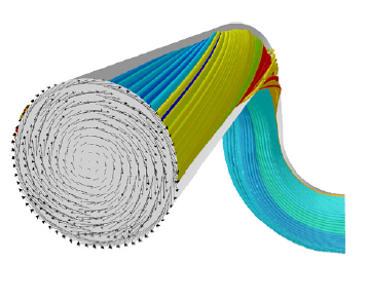
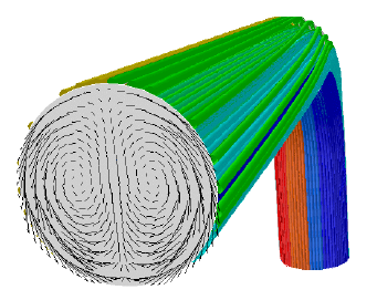
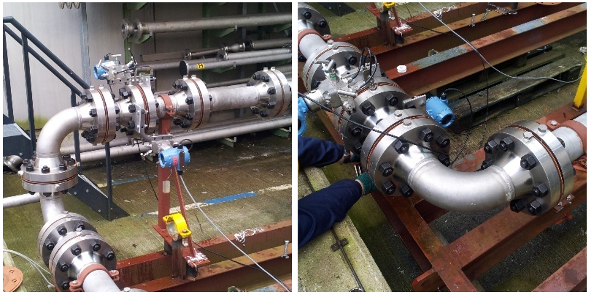
Orifice plate flow measurements
Orifice plates measurement have a century-long track record of continuous use and improvement in industrial applications. No other flow technology has the international volume of understanding and acceptance as orifice plates. Orifice plates are often described as “a hole in a plate” and often ridiculed for that simplicity. Yet it is the simplicity of an orifice plate that makes it so elegant. Leonardo da Vinci once said, “Simplicity is the ultimate sophistication”. The design of the orifice plate makes it possible to manufacture with precision and repeatability. Making one orifice plate measure the same as the next one with matching dimensions. A dimensional inspection is all that is needed to “calibrate” an orifice plate.
Knowing that two identical orifice plates will measure the same (within known uncertainties) is one of the reasons why they are the most widely used industrial flow technology even after 100 years. In today’s world, a user can replace an orifice plate and know the uncertainty of the measurement will not change, even without a flow calibration – something no other flow technology can match!
This also means that a flow calibration once done on a known orifice plate size, can be applied to all other matching orifice plates. Over the decades a massive database of traceable orifice calibrations was completed and used to create the de facto standards for orifice flow measurement. The American standards are the AGA Report No 3 and API 14.3 standards for natural measurement using an orifice plate. The international standard for orifice plates is ISO 5167.
The orifice performance in that technical database (which includes over 30,000 data points!) was tested in well-developed flow conditions. The standards confirm that measurement in matching conditions and dimensions will perform at custody transfer levels of accuracy. And since all the data points were tested in well-developed flow conditions, the standards require the same for accurate measurement.
Effect of flow disturbances on orifice measurement
If a user’s flow conditions are not well developed, with asymmetric or swirling flow, the accuracy will be affected. The effect on accuracy will depend on several factors, including the type of disturbance and the relative distance of the disturbance to the orifice location.
As the distance from the disturbance to the orifice plate increases, the flow will naturally return to a well-developed state due to the turbulence in the flow (turbulence helps us here). The distance needed to return to well-developed flow depends mostly on the type of disturbance. The AGA/API standards recommend up to 44 pipe diameters of straight pipe after double elbow to achieve well developed flow.
Shown below are two sets of flow calibration data from Mattingly and Yeh measuring three different orifice bore sizes (beta ratios) at various distances from a disturbance. Figure 8 shows single elbow effects.Figure 9 shows effects from close coupled, double elbows out of plane.
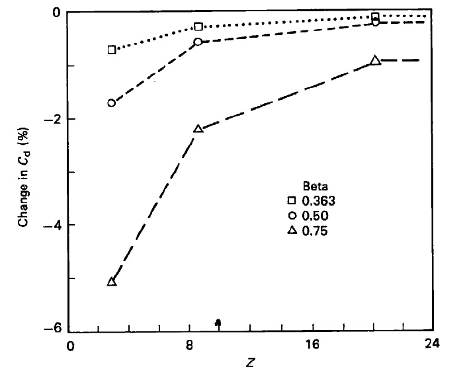
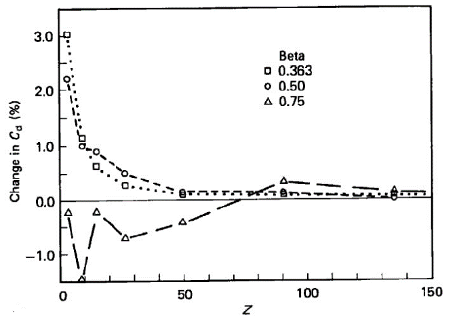
The effect of the disturbance diminishes with distance, approaching zero effect. Notice the effects on accuracy of the orifice plate measurement can be up to 5% after a single elbow using a high beta ratio. The effect lessens using smaller beta ratios. Also notice the x-axis scale of the double elbows chart is much larger than the single elbow chart. This confirms that Type 1 swirl has a much longer lasting impact on flow measurement than Type 2 swirl.
Improving flow conditions
A user can make a determination about their installation knowing the above information. They have three options available to them:
- The user could plan the measurement point as far as possible from the disturbance. The more distance means the more likely the flow is well developed at that point. Some users may have plenty of straight pipe in their system and can meet the minimum requirements in the standards. For most users, creating the necessary straight inlet piping will come with additional expense.
- The user can accept the additional uncertainty that comes with a bad installation. This might be a fine solution in applications with low accuracy requirements. But most industrial applications cannot accept accuracy shifts on the order of ±5%.
- The user could follow the most common practice in the industry: use a flow conditioner.
Flow conditioners
The user of flow conditioners is an industry best practice for ensuring optimal flow measurement with an orifice plate. Flow conditioners come in a variety of designs but have one common goal: to condition the flow to well-developed conditions ahead of an orifice flow measurement point regardless of the disturbance ahead of it.
In the AGA Report No. 3, Section 2.3.1.7 “Flow Conditioners” classifies flow conditioners into two categories: straighteners and isolating flow conditioners.
“Flow straighteners are devices that effectively remove or reduce the swirl component of a flowing stream but may have limited ability to produce the flow conditions necessary to accurately replicate the orifice plate coefficient of discharge database values. Isolating flow conditioners are devices that effectively remove the swirl component from the flowing stream while redistributing the stream to produce the flow conditions that accurately replicate the orifice plate coefficient of discharge database values.”
Flow straighteners
Flow straighteners are low blockage, swirling reducing flow conditioners. Common examples of flow straighteners are tube bundles, example shown in Figure 10 and fin-type straightening vanes, example shown in Figure 11. Tube bundles can be designed with 19 or 7 tubes concentrically grouped in the pipe. The terminology around these can be confusing as tube bundles are sometimes sold as straightening vanes, but both fall into the category of flow straightener as described in AGA 3.
These types of flow conditioners are designed to remove swirl with their elongated dimensions. But since they are low blockages, they do very little to correct he asymmetry in the flow profile. In fact, Mattingly and Yeh also showed that flow straighteners can actually make asymmetry a more persistent flow disturbance, lasting much longer in terms of distance. This is because the flow straighteners will capture the asymmetry entering each tube and reduce the type 2 swirl. By reducing the type 2 swirl, the natural turbulence is diminished and the asymmetry does not break down as quickly.
In short, flow straighteners are not recommended for orifice plate measurement.
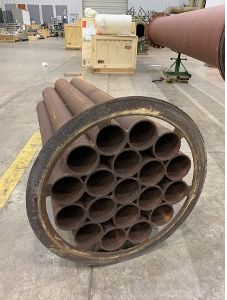

Isolating flow conditioners
Isolating flow conditioners have a blockage factor that forces the flow profile to redistribute as it passes through. This redistribution controls both the asymmetry and swirl disturbances. The design is typically a perforated plate with multiple holes designed to create a well-developed flow profile as soon as possible after the plate.
The search for the ideal pattern of holes to do this job was the subject of much research in the 1990’s as the need for flow conditioning became more and more relevant. A summary of the research from researchers such as Laws, Karnik, Zanker, Gallagher and others is fascinating but outside the scope of this paper. The most widely accepted design of this research was developed by Laws and has become known as the NOVA 50E design.
The NOVA 50E design, Figure 12, is a multi-hole flow conditioner with concentric rings of openings. 16 smaller holes around 8 midsized holes around one large central opening. The size and position of each hole is meant to stimulate the formation of a well-developed flow profile regardless of upstream disturbances. The “50” designation indicates that the plate has approximately a 50% blockage area in the flow path. The success of this design is the balance of three factors: 1) enough blockage to redistribute the flow profile, 2) large enough holes to allow passage of particles and 3) enough opening to reduce the pressure loss across the plate as much as possible. The NOVA design meets the requirements of AGA 3 Section 2.5.5 and APPENDIX 2-D.
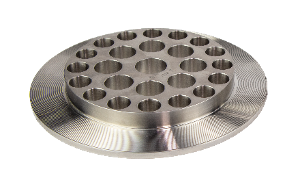
The design is universal for all flow conditions and disturbances. This advantage means a user can have one design flow conditioner for various pipeline installations and conditions. And it gives the user the assurance that most flow disturbances will be removed prior to flow measurement. For as much testing and research has been done of the effects of flow disturbances in a pipe, a user does not know the flow regime and development of their flow profile. Having a flow conditioner improves orifice plate measurement in all standard applications.
Conclusion
The use of a flow conditioner is recommended for all high accuracy orifice plate measurements. The recommended type of flow conditioner is the NOVA 50E design to remove most flow disturbances such as asymmetry and swirl. And users will benefit from the assurance that a well-designed flow conditioner will remove any unknown flow disturbances and problems that could diminish their measurement accuracy.
[1] Effects of pipe elbows and tube bundles onselected types of flowmeters, G.E. Mattingly, T.T. Yeh, Flow Measurement Instrumentation, Vol 2, January 1991
[2] US Patent 5,341,848 “Flow Conditioner”, 1994
Abstract
This paper discusses the effects of poor installations on orifice measurement and the best practices to achieve highest accuracy and performance. Flow disturbances are everywhere in pipelines and industrial applications. Knowing the types of disturbances, their effect on orifice measurement and how to correct those errors is valuable for anyone interested in accurate orifice flow measurement.
What is “Good” Flow
Most flowmeters are affected by the flow that they are trying to measure, orifice plate flowmeters included. Orifice plates measure best in “good” flow conditions and lose accuracy in “bad” conditions. There are several methods to describe and characterize good vs. bad flow conditions. When asked to describe good flow conditions, many users will use the term Laminar. This is a common yet minor misconception in flow engineering.
Laminar vs. Turbulent Flow
Laminar is a flow regime where the flow follows relatively straight lines down a pipe, Figure 1. If you were to follow a particle in the flow, it would go in a straight path and not cross paths with other particles flowing next to it. This is a regime with no turbulence. Laminar flow will happen in low flow and/or high viscous applications. In other words, the momentum forces are low and/or the viscous forces are high. Inherently this makes sense as higher velocities will encourage turbulence and higher viscosities will do the opposite.
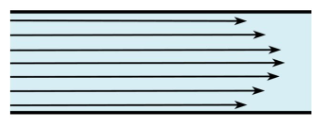
As useful tool is the Reynolds number, which is a dimensionless number used to quantify whether a flow application is in laminar flow. The Reynolds number equations is a follows:
Re=VρD/μ
Re = Reynolds number, dimensionless
V = flow velocity, ft/s
ρ = density, lbm/ft3
μ = dynamic viscosity, lbm/s·ft
The numerator of this equation combines the momentum forces in the flow, velocity, density and size. While the denominator are the inertial forces, viscosity. This follows the logic described earlier. The lower the Reynolds number, the more likely the flow regime is in a laminar state. Laminar flow is more likely to exist where the velocity, density or size is small, and/or where the viscosity is high. The commonly accepted value of laminar flow is Re < 4000. As the Reynolds number increases, the flow regime enters a transition phase between 4000 and 10,000. Above 10,000, the flow regime is considered to be turbulent.
Reynolds number - Flow regime
0 – 4,000 - Laminar
4000 – 10,000 - Transition
>10,000 - Turbulent
Turbulent flow, Figure 2, is the opposite of laminar flow in that the flow streams do not follow a straight or regular pattern. In turbulent flow the flow streams cross, small eddies occur, and mixing is more common. The word “turbulent” rightfully has negative connotations. No one wants to be on an airplane and fly through turbulence.
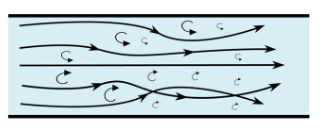
So why is Laminar the incorrect term to describe good flow? It’s not. It’s just not the world in which our flowmeters live. The vast majority of industrial pipelines are in the turbulent flow regime. Virtually all gas flows are turbulent due to the high velocities and low viscosities. Even most liquid flows are turbulent, except for some high viscosity products such as crude oil. Turbulent flow is better for orifice measurement because orifice plates were designed to measure it and their performance is well understood in those conditions.
A side note: Reynolds number is a very helpful in flow measurement. Since it is a dimensionless number, Reynolds can use a single number to describe a flow application. And that number can be used across applications. If the Reynolds number for an application is below 4000, that application is in the laminar flow regime, regardless of the size for example. Reynolds number is used when calibrating a flowmeter. Since the Reynolds number describes the flow in a single number, users can calibrate on one fluid and use the flowmeter in another fluid, knowing the performance will match at equal Reynolds numbers.
Flow profile
A better way to describe understand good vs. bad flow is the presence or absence of flow disturbances. Long, straight, unobstructed pipe will create undisturbed flow. The addition of common pipe elements will create disturbances. Common pipe elements can include single elbows, tees, two elbows in series, partially closed valves, pipe reductions or expansions, thermowells, and many more.
Just like the Reynolds number is a tool to understand the flow regime, the flow profile is a tool to visualize whether flow is disturbed or not. The flow profile attempts to show the velocity at difference points across the diameter of a flowing pipe. This can be physically measured in several ways such as with a single point Pitot tube sensor or with more complex tools such as laser doppler velocimetry. Typically, the view is across a full diameter, crossing through the midpoint of the pipe. A typical flow profile looks like Figure 3 for turbulent flow. Each arrow represents the velocity at points across a diameter of the pipe. The velocities are higher in the center of the pipe and lower near the pipe walls.
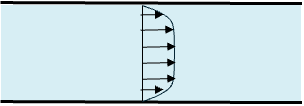
The friction on the pipe walls causes drag which slows down the fluid flow nearest to it. As the flow continues down the pipe, the next layer away from the pipe wall is slowed down slightly less. And so on until the effect of the pipe wall friction no longer affects the velocity. This is called the boundary layer effect and is created whenever flow passes over a surface. Notice the shape of the Figure 3 profile in turbulent flow is different than the shape in Figure 1. Laminar flow has a characteristic “bullet” shaped profile and turbulent has a flatter shape.
Well-developed flow is created when the boundary layer is fully established without disturbances. Put another way, well developed flow will not change its profile as it moves down the pipe. In the industrial flow measurement world, it’s also the definition of good flow and is very important in understanding flow through an orifice.
Power law estimation
When comparing whether a flow profile is well developed or not, a useful tool is the power law estimation. The power law gives a numerical estimation of a well-developed profile. The power law equation is:
u/umax = (1-r/R)1/n
u = velocity at measurement point
umax = max velocity in pipe
r = radius at measurement point
R = pipe radius
n = power
A value of n = 7 is typically used to fit the velocity profile for fully developed, turbulent flows. A higher value of n creates a flatter profile. A lower value creates a more bullet shape profile associated with laminar flow. A power law curve where
n = 7 is shown in Figure 4.
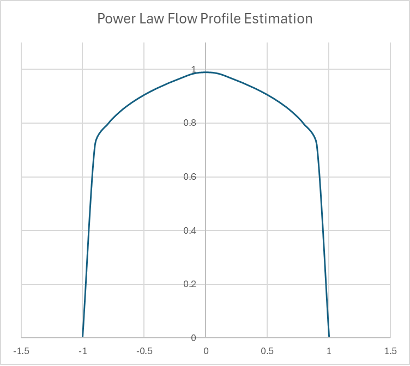
As flow is disturbed with the addition of pipe elements, the flow profile will change. For example, flow through a single elbow creates a skewed profile. The high velocity “core” of the pipe will be pushed to the opposite wall of the pipe, creating an asymmetry where the maximum velocity is no longer in the middle of the pipe. Single elbows and other elements can create asymmetry in the flow profile which is shown well in Figure 5.
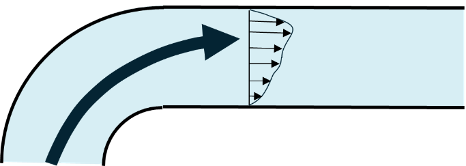
Swirling flow
The flow profile does not capture another type of flow disturbance called swirling flow. Swirling flow is when the flow has a crossflow element. Without swirl the flow will run straight down the pipe, with 0° in relation to the centerline of the pipe. If crossflow is present, the flow streams can have a swirl angle, up to 20° in severe cases.
There are two general types of swirl disturbances, Type 1 and Type 2 swirls. Type 1 swirl moves in one directional rotation across the pipe. This is also known as whole body swirl, Figure 6. Close coupled double elbows out of plane are a common cause of Type 1 swirl, along with headers, pumps and compressors. Type 2 swirl introduces two counter rotating swirls rotating in opposite directions, Figure 7. This is usually created after single elbows.
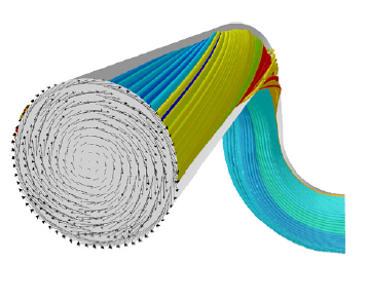
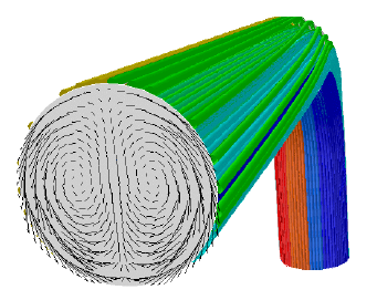
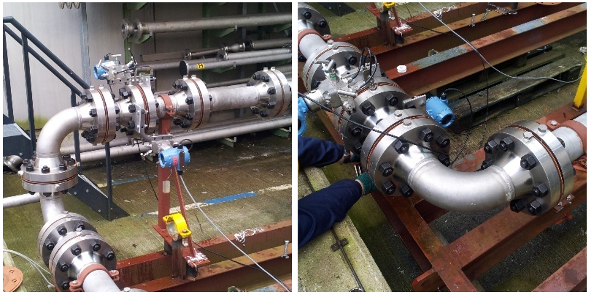
Orifice plate flow measurements
Orifice plates measurement have a century-long track record of continuous use and improvement in industrial applications. No other flow technology has the international volume of understanding and acceptance as orifice plates. Orifice plates are often described as “a hole in a plate” and often ridiculed for that simplicity. Yet it is the simplicity of an orifice plate that makes it so elegant. Leonardo da Vinci once said, “Simplicity is the ultimate sophistication”. The design of the orifice plate makes it possible to manufacture with precision and repeatability. Making one orifice plate measure the same as the next one with matching dimensions. A dimensional inspection is all that is needed to “calibrate” an orifice plate.
Knowing that two identical orifice plates will measure the same (within known uncertainties) is one of the reasons why they are the most widely used industrial flow technology even after 100 years. In today’s world, a user can replace an orifice plate and know the uncertainty of the measurement will not change, even without a flow calibration – something no other flow technology can match!
This also means that a flow calibration once done on a known orifice plate size, can be applied to all other matching orifice plates. Over the decades a massive database of traceable orifice calibrations was completed and used to create the de facto standards for orifice flow measurement. The American standards are the AGA Report No 3 and API 14.3 standards for natural measurement using an orifice plate. The international standard for orifice plates is ISO 5167.
The orifice performance in that technical database (which includes over 30,000 data points!) was tested in well-developed flow conditions. The standards confirm that measurement in matching conditions and dimensions will perform at custody transfer levels of accuracy. And since all the data points were tested in well-developed flow conditions, the standards require the same for accurate measurement.
Effect of flow disturbances on orifice measurement
If a user’s flow conditions are not well developed, with asymmetric or swirling flow, the accuracy will be affected. The effect on accuracy will depend on several factors, including the type of disturbance and the relative distance of the disturbance to the orifice location.
As the distance from the disturbance to the orifice plate increases, the flow will naturally return to a well-developed state due to the turbulence in the flow (turbulence helps us here). The distance needed to return to well-developed flow depends mostly on the type of disturbance. The AGA/API standards recommend up to 44 pipe diameters of straight pipe after double elbow to achieve well developed flow.
Shown below are two sets of flow calibration data from Mattingly and Yeh measuring three different orifice bore sizes (beta ratios) at various distances from a disturbance. Figure 8 shows single elbow effects.Figure 9 shows effects from close coupled, double elbows out of plane.
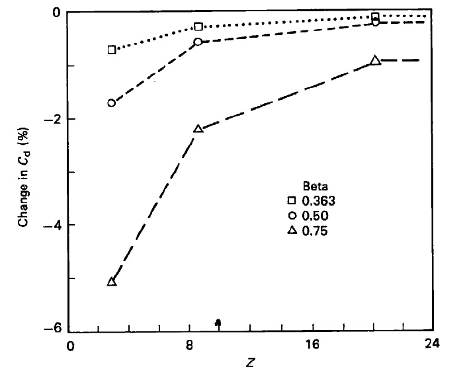
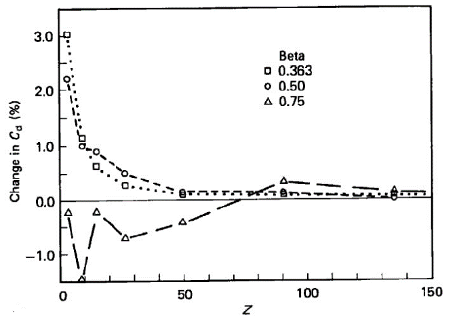
The effect of the disturbance diminishes with distance, approaching zero effect. Notice the effects on accuracy of the orifice plate measurement can be up to 5% after a single elbow using a high beta ratio. The effect lessens using smaller beta ratios. Also notice the x-axis scale of the double elbows chart is much larger than the single elbow chart. This confirms that Type 1 swirl has a much longer lasting impact on flow measurement than Type 2 swirl.
Improving flow conditions
A user can make a determination about their installation knowing the above information. They have three options available to them:
- The user could plan the measurement point as far as possible from the disturbance. The more distance means the more likely the flow is well developed at that point. Some users may have plenty of straight pipe in their system and can meet the minimum requirements in the standards. For most users, creating the necessary straight inlet piping will come with additional expense.
- The user can accept the additional uncertainty that comes with a bad installation. This might be a fine solution in applications with low accuracy requirements. But most industrial applications cannot accept accuracy shifts on the order of ±5%.
- The user could follow the most common practice in the industry: use a flow conditioner.
Flow conditioners
The user of flow conditioners is an industry best practice for ensuring optimal flow measurement with an orifice plate. Flow conditioners come in a variety of designs but have one common goal: to condition the flow to well-developed conditions ahead of an orifice flow measurement point regardless of the disturbance ahead of it.
In the AGA Report No. 3, Section 2.3.1.7 “Flow Conditioners” classifies flow conditioners into two categories: straighteners and isolating flow conditioners.
“Flow straighteners are devices that effectively remove or reduce the swirl component of a flowing stream but may have limited ability to produce the flow conditions necessary to accurately replicate the orifice plate coefficient of discharge database values. Isolating flow conditioners are devices that effectively remove the swirl component from the flowing stream while redistributing the stream to produce the flow conditions that accurately replicate the orifice plate coefficient of discharge database values.”
Flow straighteners
Flow straighteners are low blockage, swirling reducing flow conditioners. Common examples of flow straighteners are tube bundles, example shown in Figure 10 and fin-type straightening vanes, example shown in Figure 11. Tube bundles can be designed with 19 or 7 tubes concentrically grouped in the pipe. The terminology around these can be confusing as tube bundles are sometimes sold as straightening vanes, but both fall into the category of flow straightener as described in AGA 3.
These types of flow conditioners are designed to remove swirl with their elongated dimensions. But since they are low blockages, they do very little to correct he asymmetry in the flow profile. In fact, Mattingly and Yeh also showed that flow straighteners can actually make asymmetry a more persistent flow disturbance, lasting much longer in terms of distance. This is because the flow straighteners will capture the asymmetry entering each tube and reduce the type 2 swirl. By reducing the type 2 swirl, the natural turbulence is diminished and the asymmetry does not break down as quickly.
In short, flow straighteners are not recommended for orifice plate measurement.
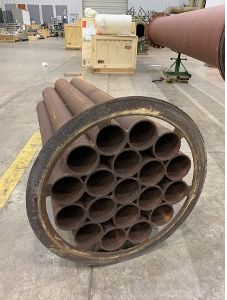

Isolating flow conditioners
Isolating flow conditioners have a blockage factor that forces the flow profile to redistribute as it passes through. This redistribution controls both the asymmetry and swirl disturbances. The design is typically a perforated plate with multiple holes designed to create a well-developed flow profile as soon as possible after the plate.
The search for the ideal pattern of holes to do this job was the subject of much research in the 1990’s as the need for flow conditioning became more and more relevant. A summary of the research from researchers such as Laws, Karnik, Zanker, Gallagher and others is fascinating but outside the scope of this paper. The most widely accepted design of this research was developed by Laws and has become known as the NOVA 50E design.
The NOVA 50E design, Figure 12, is a multi-hole flow conditioner with concentric rings of openings. 16 smaller holes around 8 midsized holes around one large central opening. The size and position of each hole is meant to stimulate the formation of a well-developed flow profile regardless of upstream disturbances. The “50” designation indicates that the plate has approximately a 50% blockage area in the flow path. The success of this design is the balance of three factors: 1) enough blockage to redistribute the flow profile, 2) large enough holes to allow passage of particles and 3) enough opening to reduce the pressure loss across the plate as much as possible. The NOVA design meets the requirements of AGA 3 Section 2.5.5 and APPENDIX 2-D.
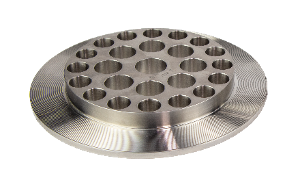
The design is universal for all flow conditions and disturbances. This advantage means a user can have one design flow conditioner for various pipeline installations and conditions. And it gives the user the assurance that most flow disturbances will be removed prior to flow measurement. For as much testing and research has been done of the effects of flow disturbances in a pipe, a user does not know the flow regime and development of their flow profile. Having a flow conditioner improves orifice plate measurement in all standard applications.
Conclusion
The use of a flow conditioner is recommended for all high accuracy orifice plate measurements. The recommended type of flow conditioner is the NOVA 50E design to remove most flow disturbances such as asymmetry and swirl. And users will benefit from the assurance that a well-designed flow conditioner will remove any unknown flow disturbances and problems that could diminish their measurement accuracy.
[1] Effects of pipe elbows and tube bundles onselected types of flowmeters, G.E. Mattingly, T.T. Yeh, Flow Measurement Instrumentation, Vol 2, January 1991
[2] US Patent 5,341,848 “Flow Conditioner”, 1994
Abstract
This paper discusses the effects of poor installations on orifice measurement and the best practices to achieve highest accuracy and performance. Flow disturbances are everywhere in pipelines and industrial applications. Knowing the types of disturbances, their effect on orifice measurement and how to correct those errors is valuable for anyone interested in accurate orifice flow measurement.
What is “Good” Flow
Most flowmeters are affected by the flow that they are trying to measure, orifice plate flowmeters included. Orifice plates measure best in “good” flow conditions and lose accuracy in “bad” conditions. There are several methods to describe and characterize good vs. bad flow conditions. When asked to describe good flow conditions, many users will use the term Laminar. This is a common yet minor misconception in flow engineering.
Laminar vs. Turbulent Flow
Laminar is a flow regime where the flow follows relatively straight lines down a pipe, Figure 1. If you were to follow a particle in the flow, it would go in a straight path and not cross paths with other particles flowing next to it. This is a regime with no turbulence. Laminar flow will happen in low flow and/or high viscous applications. In other words, the momentum forces are low and/or the viscous forces are high. Inherently this makes sense as higher velocities will encourage turbulence and higher viscosities will do the opposite.
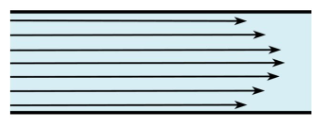
As useful tool is the Reynolds number, which is a dimensionless number used to quantify whether a flow application is in laminar flow. The Reynolds number equations is a follows:
Re=VρD/μ
Re = Reynolds number, dimensionless
V = flow velocity, ft/s
ρ = density, lbm/ft3
μ = dynamic viscosity, lbm/s·ft
The numerator of this equation combines the momentum forces in the flow, velocity, density and size. While the denominator are the inertial forces, viscosity. This follows the logic described earlier. The lower the Reynolds number, the more likely the flow regime is in a laminar state. Laminar flow is more likely to exist where the velocity, density or size is small, and/or where the viscosity is high. The commonly accepted value of laminar flow is Re < 4000. As the Reynolds number increases, the flow regime enters a transition phase between 4000 and 10,000. Above 10,000, the flow regime is considered to be turbulent.
Reynolds number - Flow regime
0 – 4,000 - Laminar
4000 – 10,000 - Transition
>10,000 - Turbulent
Turbulent flow, Figure 2, is the opposite of laminar flow in that the flow streams do not follow a straight or regular pattern. In turbulent flow the flow streams cross, small eddies occur, and mixing is more common. The word “turbulent” rightfully has negative connotations. No one wants to be on an airplane and fly through turbulence.
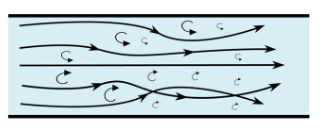
So why is Laminar the incorrect term to describe good flow? It’s not. It’s just not the world in which our flowmeters live. The vast majority of industrial pipelines are in the turbulent flow regime. Virtually all gas flows are turbulent due to the high velocities and low viscosities. Even most liquid flows are turbulent, except for some high viscosity products such as crude oil. Turbulent flow is better for orifice measurement because orifice plates were designed to measure it and their performance is well understood in those conditions.
A side note: Reynolds number is a very helpful in flow measurement. Since it is a dimensionless number, Reynolds can use a single number to describe a flow application. And that number can be used across applications. If the Reynolds number for an application is below 4000, that application is in the laminar flow regime, regardless of the size for example. Reynolds number is used when calibrating a flowmeter. Since the Reynolds number describes the flow in a single number, users can calibrate on one fluid and use the flowmeter in another fluid, knowing the performance will match at equal Reynolds numbers.
Flow profile
A better way to describe understand good vs. bad flow is the presence or absence of flow disturbances. Long, straight, unobstructed pipe will create undisturbed flow. The addition of common pipe elements will create disturbances. Common pipe elements can include single elbows, tees, two elbows in series, partially closed valves, pipe reductions or expansions, thermowells, and many more.
Just like the Reynolds number is a tool to understand the flow regime, the flow profile is a tool to visualize whether flow is disturbed or not. The flow profile attempts to show the velocity at difference points across the diameter of a flowing pipe. This can be physically measured in several ways such as with a single point Pitot tube sensor or with more complex tools such as laser doppler velocimetry. Typically, the view is across a full diameter, crossing through the midpoint of the pipe. A typical flow profile looks like Figure 3 for turbulent flow. Each arrow represents the velocity at points across a diameter of the pipe. The velocities are higher in the center of the pipe and lower near the pipe walls.
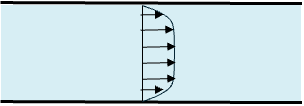
The friction on the pipe walls causes drag which slows down the fluid flow nearest to it. As the flow continues down the pipe, the next layer away from the pipe wall is slowed down slightly less. And so on until the effect of the pipe wall friction no longer affects the velocity. This is called the boundary layer effect and is created whenever flow passes over a surface. Notice the shape of the Figure 3 profile in turbulent flow is different than the shape in Figure 1. Laminar flow has a characteristic “bullet” shaped profile and turbulent has a flatter shape.
Well-developed flow is created when the boundary layer is fully established without disturbances. Put another way, well developed flow will not change its profile as it moves down the pipe. In the industrial flow measurement world, it’s also the definition of good flow and is very important in understanding flow through an orifice.
Power law estimation
When comparing whether a flow profile is well developed or not, a useful tool is the power law estimation. The power law gives a numerical estimation of a well-developed profile. The power law equation is:
u/umax = (1-r/R)1/n
u = velocity at measurement point
umax = max velocity in pipe
r = radius at measurement point
R = pipe radius
n = power
A value of n = 7 is typically used to fit the velocity profile for fully developed, turbulent flows. A higher value of n creates a flatter profile. A lower value creates a more bullet shape profile associated with laminar flow. A power law curve where
n = 7 is shown in Figure 4.
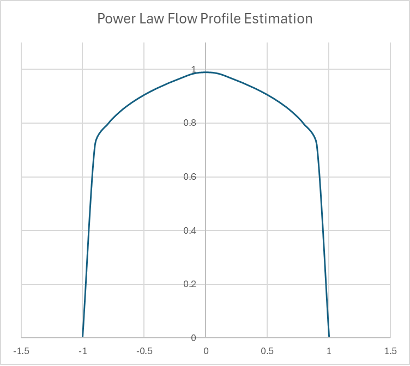
As flow is disturbed with the addition of pipe elements, the flow profile will change. For example, flow through a single elbow creates a skewed profile. The high velocity “core” of the pipe will be pushed to the opposite wall of the pipe, creating an asymmetry where the maximum velocity is no longer in the middle of the pipe. Single elbows and other elements can create asymmetry in the flow profile which is shown well in Figure 5.
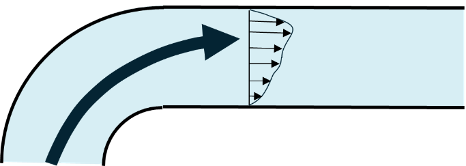
Swirling flow
The flow profile does not capture another type of flow disturbance called swirling flow. Swirling flow is when the flow has a crossflow element. Without swirl the flow will run straight down the pipe, with 0° in relation to the centerline of the pipe. If crossflow is present, the flow streams can have a swirl angle, up to 20° in severe cases.
There are two general types of swirl disturbances, Type 1 and Type 2 swirls. Type 1 swirl moves in one directional rotation across the pipe. This is also known as whole body swirl, Figure 6. Close coupled double elbows out of plane are a common cause of Type 1 swirl, along with headers, pumps and compressors. Type 2 swirl introduces two counter rotating swirls rotating in opposite directions, Figure 7. This is usually created after single elbows.
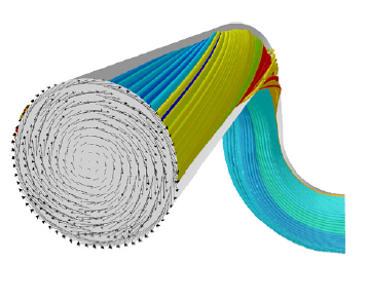
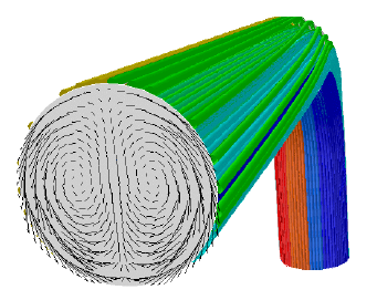
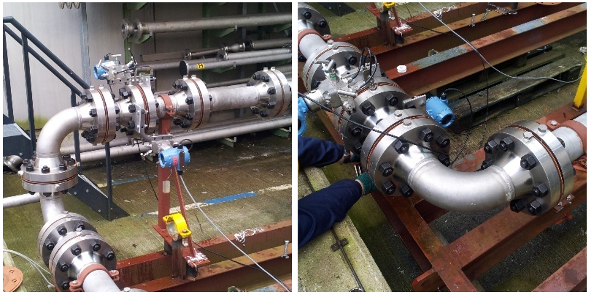
Orifice plate flow measurements
Orifice plates measurement have a century-long track record of continuous use and improvement in industrial applications. No other flow technology has the international volume of understanding and acceptance as orifice plates. Orifice plates are often described as “a hole in a plate” and often ridiculed for that simplicity. Yet it is the simplicity of an orifice plate that makes it so elegant. Leonardo da Vinci once said, “Simplicity is the ultimate sophistication”. The design of the orifice plate makes it possible to manufacture with precision and repeatability. Making one orifice plate measure the same as the next one with matching dimensions. A dimensional inspection is all that is needed to “calibrate” an orifice plate.
Knowing that two identical orifice plates will measure the same (within known uncertainties) is one of the reasons why they are the most widely used industrial flow technology even after 100 years. In today’s world, a user can replace an orifice plate and know the uncertainty of the measurement will not change, even without a flow calibration – something no other flow technology can match!
This also means that a flow calibration once done on a known orifice plate size, can be applied to all other matching orifice plates. Over the decades a massive database of traceable orifice calibrations was completed and used to create the de facto standards for orifice flow measurement. The American standards are the AGA Report No 3 and API 14.3 standards for natural measurement using an orifice plate. The international standard for orifice plates is ISO 5167.
The orifice performance in that technical database (which includes over 30,000 data points!) was tested in well-developed flow conditions. The standards confirm that measurement in matching conditions and dimensions will perform at custody transfer levels of accuracy. And since all the data points were tested in well-developed flow conditions, the standards require the same for accurate measurement.
Effect of flow disturbances on orifice measurement
If a user’s flow conditions are not well developed, with asymmetric or swirling flow, the accuracy will be affected. The effect on accuracy will depend on several factors, including the type of disturbance and the relative distance of the disturbance to the orifice location.
As the distance from the disturbance to the orifice plate increases, the flow will naturally return to a well-developed state due to the turbulence in the flow (turbulence helps us here). The distance needed to return to well-developed flow depends mostly on the type of disturbance. The AGA/API standards recommend up to 44 pipe diameters of straight pipe after double elbow to achieve well developed flow.
Shown below are two sets of flow calibration data from Mattingly and Yeh measuring three different orifice bore sizes (beta ratios) at various distances from a disturbance. Figure 8 shows single elbow effects.Figure 9 shows effects from close coupled, double elbows out of plane.
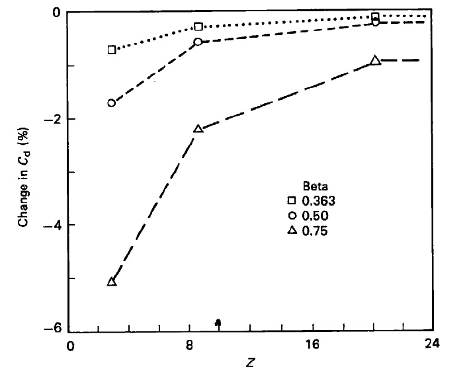
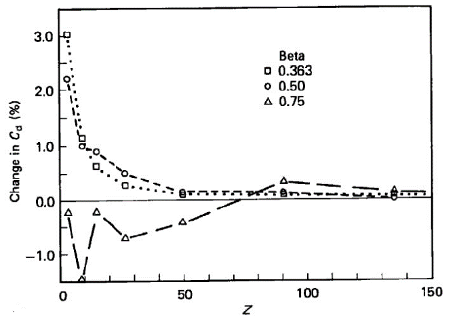
The effect of the disturbance diminishes with distance, approaching zero effect. Notice the effects on accuracy of the orifice plate measurement can be up to 5% after a single elbow using a high beta ratio. The effect lessens using smaller beta ratios. Also notice the x-axis scale of the double elbows chart is much larger than the single elbow chart. This confirms that Type 1 swirl has a much longer lasting impact on flow measurement than Type 2 swirl.
Improving flow conditions
A user can make a determination about their installation knowing the above information. They have three options available to them:
- The user could plan the measurement point as far as possible from the disturbance. The more distance means the more likely the flow is well developed at that point. Some users may have plenty of straight pipe in their system and can meet the minimum requirements in the standards. For most users, creating the necessary straight inlet piping will come with additional expense.
- The user can accept the additional uncertainty that comes with a bad installation. This might be a fine solution in applications with low accuracy requirements. But most industrial applications cannot accept accuracy shifts on the order of ±5%.
- The user could follow the most common practice in the industry: use a flow conditioner.
Flow conditioners
The user of flow conditioners is an industry best practice for ensuring optimal flow measurement with an orifice plate. Flow conditioners come in a variety of designs but have one common goal: to condition the flow to well-developed conditions ahead of an orifice flow measurement point regardless of the disturbance ahead of it.
In the AGA Report No. 3, Section 2.3.1.7 “Flow Conditioners” classifies flow conditioners into two categories: straighteners and isolating flow conditioners.
“Flow straighteners are devices that effectively remove or reduce the swirl component of a flowing stream but may have limited ability to produce the flow conditions necessary to accurately replicate the orifice plate coefficient of discharge database values. Isolating flow conditioners are devices that effectively remove the swirl component from the flowing stream while redistributing the stream to produce the flow conditions that accurately replicate the orifice plate coefficient of discharge database values.”
Flow straighteners
Flow straighteners are low blockage, swirling reducing flow conditioners. Common examples of flow straighteners are tube bundles, example shown in Figure 10 and fin-type straightening vanes, example shown in Figure 11. Tube bundles can be designed with 19 or 7 tubes concentrically grouped in the pipe. The terminology around these can be confusing as tube bundles are sometimes sold as straightening vanes, but both fall into the category of flow straightener as described in AGA 3.
These types of flow conditioners are designed to remove swirl with their elongated dimensions. But since they are low blockages, they do very little to correct he asymmetry in the flow profile. In fact, Mattingly and Yeh also showed that flow straighteners can actually make asymmetry a more persistent flow disturbance, lasting much longer in terms of distance. This is because the flow straighteners will capture the asymmetry entering each tube and reduce the type 2 swirl. By reducing the type 2 swirl, the natural turbulence is diminished and the asymmetry does not break down as quickly.
In short, flow straighteners are not recommended for orifice plate measurement.
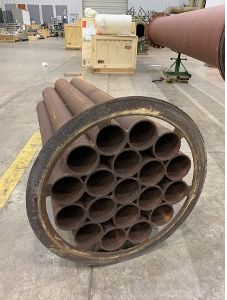

Isolating flow conditioners
Isolating flow conditioners have a blockage factor that forces the flow profile to redistribute as it passes through. This redistribution controls both the asymmetry and swirl disturbances. The design is typically a perforated plate with multiple holes designed to create a well-developed flow profile as soon as possible after the plate.
The search for the ideal pattern of holes to do this job was the subject of much research in the 1990’s as the need for flow conditioning became more and more relevant. A summary of the research from researchers such as Laws, Karnik, Zanker, Gallagher and others is fascinating but outside the scope of this paper. The most widely accepted design of this research was developed by Laws and has become known as the NOVA 50E design.
The NOVA 50E design, Figure 12, is a multi-hole flow conditioner with concentric rings of openings. 16 smaller holes around 8 midsized holes around one large central opening. The size and position of each hole is meant to stimulate the formation of a well-developed flow profile regardless of upstream disturbances. The “50” designation indicates that the plate has approximately a 50% blockage area in the flow path. The success of this design is the balance of three factors: 1) enough blockage to redistribute the flow profile, 2) large enough holes to allow passage of particles and 3) enough opening to reduce the pressure loss across the plate as much as possible. The NOVA design meets the requirements of AGA 3 Section 2.5.5 and APPENDIX 2-D.
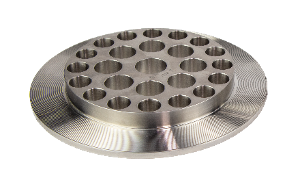
The design is universal for all flow conditions and disturbances. This advantage means a user can have one design flow conditioner for various pipeline installations and conditions. And it gives the user the assurance that most flow disturbances will be removed prior to flow measurement. For as much testing and research has been done of the effects of flow disturbances in a pipe, a user does not know the flow regime and development of their flow profile. Having a flow conditioner improves orifice plate measurement in all standard applications.
Conclusion
The use of a flow conditioner is recommended for all high accuracy orifice plate measurements. The recommended type of flow conditioner is the NOVA 50E design to remove most flow disturbances such as asymmetry and swirl. And users will benefit from the assurance that a well-designed flow conditioner will remove any unknown flow disturbances and problems that could diminish their measurement accuracy.
[1] Effects of pipe elbows and tube bundles onselected types of flowmeters, G.E. Mattingly, T.T. Yeh, Flow Measurement Instrumentation, Vol 2, January 1991
[2] US Patent 5,341,848 “Flow Conditioner”, 1994
Abstract
This paper discusses the effects of poor installations on orifice measurement and the best practices to achieve highest accuracy and performance. Flow disturbances are everywhere in pipelines and industrial applications. Knowing the types of disturbances, their effect on orifice measurement and how to correct those errors is valuable for anyone interested in accurate orifice flow measurement.
What is “Good” Flow
Most flowmeters are affected by the flow that they are trying to measure, orifice plate flowmeters included. Orifice plates measure best in “good” flow conditions and lose accuracy in “bad” conditions. There are several methods to describe and characterize good vs. bad flow conditions. When asked to describe good flow conditions, many users will use the term Laminar. This is a common yet minor misconception in flow engineering.
Laminar vs. Turbulent Flow
Laminar is a flow regime where the flow follows relatively straight lines down a pipe, Figure 1. If you were to follow a particle in the flow, it would go in a straight path and not cross paths with other particles flowing next to it. This is a regime with no turbulence. Laminar flow will happen in low flow and/or high viscous applications. In other words, the momentum forces are low and/or the viscous forces are high. Inherently this makes sense as higher velocities will encourage turbulence and higher viscosities will do the opposite.
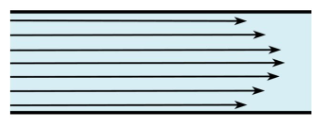
As useful tool is the Reynolds number, which is a dimensionless number used to quantify whether a flow application is in laminar flow. The Reynolds number equations is a follows:
Re=VρD/μ
Re = Reynolds number, dimensionless
V = flow velocity, ft/s
ρ = density, lbm/ft3
μ = dynamic viscosity, lbm/s·ft
The numerator of this equation combines the momentum forces in the flow, velocity, density and size. While the denominator are the inertial forces, viscosity. This follows the logic described earlier. The lower the Reynolds number, the more likely the flow regime is in a laminar state. Laminar flow is more likely to exist where the velocity, density or size is small, and/or where the viscosity is high. The commonly accepted value of laminar flow is Re < 4000. As the Reynolds number increases, the flow regime enters a transition phase between 4000 and 10,000. Above 10,000, the flow regime is considered to be turbulent.
Reynolds number - Flow regime
0 – 4,000 - Laminar
4000 – 10,000 - Transition
>10,000 - Turbulent
Turbulent flow, Figure 2, is the opposite of laminar flow in that the flow streams do not follow a straight or regular pattern. In turbulent flow the flow streams cross, small eddies occur, and mixing is more common. The word “turbulent” rightfully has negative connotations. No one wants to be on an airplane and fly through turbulence.
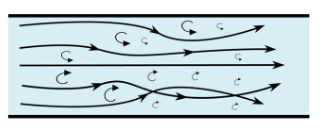
So why is Laminar the incorrect term to describe good flow? It’s not. It’s just not the world in which our flowmeters live. The vast majority of industrial pipelines are in the turbulent flow regime. Virtually all gas flows are turbulent due to the high velocities and low viscosities. Even most liquid flows are turbulent, except for some high viscosity products such as crude oil. Turbulent flow is better for orifice measurement because orifice plates were designed to measure it and their performance is well understood in those conditions.
A side note: Reynolds number is a very helpful in flow measurement. Since it is a dimensionless number, Reynolds can use a single number to describe a flow application. And that number can be used across applications. If the Reynolds number for an application is below 4000, that application is in the laminar flow regime, regardless of the size for example. Reynolds number is used when calibrating a flowmeter. Since the Reynolds number describes the flow in a single number, users can calibrate on one fluid and use the flowmeter in another fluid, knowing the performance will match at equal Reynolds numbers.
Flow profile
A better way to describe understand good vs. bad flow is the presence or absence of flow disturbances. Long, straight, unobstructed pipe will create undisturbed flow. The addition of common pipe elements will create disturbances. Common pipe elements can include single elbows, tees, two elbows in series, partially closed valves, pipe reductions or expansions, thermowells, and many more.
Just like the Reynolds number is a tool to understand the flow regime, the flow profile is a tool to visualize whether flow is disturbed or not. The flow profile attempts to show the velocity at difference points across the diameter of a flowing pipe. This can be physically measured in several ways such as with a single point Pitot tube sensor or with more complex tools such as laser doppler velocimetry. Typically, the view is across a full diameter, crossing through the midpoint of the pipe. A typical flow profile looks like Figure 3 for turbulent flow. Each arrow represents the velocity at points across a diameter of the pipe. The velocities are higher in the center of the pipe and lower near the pipe walls.
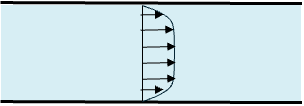
The friction on the pipe walls causes drag which slows down the fluid flow nearest to it. As the flow continues down the pipe, the next layer away from the pipe wall is slowed down slightly less. And so on until the effect of the pipe wall friction no longer affects the velocity. This is called the boundary layer effect and is created whenever flow passes over a surface. Notice the shape of the Figure 3 profile in turbulent flow is different than the shape in Figure 1. Laminar flow has a characteristic “bullet” shaped profile and turbulent has a flatter shape.
Well-developed flow is created when the boundary layer is fully established without disturbances. Put another way, well developed flow will not change its profile as it moves down the pipe. In the industrial flow measurement world, it’s also the definition of good flow and is very important in understanding flow through an orifice.
Power law estimation
When comparing whether a flow profile is well developed or not, a useful tool is the power law estimation. The power law gives a numerical estimation of a well-developed profile. The power law equation is:
u/umax = (1-r/R)1/n
u = velocity at measurement point
umax = max velocity in pipe
r = radius at measurement point
R = pipe radius
n = power
A value of n = 7 is typically used to fit the velocity profile for fully developed, turbulent flows. A higher value of n creates a flatter profile. A lower value creates a more bullet shape profile associated with laminar flow. A power law curve where
n = 7 is shown in Figure 4.
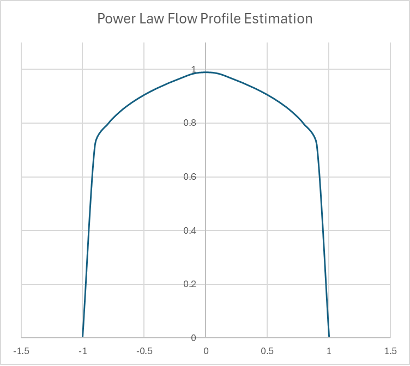
As flow is disturbed with the addition of pipe elements, the flow profile will change. For example, flow through a single elbow creates a skewed profile. The high velocity “core” of the pipe will be pushed to the opposite wall of the pipe, creating an asymmetry where the maximum velocity is no longer in the middle of the pipe. Single elbows and other elements can create asymmetry in the flow profile which is shown well in Figure 5.
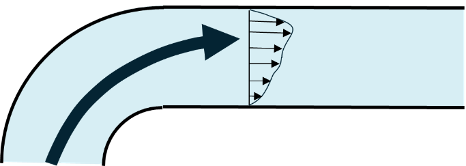
Swirling flow
The flow profile does not capture another type of flow disturbance called swirling flow. Swirling flow is when the flow has a crossflow element. Without swirl the flow will run straight down the pipe, with 0° in relation to the centerline of the pipe. If crossflow is present, the flow streams can have a swirl angle, up to 20° in severe cases.
There are two general types of swirl disturbances, Type 1 and Type 2 swirls. Type 1 swirl moves in one directional rotation across the pipe. This is also known as whole body swirl, Figure 6. Close coupled double elbows out of plane are a common cause of Type 1 swirl, along with headers, pumps and compressors. Type 2 swirl introduces two counter rotating swirls rotating in opposite directions, Figure 7. This is usually created after single elbows.
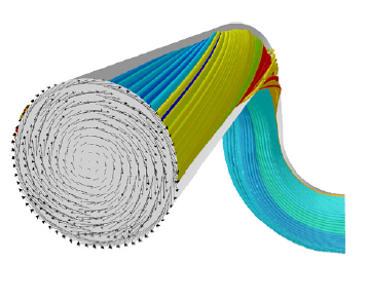
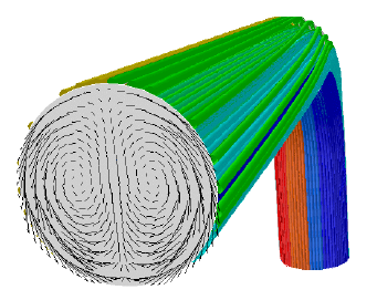
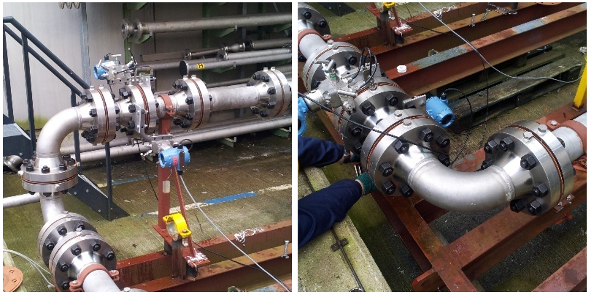
Orifice plate flow measurements
Orifice plates measurement have a century-long track record of continuous use and improvement in industrial applications. No other flow technology has the international volume of understanding and acceptance as orifice plates. Orifice plates are often described as “a hole in a plate” and often ridiculed for that simplicity. Yet it is the simplicity of an orifice plate that makes it so elegant. Leonardo da Vinci once said, “Simplicity is the ultimate sophistication”. The design of the orifice plate makes it possible to manufacture with precision and repeatability. Making one orifice plate measure the same as the next one with matching dimensions. A dimensional inspection is all that is needed to “calibrate” an orifice plate.
Knowing that two identical orifice plates will measure the same (within known uncertainties) is one of the reasons why they are the most widely used industrial flow technology even after 100 years. In today’s world, a user can replace an orifice plate and know the uncertainty of the measurement will not change, even without a flow calibration – something no other flow technology can match!
This also means that a flow calibration once done on a known orifice plate size, can be applied to all other matching orifice plates. Over the decades a massive database of traceable orifice calibrations was completed and used to create the de facto standards for orifice flow measurement. The American standards are the AGA Report No 3 and API 14.3 standards for natural measurement using an orifice plate. The international standard for orifice plates is ISO 5167.
The orifice performance in that technical database (which includes over 30,000 data points!) was tested in well-developed flow conditions. The standards confirm that measurement in matching conditions and dimensions will perform at custody transfer levels of accuracy. And since all the data points were tested in well-developed flow conditions, the standards require the same for accurate measurement.
Effect of flow disturbances on orifice measurement
If a user’s flow conditions are not well developed, with asymmetric or swirling flow, the accuracy will be affected. The effect on accuracy will depend on several factors, including the type of disturbance and the relative distance of the disturbance to the orifice location.
As the distance from the disturbance to the orifice plate increases, the flow will naturally return to a well-developed state due to the turbulence in the flow (turbulence helps us here). The distance needed to return to well-developed flow depends mostly on the type of disturbance. The AGA/API standards recommend up to 44 pipe diameters of straight pipe after double elbow to achieve well developed flow.
Shown below are two sets of flow calibration data from Mattingly and Yeh measuring three different orifice bore sizes (beta ratios) at various distances from a disturbance. Figure 8 shows single elbow effects.Figure 9 shows effects from close coupled, double elbows out of plane.
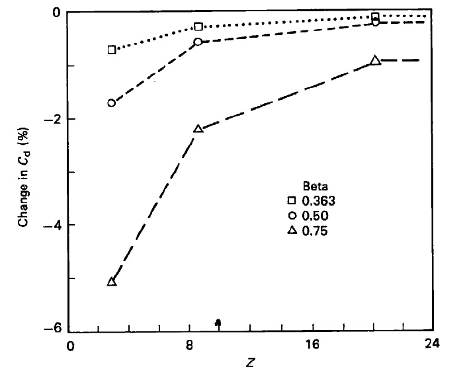
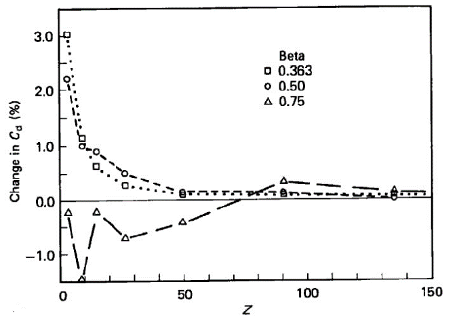
The effect of the disturbance diminishes with distance, approaching zero effect. Notice the effects on accuracy of the orifice plate measurement can be up to 5% after a single elbow using a high beta ratio. The effect lessens using smaller beta ratios. Also notice the x-axis scale of the double elbows chart is much larger than the single elbow chart. This confirms that Type 1 swirl has a much longer lasting impact on flow measurement than Type 2 swirl.
Improving flow conditions
A user can make a determination about their installation knowing the above information. They have three options available to them:
- The user could plan the measurement point as far as possible from the disturbance. The more distance means the more likely the flow is well developed at that point. Some users may have plenty of straight pipe in their system and can meet the minimum requirements in the standards. For most users, creating the necessary straight inlet piping will come with additional expense.
- The user can accept the additional uncertainty that comes with a bad installation. This might be a fine solution in applications with low accuracy requirements. But most industrial applications cannot accept accuracy shifts on the order of ±5%.
- The user could follow the most common practice in the industry: use a flow conditioner.
Flow conditioners
The user of flow conditioners is an industry best practice for ensuring optimal flow measurement with an orifice plate. Flow conditioners come in a variety of designs but have one common goal: to condition the flow to well-developed conditions ahead of an orifice flow measurement point regardless of the disturbance ahead of it.
In the AGA Report No. 3, Section 2.3.1.7 “Flow Conditioners” classifies flow conditioners into two categories: straighteners and isolating flow conditioners.
“Flow straighteners are devices that effectively remove or reduce the swirl component of a flowing stream but may have limited ability to produce the flow conditions necessary to accurately replicate the orifice plate coefficient of discharge database values. Isolating flow conditioners are devices that effectively remove the swirl component from the flowing stream while redistributing the stream to produce the flow conditions that accurately replicate the orifice plate coefficient of discharge database values.”
Flow straighteners
Flow straighteners are low blockage, swirling reducing flow conditioners. Common examples of flow straighteners are tube bundles, example shown in Figure 10 and fin-type straightening vanes, example shown in Figure 11. Tube bundles can be designed with 19 or 7 tubes concentrically grouped in the pipe. The terminology around these can be confusing as tube bundles are sometimes sold as straightening vanes, but both fall into the category of flow straightener as described in AGA 3.
These types of flow conditioners are designed to remove swirl with their elongated dimensions. But since they are low blockages, they do very little to correct he asymmetry in the flow profile. In fact, Mattingly and Yeh also showed that flow straighteners can actually make asymmetry a more persistent flow disturbance, lasting much longer in terms of distance. This is because the flow straighteners will capture the asymmetry entering each tube and reduce the type 2 swirl. By reducing the type 2 swirl, the natural turbulence is diminished and the asymmetry does not break down as quickly.
In short, flow straighteners are not recommended for orifice plate measurement.
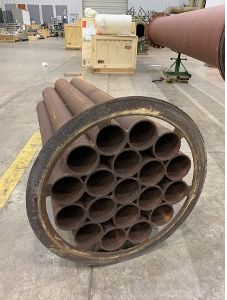

Isolating flow conditioners
Isolating flow conditioners have a blockage factor that forces the flow profile to redistribute as it passes through. This redistribution controls both the asymmetry and swirl disturbances. The design is typically a perforated plate with multiple holes designed to create a well-developed flow profile as soon as possible after the plate.
The search for the ideal pattern of holes to do this job was the subject of much research in the 1990’s as the need for flow conditioning became more and more relevant. A summary of the research from researchers such as Laws, Karnik, Zanker, Gallagher and others is fascinating but outside the scope of this paper. The most widely accepted design of this research was developed by Laws and has become known as the NOVA 50E design.
The NOVA 50E design, Figure 12, is a multi-hole flow conditioner with concentric rings of openings. 16 smaller holes around 8 midsized holes around one large central opening. The size and position of each hole is meant to stimulate the formation of a well-developed flow profile regardless of upstream disturbances. The “50” designation indicates that the plate has approximately a 50% blockage area in the flow path. The success of this design is the balance of three factors: 1) enough blockage to redistribute the flow profile, 2) large enough holes to allow passage of particles and 3) enough opening to reduce the pressure loss across the plate as much as possible. The NOVA design meets the requirements of AGA 3 Section 2.5.5 and APPENDIX 2-D.
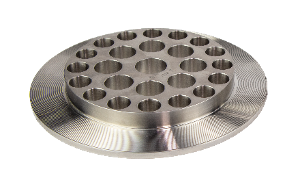
The design is universal for all flow conditions and disturbances. This advantage means a user can have one design flow conditioner for various pipeline installations and conditions. And it gives the user the assurance that most flow disturbances will be removed prior to flow measurement. For as much testing and research has been done of the effects of flow disturbances in a pipe, a user does not know the flow regime and development of their flow profile. Having a flow conditioner improves orifice plate measurement in all standard applications.
Conclusion
The use of a flow conditioner is recommended for all high accuracy orifice plate measurements. The recommended type of flow conditioner is the NOVA 50E design to remove most flow disturbances such as asymmetry and swirl. And users will benefit from the assurance that a well-designed flow conditioner will remove any unknown flow disturbances and problems that could diminish their measurement accuracy.
[1] Effects of pipe elbows and tube bundles onselected types of flowmeters, G.E. Mattingly, T.T. Yeh, Flow Measurement Instrumentation, Vol 2, January 1991
[2] US Patent 5,341,848 “Flow Conditioner”, 1994
Abstract
This paper discusses the effects of poor installations on orifice measurement and the best practices to achieve highest accuracy and performance. Flow disturbances are everywhere in pipelines and industrial applications. Knowing the types of disturbances, their effect on orifice measurement and how to correct those errors is valuable for anyone interested in accurate orifice flow measurement.
What is “Good” Flow
Most flowmeters are affected by the flow that they are trying to measure, orifice plate flowmeters included. Orifice plates measure best in “good” flow conditions and lose accuracy in “bad” conditions. There are several methods to describe and characterize good vs. bad flow conditions. When asked to describe good flow conditions, many users will use the term Laminar. This is a common yet minor misconception in flow engineering.
Laminar vs. Turbulent Flow
Laminar is a flow regime where the flow follows relatively straight lines down a pipe, Figure 1. If you were to follow a particle in the flow, it would go in a straight path and not cross paths with other particles flowing next to it. This is a regime with no turbulence. Laminar flow will happen in low flow and/or high viscous applications. In other words, the momentum forces are low and/or the viscous forces are high. Inherently this makes sense as higher velocities will encourage turbulence and higher viscosities will do the opposite.
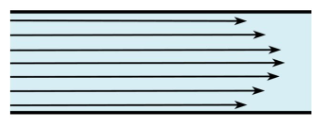
As useful tool is the Reynolds number, which is a dimensionless number used to quantify whether a flow application is in laminar flow. The Reynolds number equations is a follows:
Re=VρD/μ
Re = Reynolds number, dimensionless
V = flow velocity, ft/s
ρ = density, lbm/ft3
μ = dynamic viscosity, lbm/s·ft
The numerator of this equation combines the momentum forces in the flow, velocity, density and size. While the denominator are the inertial forces, viscosity. This follows the logic described earlier. The lower the Reynolds number, the more likely the flow regime is in a laminar state. Laminar flow is more likely to exist where the velocity, density or size is small, and/or where the viscosity is high. The commonly accepted value of laminar flow is Re < 4000. As the Reynolds number increases, the flow regime enters a transition phase between 4000 and 10,000. Above 10,000, the flow regime is considered to be turbulent.
Reynolds number - Flow regime
0 – 4,000 - Laminar
4000 – 10,000 - Transition
>10,000 - Turbulent
Turbulent flow, Figure 2, is the opposite of laminar flow in that the flow streams do not follow a straight or regular pattern. In turbulent flow the flow streams cross, small eddies occur, and mixing is more common. The word “turbulent” rightfully has negative connotations. No one wants to be on an airplane and fly through turbulence.
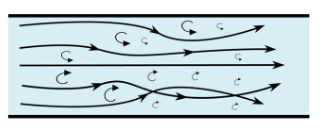
So why is Laminar the incorrect term to describe good flow? It’s not. It’s just not the world in which our flowmeters live. The vast majority of industrial pipelines are in the turbulent flow regime. Virtually all gas flows are turbulent due to the high velocities and low viscosities. Even most liquid flows are turbulent, except for some high viscosity products such as crude oil. Turbulent flow is better for orifice measurement because orifice plates were designed to measure it and their performance is well understood in those conditions.
A side note: Reynolds number is a very helpful in flow measurement. Since it is a dimensionless number, Reynolds can use a single number to describe a flow application. And that number can be used across applications. If the Reynolds number for an application is below 4000, that application is in the laminar flow regime, regardless of the size for example. Reynolds number is used when calibrating a flowmeter. Since the Reynolds number describes the flow in a single number, users can calibrate on one fluid and use the flowmeter in another fluid, knowing the performance will match at equal Reynolds numbers.
Flow profile
A better way to describe understand good vs. bad flow is the presence or absence of flow disturbances. Long, straight, unobstructed pipe will create undisturbed flow. The addition of common pipe elements will create disturbances. Common pipe elements can include single elbows, tees, two elbows in series, partially closed valves, pipe reductions or expansions, thermowells, and many more.
Just like the Reynolds number is a tool to understand the flow regime, the flow profile is a tool to visualize whether flow is disturbed or not. The flow profile attempts to show the velocity at difference points across the diameter of a flowing pipe. This can be physically measured in several ways such as with a single point Pitot tube sensor or with more complex tools such as laser doppler velocimetry. Typically, the view is across a full diameter, crossing through the midpoint of the pipe. A typical flow profile looks like Figure 3 for turbulent flow. Each arrow represents the velocity at points across a diameter of the pipe. The velocities are higher in the center of the pipe and lower near the pipe walls.
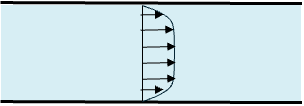
The friction on the pipe walls causes drag which slows down the fluid flow nearest to it. As the flow continues down the pipe, the next layer away from the pipe wall is slowed down slightly less. And so on until the effect of the pipe wall friction no longer affects the velocity. This is called the boundary layer effect and is created whenever flow passes over a surface. Notice the shape of the Figure 3 profile in turbulent flow is different than the shape in Figure 1. Laminar flow has a characteristic “bullet” shaped profile and turbulent has a flatter shape.
Well-developed flow is created when the boundary layer is fully established without disturbances. Put another way, well developed flow will not change its profile as it moves down the pipe. In the industrial flow measurement world, it’s also the definition of good flow and is very important in understanding flow through an orifice.
Power law estimation
When comparing whether a flow profile is well developed or not, a useful tool is the power law estimation. The power law gives a numerical estimation of a well-developed profile. The power law equation is:
u/umax = (1-r/R)1/n
u = velocity at measurement point
umax = max velocity in pipe
r = radius at measurement point
R = pipe radius
n = power
A value of n = 7 is typically used to fit the velocity profile for fully developed, turbulent flows. A higher value of n creates a flatter profile. A lower value creates a more bullet shape profile associated with laminar flow. A power law curve where
n = 7 is shown in Figure 4.
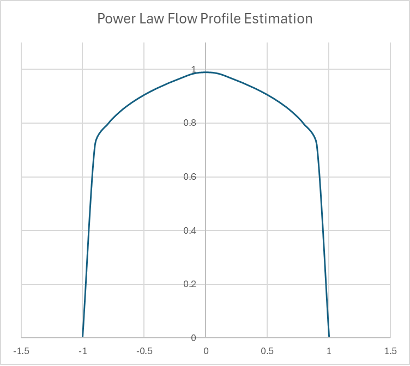
As flow is disturbed with the addition of pipe elements, the flow profile will change. For example, flow through a single elbow creates a skewed profile. The high velocity “core” of the pipe will be pushed to the opposite wall of the pipe, creating an asymmetry where the maximum velocity is no longer in the middle of the pipe. Single elbows and other elements can create asymmetry in the flow profile which is shown well in Figure 5.
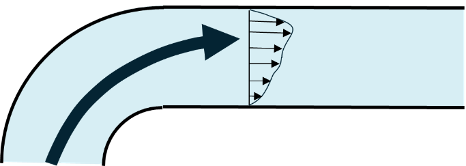
Swirling flow
The flow profile does not capture another type of flow disturbance called swirling flow. Swirling flow is when the flow has a crossflow element. Without swirl the flow will run straight down the pipe, with 0° in relation to the centerline of the pipe. If crossflow is present, the flow streams can have a swirl angle, up to 20° in severe cases.
There are two general types of swirl disturbances, Type 1 and Type 2 swirls. Type 1 swirl moves in one directional rotation across the pipe. This is also known as whole body swirl, Figure 6. Close coupled double elbows out of plane are a common cause of Type 1 swirl, along with headers, pumps and compressors. Type 2 swirl introduces two counter rotating swirls rotating in opposite directions, Figure 7. This is usually created after single elbows.
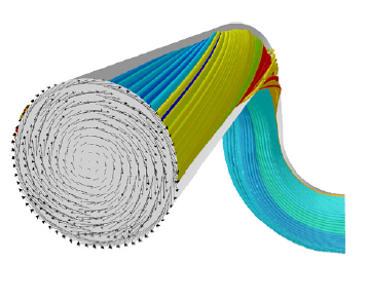
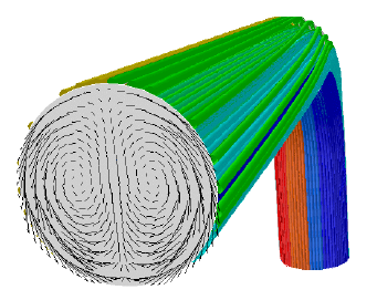
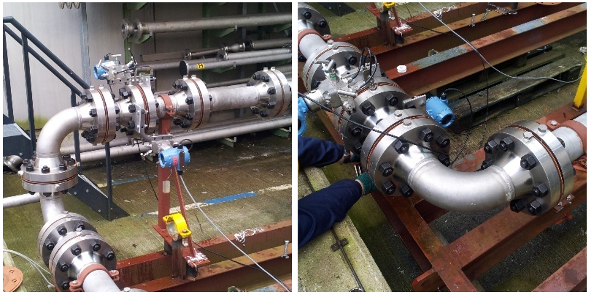
Orifice plate flow measurements
Orifice plates measurement have a century-long track record of continuous use and improvement in industrial applications. No other flow technology has the international volume of understanding and acceptance as orifice plates. Orifice plates are often described as “a hole in a plate” and often ridiculed for that simplicity. Yet it is the simplicity of an orifice plate that makes it so elegant. Leonardo da Vinci once said, “Simplicity is the ultimate sophistication”. The design of the orifice plate makes it possible to manufacture with precision and repeatability. Making one orifice plate measure the same as the next one with matching dimensions. A dimensional inspection is all that is needed to “calibrate” an orifice plate.
Knowing that two identical orifice plates will measure the same (within known uncertainties) is one of the reasons why they are the most widely used industrial flow technology even after 100 years. In today’s world, a user can replace an orifice plate and know the uncertainty of the measurement will not change, even without a flow calibration – something no other flow technology can match!
This also means that a flow calibration once done on a known orifice plate size, can be applied to all other matching orifice plates. Over the decades a massive database of traceable orifice calibrations was completed and used to create the de facto standards for orifice flow measurement. The American standards are the AGA Report No 3 and API 14.3 standards for natural measurement using an orifice plate. The international standard for orifice plates is ISO 5167.
The orifice performance in that technical database (which includes over 30,000 data points!) was tested in well-developed flow conditions. The standards confirm that measurement in matching conditions and dimensions will perform at custody transfer levels of accuracy. And since all the data points were tested in well-developed flow conditions, the standards require the same for accurate measurement.
Effect of flow disturbances on orifice measurement
If a user’s flow conditions are not well developed, with asymmetric or swirling flow, the accuracy will be affected. The effect on accuracy will depend on several factors, including the type of disturbance and the relative distance of the disturbance to the orifice location.
As the distance from the disturbance to the orifice plate increases, the flow will naturally return to a well-developed state due to the turbulence in the flow (turbulence helps us here). The distance needed to return to well-developed flow depends mostly on the type of disturbance. The AGA/API standards recommend up to 44 pipe diameters of straight pipe after double elbow to achieve well developed flow.
Shown below are two sets of flow calibration data from Mattingly and Yeh measuring three different orifice bore sizes (beta ratios) at various distances from a disturbance. Figure 8 shows single elbow effects.Figure 9 shows effects from close coupled, double elbows out of plane.
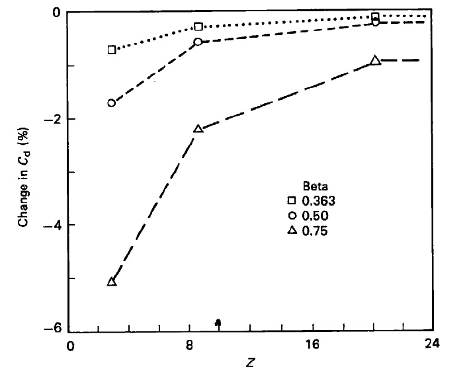
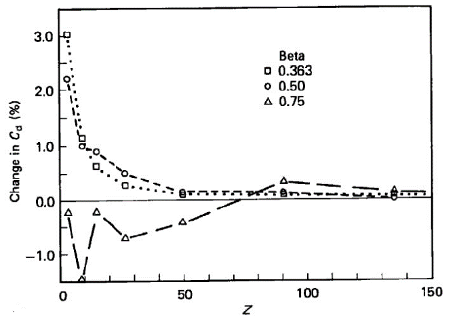
The effect of the disturbance diminishes with distance, approaching zero effect. Notice the effects on accuracy of the orifice plate measurement can be up to 5% after a single elbow using a high beta ratio. The effect lessens using smaller beta ratios. Also notice the x-axis scale of the double elbows chart is much larger than the single elbow chart. This confirms that Type 1 swirl has a much longer lasting impact on flow measurement than Type 2 swirl.
Improving flow conditions
A user can make a determination about their installation knowing the above information. They have three options available to them:
- The user could plan the measurement point as far as possible from the disturbance. The more distance means the more likely the flow is well developed at that point. Some users may have plenty of straight pipe in their system and can meet the minimum requirements in the standards. For most users, creating the necessary straight inlet piping will come with additional expense.
- The user can accept the additional uncertainty that comes with a bad installation. This might be a fine solution in applications with low accuracy requirements. But most industrial applications cannot accept accuracy shifts on the order of ±5%.
- The user could follow the most common practice in the industry: use a flow conditioner.
Flow conditioners
The user of flow conditioners is an industry best practice for ensuring optimal flow measurement with an orifice plate. Flow conditioners come in a variety of designs but have one common goal: to condition the flow to well-developed conditions ahead of an orifice flow measurement point regardless of the disturbance ahead of it.
In the AGA Report No. 3, Section 2.3.1.7 “Flow Conditioners” classifies flow conditioners into two categories: straighteners and isolating flow conditioners.
“Flow straighteners are devices that effectively remove or reduce the swirl component of a flowing stream but may have limited ability to produce the flow conditions necessary to accurately replicate the orifice plate coefficient of discharge database values. Isolating flow conditioners are devices that effectively remove the swirl component from the flowing stream while redistributing the stream to produce the flow conditions that accurately replicate the orifice plate coefficient of discharge database values.”
Flow straighteners
Flow straighteners are low blockage, swirling reducing flow conditioners. Common examples of flow straighteners are tube bundles, example shown in Figure 10 and fin-type straightening vanes, example shown in Figure 11. Tube bundles can be designed with 19 or 7 tubes concentrically grouped in the pipe. The terminology around these can be confusing as tube bundles are sometimes sold as straightening vanes, but both fall into the category of flow straightener as described in AGA 3.
These types of flow conditioners are designed to remove swirl with their elongated dimensions. But since they are low blockages, they do very little to correct he asymmetry in the flow profile. In fact, Mattingly and Yeh also showed that flow straighteners can actually make asymmetry a more persistent flow disturbance, lasting much longer in terms of distance. This is because the flow straighteners will capture the asymmetry entering each tube and reduce the type 2 swirl. By reducing the type 2 swirl, the natural turbulence is diminished and the asymmetry does not break down as quickly.
In short, flow straighteners are not recommended for orifice plate measurement.
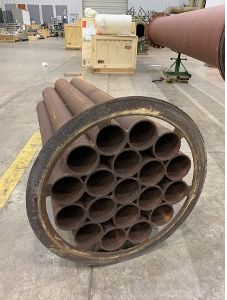

Isolating flow conditioners
Isolating flow conditioners have a blockage factor that forces the flow profile to redistribute as it passes through. This redistribution controls both the asymmetry and swirl disturbances. The design is typically a perforated plate with multiple holes designed to create a well-developed flow profile as soon as possible after the plate.
The search for the ideal pattern of holes to do this job was the subject of much research in the 1990’s as the need for flow conditioning became more and more relevant. A summary of the research from researchers such as Laws, Karnik, Zanker, Gallagher and others is fascinating but outside the scope of this paper. The most widely accepted design of this research was developed by Laws and has become known as the NOVA 50E design.
The NOVA 50E design, Figure 12, is a multi-hole flow conditioner with concentric rings of openings. 16 smaller holes around 8 midsized holes around one large central opening. The size and position of each hole is meant to stimulate the formation of a well-developed flow profile regardless of upstream disturbances. The “50” designation indicates that the plate has approximately a 50% blockage area in the flow path. The success of this design is the balance of three factors: 1) enough blockage to redistribute the flow profile, 2) large enough holes to allow passage of particles and 3) enough opening to reduce the pressure loss across the plate as much as possible. The NOVA design meets the requirements of AGA 3 Section 2.5.5 and APPENDIX 2-D.
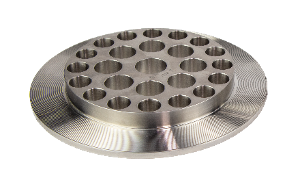
The design is universal for all flow conditions and disturbances. This advantage means a user can have one design flow conditioner for various pipeline installations and conditions. And it gives the user the assurance that most flow disturbances will be removed prior to flow measurement. For as much testing and research has been done of the effects of flow disturbances in a pipe, a user does not know the flow regime and development of their flow profile. Having a flow conditioner improves orifice plate measurement in all standard applications.
Conclusion
The use of a flow conditioner is recommended for all high accuracy orifice plate measurements. The recommended type of flow conditioner is the NOVA 50E design to remove most flow disturbances such as asymmetry and swirl. And users will benefit from the assurance that a well-designed flow conditioner will remove any unknown flow disturbances and problems that could diminish their measurement accuracy.
[1] Effects of pipe elbows and tube bundles onselected types of flowmeters, G.E. Mattingly, T.T. Yeh, Flow Measurement Instrumentation, Vol 2, January 1991
[2] US Patent 5,341,848 “Flow Conditioner”, 1994
Abstract
This paper discusses the effects of poor installations on orifice measurement and the best practices to achieve highest accuracy and performance. Flow disturbances are everywhere in pipelines and industrial applications. Knowing the types of disturbances, their effect on orifice measurement and how to correct those errors is valuable for anyone interested in accurate orifice flow measurement.
What is “Good” Flow
Most flowmeters are affected by the flow that they are trying to measure, orifice plate flowmeters included. Orifice plates measure best in “good” flow conditions and lose accuracy in “bad” conditions. There are several methods to describe and characterize good vs. bad flow conditions. When asked to describe good flow conditions, many users will use the term Laminar. This is a common yet minor misconception in flow engineering.
Laminar vs. Turbulent Flow
Laminar is a flow regime where the flow follows relatively straight lines down a pipe, Figure 1. If you were to follow a particle in the flow, it would go in a straight path and not cross paths with other particles flowing next to it. This is a regime with no turbulence. Laminar flow will happen in low flow and/or high viscous applications. In other words, the momentum forces are low and/or the viscous forces are high. Inherently this makes sense as higher velocities will encourage turbulence and higher viscosities will do the opposite.
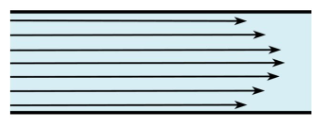
As useful tool is the Reynolds number, which is a dimensionless number used to quantify whether a flow application is in laminar flow. The Reynolds number equations is a follows:
Re=VρD/μ
Re = Reynolds number, dimensionless
V = flow velocity, ft/s
ρ = density, lbm/ft3
μ = dynamic viscosity, lbm/s·ft
The numerator of this equation combines the momentum forces in the flow, velocity, density and size. While the denominator are the inertial forces, viscosity. This follows the logic described earlier. The lower the Reynolds number, the more likely the flow regime is in a laminar state. Laminar flow is more likely to exist where the velocity, density or size is small, and/or where the viscosity is high. The commonly accepted value of laminar flow is Re < 4000. As the Reynolds number increases, the flow regime enters a transition phase between 4000 and 10,000. Above 10,000, the flow regime is considered to be turbulent.
Reynolds number - Flow regime
0 – 4,000 - Laminar
4000 – 10,000 - Transition
>10,000 - Turbulent
Turbulent flow, Figure 2, is the opposite of laminar flow in that the flow streams do not follow a straight or regular pattern. In turbulent flow the flow streams cross, small eddies occur, and mixing is more common. The word “turbulent” rightfully has negative connotations. No one wants to be on an airplane and fly through turbulence.
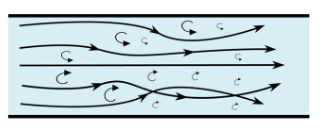
So why is Laminar the incorrect term to describe good flow? It’s not. It’s just not the world in which our flowmeters live. The vast majority of industrial pipelines are in the turbulent flow regime. Virtually all gas flows are turbulent due to the high velocities and low viscosities. Even most liquid flows are turbulent, except for some high viscosity products such as crude oil. Turbulent flow is better for orifice measurement because orifice plates were designed to measure it and their performance is well understood in those conditions.
A side note: Reynolds number is a very helpful in flow measurement. Since it is a dimensionless number, Reynolds can use a single number to describe a flow application. And that number can be used across applications. If the Reynolds number for an application is below 4000, that application is in the laminar flow regime, regardless of the size for example. Reynolds number is used when calibrating a flowmeter. Since the Reynolds number describes the flow in a single number, users can calibrate on one fluid and use the flowmeter in another fluid, knowing the performance will match at equal Reynolds numbers.
Flow profile
A better way to describe understand good vs. bad flow is the presence or absence of flow disturbances. Long, straight, unobstructed pipe will create undisturbed flow. The addition of common pipe elements will create disturbances. Common pipe elements can include single elbows, tees, two elbows in series, partially closed valves, pipe reductions or expansions, thermowells, and many more.
Just like the Reynolds number is a tool to understand the flow regime, the flow profile is a tool to visualize whether flow is disturbed or not. The flow profile attempts to show the velocity at difference points across the diameter of a flowing pipe. This can be physically measured in several ways such as with a single point Pitot tube sensor or with more complex tools such as laser doppler velocimetry. Typically, the view is across a full diameter, crossing through the midpoint of the pipe. A typical flow profile looks like Figure 3 for turbulent flow. Each arrow represents the velocity at points across a diameter of the pipe. The velocities are higher in the center of the pipe and lower near the pipe walls.
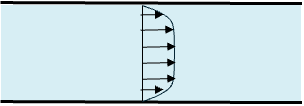
The friction on the pipe walls causes drag which slows down the fluid flow nearest to it. As the flow continues down the pipe, the next layer away from the pipe wall is slowed down slightly less. And so on until the effect of the pipe wall friction no longer affects the velocity. This is called the boundary layer effect and is created whenever flow passes over a surface. Notice the shape of the Figure 3 profile in turbulent flow is different than the shape in Figure 1. Laminar flow has a characteristic “bullet” shaped profile and turbulent has a flatter shape.
Well-developed flow is created when the boundary layer is fully established without disturbances. Put another way, well developed flow will not change its profile as it moves down the pipe. In the industrial flow measurement world, it’s also the definition of good flow and is very important in understanding flow through an orifice.
Power law estimation
When comparing whether a flow profile is well developed or not, a useful tool is the power law estimation. The power law gives a numerical estimation of a well-developed profile. The power law equation is:
u/umax = (1-r/R)1/n
u = velocity at measurement point
umax = max velocity in pipe
r = radius at measurement point
R = pipe radius
n = power
A value of n = 7 is typically used to fit the velocity profile for fully developed, turbulent flows. A higher value of n creates a flatter profile. A lower value creates a more bullet shape profile associated with laminar flow. A power law curve where
n = 7 is shown in Figure 4.
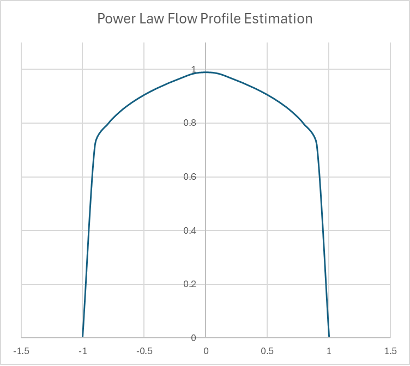
As flow is disturbed with the addition of pipe elements, the flow profile will change. For example, flow through a single elbow creates a skewed profile. The high velocity “core” of the pipe will be pushed to the opposite wall of the pipe, creating an asymmetry where the maximum velocity is no longer in the middle of the pipe. Single elbows and other elements can create asymmetry in the flow profile which is shown well in Figure 5.
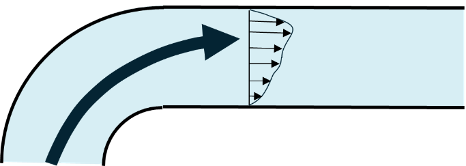
Swirling flow
The flow profile does not capture another type of flow disturbance called swirling flow. Swirling flow is when the flow has a crossflow element. Without swirl the flow will run straight down the pipe, with 0° in relation to the centerline of the pipe. If crossflow is present, the flow streams can have a swirl angle, up to 20° in severe cases.
There are two general types of swirl disturbances, Type 1 and Type 2 swirls. Type 1 swirl moves in one directional rotation across the pipe. This is also known as whole body swirl, Figure 6. Close coupled double elbows out of plane are a common cause of Type 1 swirl, along with headers, pumps and compressors. Type 2 swirl introduces two counter rotating swirls rotating in opposite directions, Figure 7. This is usually created after single elbows.
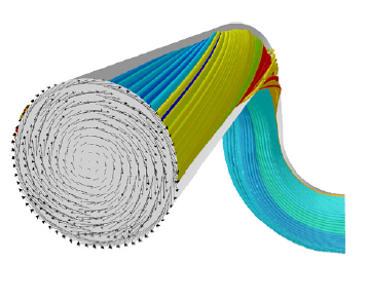
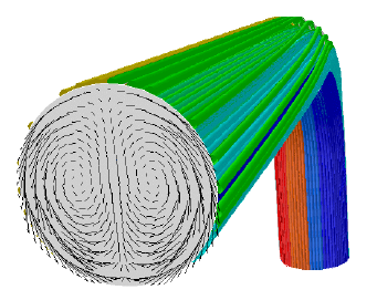
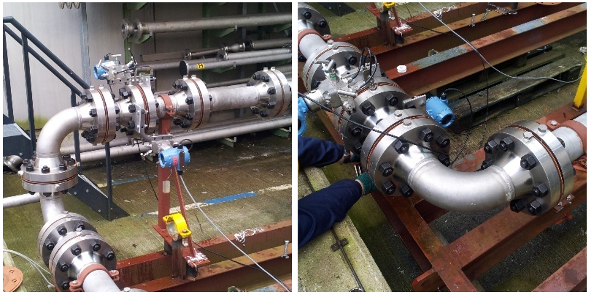
Orifice plate flow measurements
Orifice plates measurement have a century-long track record of continuous use and improvement in industrial applications. No other flow technology has the international volume of understanding and acceptance as orifice plates. Orifice plates are often described as “a hole in a plate” and often ridiculed for that simplicity. Yet it is the simplicity of an orifice plate that makes it so elegant. Leonardo da Vinci once said, “Simplicity is the ultimate sophistication”. The design of the orifice plate makes it possible to manufacture with precision and repeatability. Making one orifice plate measure the same as the next one with matching dimensions. A dimensional inspection is all that is needed to “calibrate” an orifice plate.
Knowing that two identical orifice plates will measure the same (within known uncertainties) is one of the reasons why they are the most widely used industrial flow technology even after 100 years. In today’s world, a user can replace an orifice plate and know the uncertainty of the measurement will not change, even without a flow calibration – something no other flow technology can match!
This also means that a flow calibration once done on a known orifice plate size, can be applied to all other matching orifice plates. Over the decades a massive database of traceable orifice calibrations was completed and used to create the de facto standards for orifice flow measurement. The American standards are the AGA Report No 3 and API 14.3 standards for natural measurement using an orifice plate. The international standard for orifice plates is ISO 5167.
The orifice performance in that technical database (which includes over 30,000 data points!) was tested in well-developed flow conditions. The standards confirm that measurement in matching conditions and dimensions will perform at custody transfer levels of accuracy. And since all the data points were tested in well-developed flow conditions, the standards require the same for accurate measurement.
Effect of flow disturbances on orifice measurement
If a user’s flow conditions are not well developed, with asymmetric or swirling flow, the accuracy will be affected. The effect on accuracy will depend on several factors, including the type of disturbance and the relative distance of the disturbance to the orifice location.
As the distance from the disturbance to the orifice plate increases, the flow will naturally return to a well-developed state due to the turbulence in the flow (turbulence helps us here). The distance needed to return to well-developed flow depends mostly on the type of disturbance. The AGA/API standards recommend up to 44 pipe diameters of straight pipe after double elbow to achieve well developed flow.
Shown below are two sets of flow calibration data from Mattingly and Yeh measuring three different orifice bore sizes (beta ratios) at various distances from a disturbance. Figure 8 shows single elbow effects.Figure 9 shows effects from close coupled, double elbows out of plane.
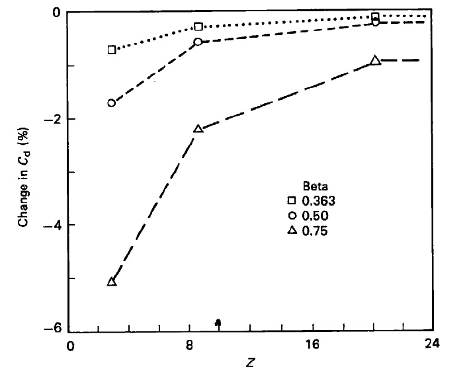
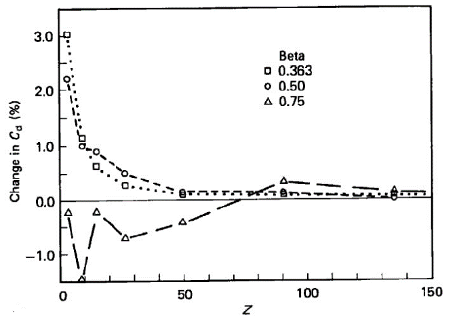
The effect of the disturbance diminishes with distance, approaching zero effect. Notice the effects on accuracy of the orifice plate measurement can be up to 5% after a single elbow using a high beta ratio. The effect lessens using smaller beta ratios. Also notice the x-axis scale of the double elbows chart is much larger than the single elbow chart. This confirms that Type 1 swirl has a much longer lasting impact on flow measurement than Type 2 swirl.
Improving flow conditions
A user can make a determination about their installation knowing the above information. They have three options available to them:
- The user could plan the measurement point as far as possible from the disturbance. The more distance means the more likely the flow is well developed at that point. Some users may have plenty of straight pipe in their system and can meet the minimum requirements in the standards. For most users, creating the necessary straight inlet piping will come with additional expense.
- The user can accept the additional uncertainty that comes with a bad installation. This might be a fine solution in applications with low accuracy requirements. But most industrial applications cannot accept accuracy shifts on the order of ±5%.
- The user could follow the most common practice in the industry: use a flow conditioner.
Flow conditioners
The user of flow conditioners is an industry best practice for ensuring optimal flow measurement with an orifice plate. Flow conditioners come in a variety of designs but have one common goal: to condition the flow to well-developed conditions ahead of an orifice flow measurement point regardless of the disturbance ahead of it.
In the AGA Report No. 3, Section 2.3.1.7 “Flow Conditioners” classifies flow conditioners into two categories: straighteners and isolating flow conditioners.
“Flow straighteners are devices that effectively remove or reduce the swirl component of a flowing stream but may have limited ability to produce the flow conditions necessary to accurately replicate the orifice plate coefficient of discharge database values. Isolating flow conditioners are devices that effectively remove the swirl component from the flowing stream while redistributing the stream to produce the flow conditions that accurately replicate the orifice plate coefficient of discharge database values.”
Flow straighteners
Flow straighteners are low blockage, swirling reducing flow conditioners. Common examples of flow straighteners are tube bundles, example shown in Figure 10 and fin-type straightening vanes, example shown in Figure 11. Tube bundles can be designed with 19 or 7 tubes concentrically grouped in the pipe. The terminology around these can be confusing as tube bundles are sometimes sold as straightening vanes, but both fall into the category of flow straightener as described in AGA 3.
These types of flow conditioners are designed to remove swirl with their elongated dimensions. But since they are low blockages, they do very little to correct he asymmetry in the flow profile. In fact, Mattingly and Yeh also showed that flow straighteners can actually make asymmetry a more persistent flow disturbance, lasting much longer in terms of distance. This is because the flow straighteners will capture the asymmetry entering each tube and reduce the type 2 swirl. By reducing the type 2 swirl, the natural turbulence is diminished and the asymmetry does not break down as quickly.
In short, flow straighteners are not recommended for orifice plate measurement.
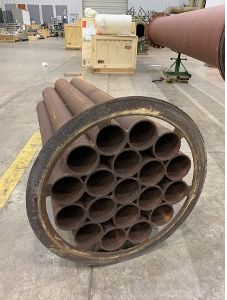

Isolating flow conditioners
Isolating flow conditioners have a blockage factor that forces the flow profile to redistribute as it passes through. This redistribution controls both the asymmetry and swirl disturbances. The design is typically a perforated plate with multiple holes designed to create a well-developed flow profile as soon as possible after the plate.
The search for the ideal pattern of holes to do this job was the subject of much research in the 1990’s as the need for flow conditioning became more and more relevant. A summary of the research from researchers such as Laws, Karnik, Zanker, Gallagher and others is fascinating but outside the scope of this paper. The most widely accepted design of this research was developed by Laws and has become known as the NOVA 50E design.
The NOVA 50E design, Figure 12, is a multi-hole flow conditioner with concentric rings of openings. 16 smaller holes around 8 midsized holes around one large central opening. The size and position of each hole is meant to stimulate the formation of a well-developed flow profile regardless of upstream disturbances. The “50” designation indicates that the plate has approximately a 50% blockage area in the flow path. The success of this design is the balance of three factors: 1) enough blockage to redistribute the flow profile, 2) large enough holes to allow passage of particles and 3) enough opening to reduce the pressure loss across the plate as much as possible. The NOVA design meets the requirements of AGA 3 Section 2.5.5 and APPENDIX 2-D.
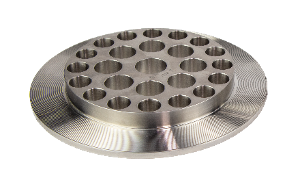
The design is universal for all flow conditions and disturbances. This advantage means a user can have one design flow conditioner for various pipeline installations and conditions. And it gives the user the assurance that most flow disturbances will be removed prior to flow measurement. For as much testing and research has been done of the effects of flow disturbances in a pipe, a user does not know the flow regime and development of their flow profile. Having a flow conditioner improves orifice plate measurement in all standard applications.
Conclusion
The use of a flow conditioner is recommended for all high accuracy orifice plate measurements. The recommended type of flow conditioner is the NOVA 50E design to remove most flow disturbances such as asymmetry and swirl. And users will benefit from the assurance that a well-designed flow conditioner will remove any unknown flow disturbances and problems that could diminish their measurement accuracy.
[1] Effects of pipe elbows and tube bundles onselected types of flowmeters, G.E. Mattingly, T.T. Yeh, Flow Measurement Instrumentation, Vol 2, January 1991
[2] US Patent 5,341,848 “Flow Conditioner”, 1994
Abstract
This paper discusses the effects of poor installations on orifice measurement and the best practices to achieve highest accuracy and performance. Flow disturbances are everywhere in pipelines and industrial applications. Knowing the types of disturbances, their effect on orifice measurement and how to correct those errors is valuable for anyone interested in accurate orifice flow measurement.
What is “Good” Flow
Most flowmeters are affected by the flow that they are trying to measure, orifice plate flowmeters included. Orifice plates measure best in “good” flow conditions and lose accuracy in “bad” conditions. There are several methods to describe and characterize good vs. bad flow conditions. When asked to describe good flow conditions, many users will use the term Laminar. This is a common yet minor misconception in flow engineering.
Laminar vs. Turbulent Flow
Laminar is a flow regime where the flow follows relatively straight lines down a pipe, Figure 1. If you were to follow a particle in the flow, it would go in a straight path and not cross paths with other particles flowing next to it. This is a regime with no turbulence. Laminar flow will happen in low flow and/or high viscous applications. In other words, the momentum forces are low and/or the viscous forces are high. Inherently this makes sense as higher velocities will encourage turbulence and higher viscosities will do the opposite.
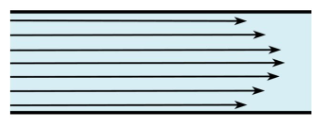
As useful tool is the Reynolds number, which is a dimensionless number used to quantify whether a flow application is in laminar flow. The Reynolds number equations is a follows:
Re=VρD/μ
Re = Reynolds number, dimensionless
V = flow velocity, ft/s
ρ = density, lbm/ft3
μ = dynamic viscosity, lbm/s·ft
The numerator of this equation combines the momentum forces in the flow, velocity, density and size. While the denominator are the inertial forces, viscosity. This follows the logic described earlier. The lower the Reynolds number, the more likely the flow regime is in a laminar state. Laminar flow is more likely to exist where the velocity, density or size is small, and/or where the viscosity is high. The commonly accepted value of laminar flow is Re < 4000. As the Reynolds number increases, the flow regime enters a transition phase between 4000 and 10,000. Above 10,000, the flow regime is considered to be turbulent.
Reynolds number - Flow regime
0 – 4,000 - Laminar
4000 – 10,000 - Transition
>10,000 - Turbulent
Turbulent flow, Figure 2, is the opposite of laminar flow in that the flow streams do not follow a straight or regular pattern. In turbulent flow the flow streams cross, small eddies occur, and mixing is more common. The word “turbulent” rightfully has negative connotations. No one wants to be on an airplane and fly through turbulence.
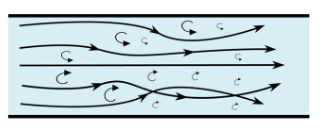
So why is Laminar the incorrect term to describe good flow? It’s not. It’s just not the world in which our flowmeters live. The vast majority of industrial pipelines are in the turbulent flow regime. Virtually all gas flows are turbulent due to the high velocities and low viscosities. Even most liquid flows are turbulent, except for some high viscosity products such as crude oil. Turbulent flow is better for orifice measurement because orifice plates were designed to measure it and their performance is well understood in those conditions.
A side note: Reynolds number is a very helpful in flow measurement. Since it is a dimensionless number, Reynolds can use a single number to describe a flow application. And that number can be used across applications. If the Reynolds number for an application is below 4000, that application is in the laminar flow regime, regardless of the size for example. Reynolds number is used when calibrating a flowmeter. Since the Reynolds number describes the flow in a single number, users can calibrate on one fluid and use the flowmeter in another fluid, knowing the performance will match at equal Reynolds numbers.
Flow profile
A better way to describe understand good vs. bad flow is the presence or absence of flow disturbances. Long, straight, unobstructed pipe will create undisturbed flow. The addition of common pipe elements will create disturbances. Common pipe elements can include single elbows, tees, two elbows in series, partially closed valves, pipe reductions or expansions, thermowells, and many more.
Just like the Reynolds number is a tool to understand the flow regime, the flow profile is a tool to visualize whether flow is disturbed or not. The flow profile attempts to show the velocity at difference points across the diameter of a flowing pipe. This can be physically measured in several ways such as with a single point Pitot tube sensor or with more complex tools such as laser doppler velocimetry. Typically, the view is across a full diameter, crossing through the midpoint of the pipe. A typical flow profile looks like Figure 3 for turbulent flow. Each arrow represents the velocity at points across a diameter of the pipe. The velocities are higher in the center of the pipe and lower near the pipe walls.
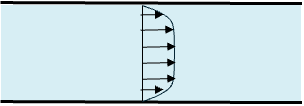
The friction on the pipe walls causes drag which slows down the fluid flow nearest to it. As the flow continues down the pipe, the next layer away from the pipe wall is slowed down slightly less. And so on until the effect of the pipe wall friction no longer affects the velocity. This is called the boundary layer effect and is created whenever flow passes over a surface. Notice the shape of the Figure 3 profile in turbulent flow is different than the shape in Figure 1. Laminar flow has a characteristic “bullet” shaped profile and turbulent has a flatter shape.
Well-developed flow is created when the boundary layer is fully established without disturbances. Put another way, well developed flow will not change its profile as it moves down the pipe. In the industrial flow measurement world, it’s also the definition of good flow and is very important in understanding flow through an orifice.
Power law estimation
When comparing whether a flow profile is well developed or not, a useful tool is the power law estimation. The power law gives a numerical estimation of a well-developed profile. The power law equation is:
u/umax = (1-r/R)1/n
u = velocity at measurement point
umax = max velocity in pipe
r = radius at measurement point
R = pipe radius
n = power
A value of n = 7 is typically used to fit the velocity profile for fully developed, turbulent flows. A higher value of n creates a flatter profile. A lower value creates a more bullet shape profile associated with laminar flow. A power law curve where
n = 7 is shown in Figure 4.
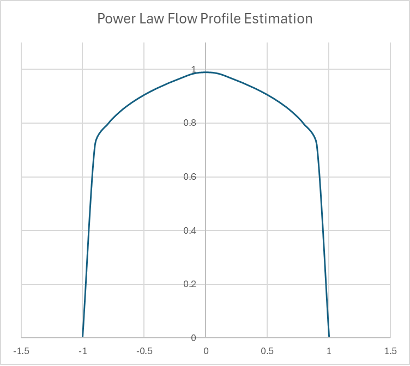
As flow is disturbed with the addition of pipe elements, the flow profile will change. For example, flow through a single elbow creates a skewed profile. The high velocity “core” of the pipe will be pushed to the opposite wall of the pipe, creating an asymmetry where the maximum velocity is no longer in the middle of the pipe. Single elbows and other elements can create asymmetry in the flow profile which is shown well in Figure 5.
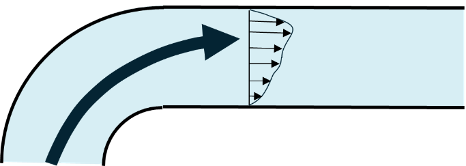
Swirling flow
The flow profile does not capture another type of flow disturbance called swirling flow. Swirling flow is when the flow has a crossflow element. Without swirl the flow will run straight down the pipe, with 0° in relation to the centerline of the pipe. If crossflow is present, the flow streams can have a swirl angle, up to 20° in severe cases.
There are two general types of swirl disturbances, Type 1 and Type 2 swirls. Type 1 swirl moves in one directional rotation across the pipe. This is also known as whole body swirl, Figure 6. Close coupled double elbows out of plane are a common cause of Type 1 swirl, along with headers, pumps and compressors. Type 2 swirl introduces two counter rotating swirls rotating in opposite directions, Figure 7. This is usually created after single elbows.
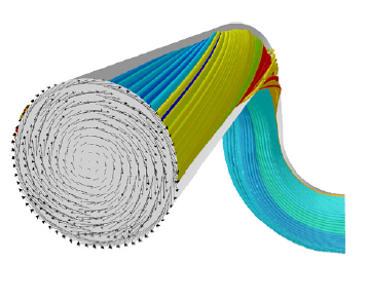
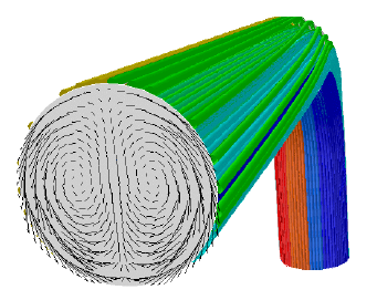
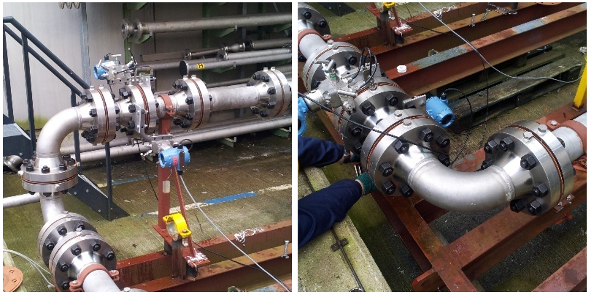
Orifice plate flow measurements
Orifice plates measurement have a century-long track record of continuous use and improvement in industrial applications. No other flow technology has the international volume of understanding and acceptance as orifice plates. Orifice plates are often described as “a hole in a plate” and often ridiculed for that simplicity. Yet it is the simplicity of an orifice plate that makes it so elegant. Leonardo da Vinci once said, “Simplicity is the ultimate sophistication”. The design of the orifice plate makes it possible to manufacture with precision and repeatability. Making one orifice plate measure the same as the next one with matching dimensions. A dimensional inspection is all that is needed to “calibrate” an orifice plate.
Knowing that two identical orifice plates will measure the same (within known uncertainties) is one of the reasons why they are the most widely used industrial flow technology even after 100 years. In today’s world, a user can replace an orifice plate and know the uncertainty of the measurement will not change, even without a flow calibration – something no other flow technology can match!
This also means that a flow calibration once done on a known orifice plate size, can be applied to all other matching orifice plates. Over the decades a massive database of traceable orifice calibrations was completed and used to create the de facto standards for orifice flow measurement. The American standards are the AGA Report No 3 and API 14.3 standards for natural measurement using an orifice plate. The international standard for orifice plates is ISO 5167.
The orifice performance in that technical database (which includes over 30,000 data points!) was tested in well-developed flow conditions. The standards confirm that measurement in matching conditions and dimensions will perform at custody transfer levels of accuracy. And since all the data points were tested in well-developed flow conditions, the standards require the same for accurate measurement.
Effect of flow disturbances on orifice measurement
If a user’s flow conditions are not well developed, with asymmetric or swirling flow, the accuracy will be affected. The effect on accuracy will depend on several factors, including the type of disturbance and the relative distance of the disturbance to the orifice location.
As the distance from the disturbance to the orifice plate increases, the flow will naturally return to a well-developed state due to the turbulence in the flow (turbulence helps us here). The distance needed to return to well-developed flow depends mostly on the type of disturbance. The AGA/API standards recommend up to 44 pipe diameters of straight pipe after double elbow to achieve well developed flow.
Shown below are two sets of flow calibration data from Mattingly and Yeh measuring three different orifice bore sizes (beta ratios) at various distances from a disturbance. Figure 8 shows single elbow effects.Figure 9 shows effects from close coupled, double elbows out of plane.
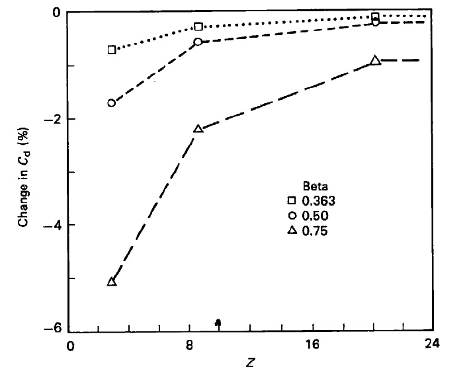
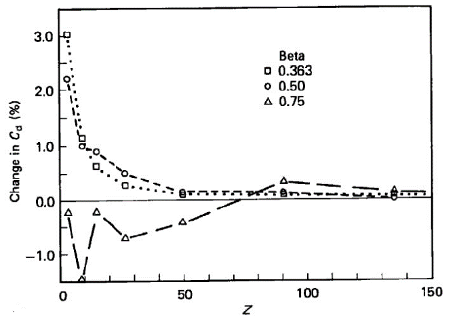
The effect of the disturbance diminishes with distance, approaching zero effect. Notice the effects on accuracy of the orifice plate measurement can be up to 5% after a single elbow using a high beta ratio. The effect lessens using smaller beta ratios. Also notice the x-axis scale of the double elbows chart is much larger than the single elbow chart. This confirms that Type 1 swirl has a much longer lasting impact on flow measurement than Type 2 swirl.
Improving flow conditions
A user can make a determination about their installation knowing the above information. They have three options available to them:
- The user could plan the measurement point as far as possible from the disturbance. The more distance means the more likely the flow is well developed at that point. Some users may have plenty of straight pipe in their system and can meet the minimum requirements in the standards. For most users, creating the necessary straight inlet piping will come with additional expense.
- The user can accept the additional uncertainty that comes with a bad installation. This might be a fine solution in applications with low accuracy requirements. But most industrial applications cannot accept accuracy shifts on the order of ±5%.
- The user could follow the most common practice in the industry: use a flow conditioner.
Flow conditioners
The user of flow conditioners is an industry best practice for ensuring optimal flow measurement with an orifice plate. Flow conditioners come in a variety of designs but have one common goal: to condition the flow to well-developed conditions ahead of an orifice flow measurement point regardless of the disturbance ahead of it.
In the AGA Report No. 3, Section 2.3.1.7 “Flow Conditioners” classifies flow conditioners into two categories: straighteners and isolating flow conditioners.
“Flow straighteners are devices that effectively remove or reduce the swirl component of a flowing stream but may have limited ability to produce the flow conditions necessary to accurately replicate the orifice plate coefficient of discharge database values. Isolating flow conditioners are devices that effectively remove the swirl component from the flowing stream while redistributing the stream to produce the flow conditions that accurately replicate the orifice plate coefficient of discharge database values.”
Flow straighteners
Flow straighteners are low blockage, swirling reducing flow conditioners. Common examples of flow straighteners are tube bundles, example shown in Figure 10 and fin-type straightening vanes, example shown in Figure 11. Tube bundles can be designed with 19 or 7 tubes concentrically grouped in the pipe. The terminology around these can be confusing as tube bundles are sometimes sold as straightening vanes, but both fall into the category of flow straightener as described in AGA 3.
These types of flow conditioners are designed to remove swirl with their elongated dimensions. But since they are low blockages, they do very little to correct he asymmetry in the flow profile. In fact, Mattingly and Yeh also showed that flow straighteners can actually make asymmetry a more persistent flow disturbance, lasting much longer in terms of distance. This is because the flow straighteners will capture the asymmetry entering each tube and reduce the type 2 swirl. By reducing the type 2 swirl, the natural turbulence is diminished and the asymmetry does not break down as quickly.
In short, flow straighteners are not recommended for orifice plate measurement.
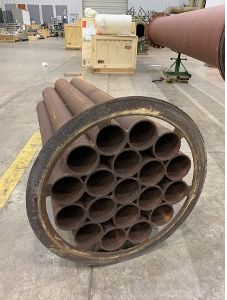

Isolating flow conditioners
Isolating flow conditioners have a blockage factor that forces the flow profile to redistribute as it passes through. This redistribution controls both the asymmetry and swirl disturbances. The design is typically a perforated plate with multiple holes designed to create a well-developed flow profile as soon as possible after the plate.
The search for the ideal pattern of holes to do this job was the subject of much research in the 1990’s as the need for flow conditioning became more and more relevant. A summary of the research from researchers such as Laws, Karnik, Zanker, Gallagher and others is fascinating but outside the scope of this paper. The most widely accepted design of this research was developed by Laws and has become known as the NOVA 50E design.
The NOVA 50E design, Figure 12, is a multi-hole flow conditioner with concentric rings of openings. 16 smaller holes around 8 midsized holes around one large central opening. The size and position of each hole is meant to stimulate the formation of a well-developed flow profile regardless of upstream disturbances. The “50” designation indicates that the plate has approximately a 50% blockage area in the flow path. The success of this design is the balance of three factors: 1) enough blockage to redistribute the flow profile, 2) large enough holes to allow passage of particles and 3) enough opening to reduce the pressure loss across the plate as much as possible. The NOVA design meets the requirements of AGA 3 Section 2.5.5 and APPENDIX 2-D.
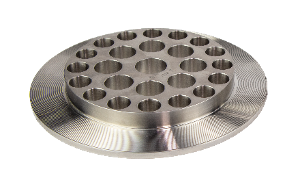
The design is universal for all flow conditions and disturbances. This advantage means a user can have one design flow conditioner for various pipeline installations and conditions. And it gives the user the assurance that most flow disturbances will be removed prior to flow measurement. For as much testing and research has been done of the effects of flow disturbances in a pipe, a user does not know the flow regime and development of their flow profile. Having a flow conditioner improves orifice plate measurement in all standard applications.
Conclusion
The use of a flow conditioner is recommended for all high accuracy orifice plate measurements. The recommended type of flow conditioner is the NOVA 50E design to remove most flow disturbances such as asymmetry and swirl. And users will benefit from the assurance that a well-designed flow conditioner will remove any unknown flow disturbances and problems that could diminish their measurement accuracy.
[1] Effects of pipe elbows and tube bundles onselected types of flowmeters, G.E. Mattingly, T.T. Yeh, Flow Measurement Instrumentation, Vol 2, January 1991
[2] US Patent 5,341,848 “Flow Conditioner”, 1994
Abstract
This paper discusses the effects of poor installations on orifice measurement and the best practices to achieve highest accuracy and performance. Flow disturbances are everywhere in pipelines and industrial applications. Knowing the types of disturbances, their effect on orifice measurement and how to correct those errors is valuable for anyone interested in accurate orifice flow measurement.
What is “Good” Flow
Most flowmeters are affected by the flow that they are trying to measure, orifice plate flowmeters included. Orifice plates measure best in “good” flow conditions and lose accuracy in “bad” conditions. There are several methods to describe and characterize good vs. bad flow conditions. When asked to describe good flow conditions, many users will use the term Laminar. This is a common yet minor misconception in flow engineering.
Laminar vs. Turbulent Flow
Laminar is a flow regime where the flow follows relatively straight lines down a pipe, Figure 1. If you were to follow a particle in the flow, it would go in a straight path and not cross paths with other particles flowing next to it. This is a regime with no turbulence. Laminar flow will happen in low flow and/or high viscous applications. In other words, the momentum forces are low and/or the viscous forces are high. Inherently this makes sense as higher velocities will encourage turbulence and higher viscosities will do the opposite.
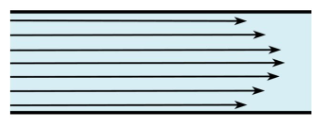
As useful tool is the Reynolds number, which is a dimensionless number used to quantify whether a flow application is in laminar flow. The Reynolds number equations is a follows:
Re=VρD/μ
Re = Reynolds number, dimensionless
V = flow velocity, ft/s
ρ = density, lbm/ft3
μ = dynamic viscosity, lbm/s·ft
The numerator of this equation combines the momentum forces in the flow, velocity, density and size. While the denominator are the inertial forces, viscosity. This follows the logic described earlier. The lower the Reynolds number, the more likely the flow regime is in a laminar state. Laminar flow is more likely to exist where the velocity, density or size is small, and/or where the viscosity is high. The commonly accepted value of laminar flow is Re < 4000. As the Reynolds number increases, the flow regime enters a transition phase between 4000 and 10,000. Above 10,000, the flow regime is considered to be turbulent.
Reynolds number - Flow regime
0 – 4,000 - Laminar
4000 – 10,000 - Transition
>10,000 - Turbulent
Turbulent flow, Figure 2, is the opposite of laminar flow in that the flow streams do not follow a straight or regular pattern. In turbulent flow the flow streams cross, small eddies occur, and mixing is more common. The word “turbulent” rightfully has negative connotations. No one wants to be on an airplane and fly through turbulence.
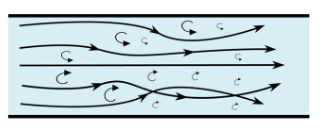
So why is Laminar the incorrect term to describe good flow? It’s not. It’s just not the world in which our flowmeters live. The vast majority of industrial pipelines are in the turbulent flow regime. Virtually all gas flows are turbulent due to the high velocities and low viscosities. Even most liquid flows are turbulent, except for some high viscosity products such as crude oil. Turbulent flow is better for orifice measurement because orifice plates were designed to measure it and their performance is well understood in those conditions.
A side note: Reynolds number is a very helpful in flow measurement. Since it is a dimensionless number, Reynolds can use a single number to describe a flow application. And that number can be used across applications. If the Reynolds number for an application is below 4000, that application is in the laminar flow regime, regardless of the size for example. Reynolds number is used when calibrating a flowmeter. Since the Reynolds number describes the flow in a single number, users can calibrate on one fluid and use the flowmeter in another fluid, knowing the performance will match at equal Reynolds numbers.
Flow profile
A better way to describe understand good vs. bad flow is the presence or absence of flow disturbances. Long, straight, unobstructed pipe will create undisturbed flow. The addition of common pipe elements will create disturbances. Common pipe elements can include single elbows, tees, two elbows in series, partially closed valves, pipe reductions or expansions, thermowells, and many more.
Just like the Reynolds number is a tool to understand the flow regime, the flow profile is a tool to visualize whether flow is disturbed or not. The flow profile attempts to show the velocity at difference points across the diameter of a flowing pipe. This can be physically measured in several ways such as with a single point Pitot tube sensor or with more complex tools such as laser doppler velocimetry. Typically, the view is across a full diameter, crossing through the midpoint of the pipe. A typical flow profile looks like Figure 3 for turbulent flow. Each arrow represents the velocity at points across a diameter of the pipe. The velocities are higher in the center of the pipe and lower near the pipe walls.
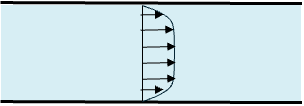
The friction on the pipe walls causes drag which slows down the fluid flow nearest to it. As the flow continues down the pipe, the next layer away from the pipe wall is slowed down slightly less. And so on until the effect of the pipe wall friction no longer affects the velocity. This is called the boundary layer effect and is created whenever flow passes over a surface. Notice the shape of the Figure 3 profile in turbulent flow is different than the shape in Figure 1. Laminar flow has a characteristic “bullet” shaped profile and turbulent has a flatter shape.
Well-developed flow is created when the boundary layer is fully established without disturbances. Put another way, well developed flow will not change its profile as it moves down the pipe. In the industrial flow measurement world, it’s also the definition of good flow and is very important in understanding flow through an orifice.
Power law estimation
When comparing whether a flow profile is well developed or not, a useful tool is the power law estimation. The power law gives a numerical estimation of a well-developed profile. The power law equation is:
u/umax = (1-r/R)1/n
u = velocity at measurement point
umax = max velocity in pipe
r = radius at measurement point
R = pipe radius
n = power
A value of n = 7 is typically used to fit the velocity profile for fully developed, turbulent flows. A higher value of n creates a flatter profile. A lower value creates a more bullet shape profile associated with laminar flow. A power law curve where
n = 7 is shown in Figure 4.
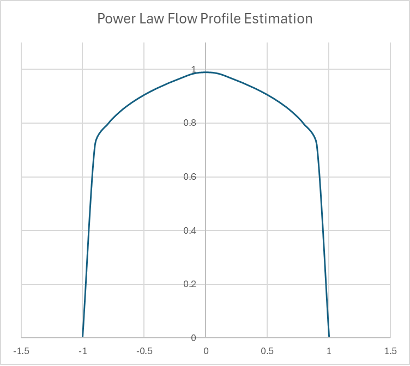
As flow is disturbed with the addition of pipe elements, the flow profile will change. For example, flow through a single elbow creates a skewed profile. The high velocity “core” of the pipe will be pushed to the opposite wall of the pipe, creating an asymmetry where the maximum velocity is no longer in the middle of the pipe. Single elbows and other elements can create asymmetry in the flow profile which is shown well in Figure 5.
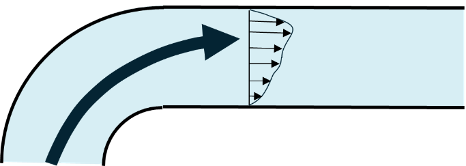
Swirling flow
The flow profile does not capture another type of flow disturbance called swirling flow. Swirling flow is when the flow has a crossflow element. Without swirl the flow will run straight down the pipe, with 0° in relation to the centerline of the pipe. If crossflow is present, the flow streams can have a swirl angle, up to 20° in severe cases.
There are two general types of swirl disturbances, Type 1 and Type 2 swirls. Type 1 swirl moves in one directional rotation across the pipe. This is also known as whole body swirl, Figure 6. Close coupled double elbows out of plane are a common cause of Type 1 swirl, along with headers, pumps and compressors. Type 2 swirl introduces two counter rotating swirls rotating in opposite directions, Figure 7. This is usually created after single elbows.
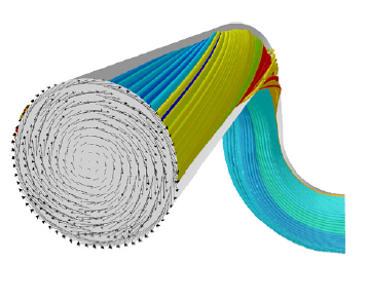
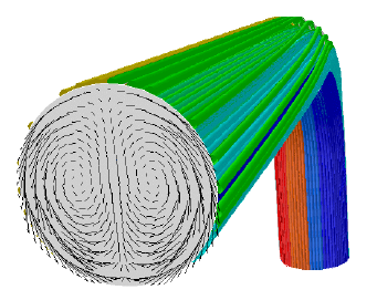
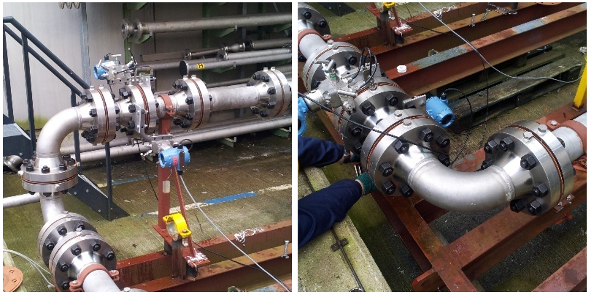
Orifice plate flow measurements
Orifice plates measurement have a century-long track record of continuous use and improvement in industrial applications. No other flow technology has the international volume of understanding and acceptance as orifice plates. Orifice plates are often described as “a hole in a plate” and often ridiculed for that simplicity. Yet it is the simplicity of an orifice plate that makes it so elegant. Leonardo da Vinci once said, “Simplicity is the ultimate sophistication”. The design of the orifice plate makes it possible to manufacture with precision and repeatability. Making one orifice plate measure the same as the next one with matching dimensions. A dimensional inspection is all that is needed to “calibrate” an orifice plate.
Knowing that two identical orifice plates will measure the same (within known uncertainties) is one of the reasons why they are the most widely used industrial flow technology even after 100 years. In today’s world, a user can replace an orifice plate and know the uncertainty of the measurement will not change, even without a flow calibration – something no other flow technology can match!
This also means that a flow calibration once done on a known orifice plate size, can be applied to all other matching orifice plates. Over the decades a massive database of traceable orifice calibrations was completed and used to create the de facto standards for orifice flow measurement. The American standards are the AGA Report No 3 and API 14.3 standards for natural measurement using an orifice plate. The international standard for orifice plates is ISO 5167.
The orifice performance in that technical database (which includes over 30,000 data points!) was tested in well-developed flow conditions. The standards confirm that measurement in matching conditions and dimensions will perform at custody transfer levels of accuracy. And since all the data points were tested in well-developed flow conditions, the standards require the same for accurate measurement.
Effect of flow disturbances on orifice measurement
If a user’s flow conditions are not well developed, with asymmetric or swirling flow, the accuracy will be affected. The effect on accuracy will depend on several factors, including the type of disturbance and the relative distance of the disturbance to the orifice location.
As the distance from the disturbance to the orifice plate increases, the flow will naturally return to a well-developed state due to the turbulence in the flow (turbulence helps us here). The distance needed to return to well-developed flow depends mostly on the type of disturbance. The AGA/API standards recommend up to 44 pipe diameters of straight pipe after double elbow to achieve well developed flow.
Shown below are two sets of flow calibration data from Mattingly and Yeh measuring three different orifice bore sizes (beta ratios) at various distances from a disturbance. Figure 8 shows single elbow effects.Figure 9 shows effects from close coupled, double elbows out of plane.
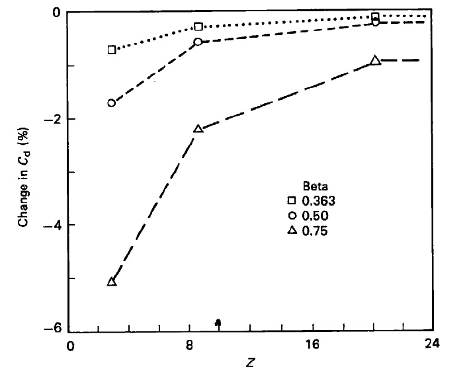
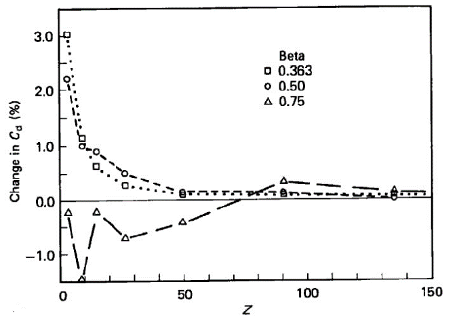
The effect of the disturbance diminishes with distance, approaching zero effect. Notice the effects on accuracy of the orifice plate measurement can be up to 5% after a single elbow using a high beta ratio. The effect lessens using smaller beta ratios. Also notice the x-axis scale of the double elbows chart is much larger than the single elbow chart. This confirms that Type 1 swirl has a much longer lasting impact on flow measurement than Type 2 swirl.
Improving flow conditions
A user can make a determination about their installation knowing the above information. They have three options available to them:
- The user could plan the measurement point as far as possible from the disturbance. The more distance means the more likely the flow is well developed at that point. Some users may have plenty of straight pipe in their system and can meet the minimum requirements in the standards. For most users, creating the necessary straight inlet piping will come with additional expense.
- The user can accept the additional uncertainty that comes with a bad installation. This might be a fine solution in applications with low accuracy requirements. But most industrial applications cannot accept accuracy shifts on the order of ±5%.
- The user could follow the most common practice in the industry: use a flow conditioner.
Flow conditioners
The user of flow conditioners is an industry best practice for ensuring optimal flow measurement with an orifice plate. Flow conditioners come in a variety of designs but have one common goal: to condition the flow to well-developed conditions ahead of an orifice flow measurement point regardless of the disturbance ahead of it.
In the AGA Report No. 3, Section 2.3.1.7 “Flow Conditioners” classifies flow conditioners into two categories: straighteners and isolating flow conditioners.
“Flow straighteners are devices that effectively remove or reduce the swirl component of a flowing stream but may have limited ability to produce the flow conditions necessary to accurately replicate the orifice plate coefficient of discharge database values. Isolating flow conditioners are devices that effectively remove the swirl component from the flowing stream while redistributing the stream to produce the flow conditions that accurately replicate the orifice plate coefficient of discharge database values.”
Flow straighteners
Flow straighteners are low blockage, swirling reducing flow conditioners. Common examples of flow straighteners are tube bundles, example shown in Figure 10 and fin-type straightening vanes, example shown in Figure 11. Tube bundles can be designed with 19 or 7 tubes concentrically grouped in the pipe. The terminology around these can be confusing as tube bundles are sometimes sold as straightening vanes, but both fall into the category of flow straightener as described in AGA 3.
These types of flow conditioners are designed to remove swirl with their elongated dimensions. But since they are low blockages, they do very little to correct he asymmetry in the flow profile. In fact, Mattingly and Yeh also showed that flow straighteners can actually make asymmetry a more persistent flow disturbance, lasting much longer in terms of distance. This is because the flow straighteners will capture the asymmetry entering each tube and reduce the type 2 swirl. By reducing the type 2 swirl, the natural turbulence is diminished and the asymmetry does not break down as quickly.
In short, flow straighteners are not recommended for orifice plate measurement.
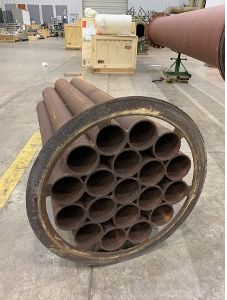

Isolating flow conditioners
Isolating flow conditioners have a blockage factor that forces the flow profile to redistribute as it passes through. This redistribution controls both the asymmetry and swirl disturbances. The design is typically a perforated plate with multiple holes designed to create a well-developed flow profile as soon as possible after the plate.
The search for the ideal pattern of holes to do this job was the subject of much research in the 1990’s as the need for flow conditioning became more and more relevant. A summary of the research from researchers such as Laws, Karnik, Zanker, Gallagher and others is fascinating but outside the scope of this paper. The most widely accepted design of this research was developed by Laws and has become known as the NOVA 50E design.
The NOVA 50E design, Figure 12, is a multi-hole flow conditioner with concentric rings of openings. 16 smaller holes around 8 midsized holes around one large central opening. The size and position of each hole is meant to stimulate the formation of a well-developed flow profile regardless of upstream disturbances. The “50” designation indicates that the plate has approximately a 50% blockage area in the flow path. The success of this design is the balance of three factors: 1) enough blockage to redistribute the flow profile, 2) large enough holes to allow passage of particles and 3) enough opening to reduce the pressure loss across the plate as much as possible. The NOVA design meets the requirements of AGA 3 Section 2.5.5 and APPENDIX 2-D.
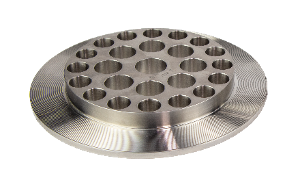
The design is universal for all flow conditions and disturbances. This advantage means a user can have one design flow conditioner for various pipeline installations and conditions. And it gives the user the assurance that most flow disturbances will be removed prior to flow measurement. For as much testing and research has been done of the effects of flow disturbances in a pipe, a user does not know the flow regime and development of their flow profile. Having a flow conditioner improves orifice plate measurement in all standard applications.
Conclusion
The use of a flow conditioner is recommended for all high accuracy orifice plate measurements. The recommended type of flow conditioner is the NOVA 50E design to remove most flow disturbances such as asymmetry and swirl. And users will benefit from the assurance that a well-designed flow conditioner will remove any unknown flow disturbances and problems that could diminish their measurement accuracy.
[1] Effects of pipe elbows and tube bundles onselected types of flowmeters, G.E. Mattingly, T.T. Yeh, Flow Measurement Instrumentation, Vol 2, January 1991
[2] US Patent 5,341,848 “Flow Conditioner”, 1994
Abstract
This paper discusses the effects of poor installations on orifice measurement and the best practices to achieve highest accuracy and performance. Flow disturbances are everywhere in pipelines and industrial applications. Knowing the types of disturbances, their effect on orifice measurement and how to correct those errors is valuable for anyone interested in accurate orifice flow measurement.
What is “Good” Flow
Most flowmeters are affected by the flow that they are trying to measure, orifice plate flowmeters included. Orifice plates measure best in “good” flow conditions and lose accuracy in “bad” conditions. There are several methods to describe and characterize good vs. bad flow conditions. When asked to describe good flow conditions, many users will use the term Laminar. This is a common yet minor misconception in flow engineering.
Laminar vs. Turbulent Flow
Laminar is a flow regime where the flow follows relatively straight lines down a pipe, Figure 1. If you were to follow a particle in the flow, it would go in a straight path and not cross paths with other particles flowing next to it. This is a regime with no turbulence. Laminar flow will happen in low flow and/or high viscous applications. In other words, the momentum forces are low and/or the viscous forces are high. Inherently this makes sense as higher velocities will encourage turbulence and higher viscosities will do the opposite.
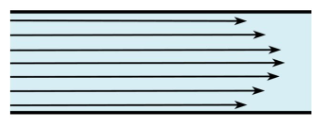
As useful tool is the Reynolds number, which is a dimensionless number used to quantify whether a flow application is in laminar flow. The Reynolds number equations is a follows:
Re=VρD/μ
Re = Reynolds number, dimensionless
V = flow velocity, ft/s
ρ = density, lbm/ft3
μ = dynamic viscosity, lbm/s·ft
The numerator of this equation combines the momentum forces in the flow, velocity, density and size. While the denominator are the inertial forces, viscosity. This follows the logic described earlier. The lower the Reynolds number, the more likely the flow regime is in a laminar state. Laminar flow is more likely to exist where the velocity, density or size is small, and/or where the viscosity is high. The commonly accepted value of laminar flow is Re < 4000. As the Reynolds number increases, the flow regime enters a transition phase between 4000 and 10,000. Above 10,000, the flow regime is considered to be turbulent.
Reynolds number - Flow regime
0 – 4,000 - Laminar
4000 – 10,000 - Transition
>10,000 - Turbulent
Turbulent flow, Figure 2, is the opposite of laminar flow in that the flow streams do not follow a straight or regular pattern. In turbulent flow the flow streams cross, small eddies occur, and mixing is more common. The word “turbulent” rightfully has negative connotations. No one wants to be on an airplane and fly through turbulence.
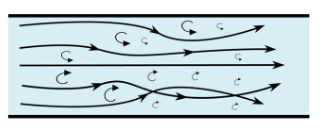
So why is Laminar the incorrect term to describe good flow? It’s not. It’s just not the world in which our flowmeters live. The vast majority of industrial pipelines are in the turbulent flow regime. Virtually all gas flows are turbulent due to the high velocities and low viscosities. Even most liquid flows are turbulent, except for some high viscosity products such as crude oil. Turbulent flow is better for orifice measurement because orifice plates were designed to measure it and their performance is well understood in those conditions.
A side note: Reynolds number is a very helpful in flow measurement. Since it is a dimensionless number, Reynolds can use a single number to describe a flow application. And that number can be used across applications. If the Reynolds number for an application is below 4000, that application is in the laminar flow regime, regardless of the size for example. Reynolds number is used when calibrating a flowmeter. Since the Reynolds number describes the flow in a single number, users can calibrate on one fluid and use the flowmeter in another fluid, knowing the performance will match at equal Reynolds numbers.
Flow profile
A better way to describe understand good vs. bad flow is the presence or absence of flow disturbances. Long, straight, unobstructed pipe will create undisturbed flow. The addition of common pipe elements will create disturbances. Common pipe elements can include single elbows, tees, two elbows in series, partially closed valves, pipe reductions or expansions, thermowells, and many more.
Just like the Reynolds number is a tool to understand the flow regime, the flow profile is a tool to visualize whether flow is disturbed or not. The flow profile attempts to show the velocity at difference points across the diameter of a flowing pipe. This can be physically measured in several ways such as with a single point Pitot tube sensor or with more complex tools such as laser doppler velocimetry. Typically, the view is across a full diameter, crossing through the midpoint of the pipe. A typical flow profile looks like Figure 3 for turbulent flow. Each arrow represents the velocity at points across a diameter of the pipe. The velocities are higher in the center of the pipe and lower near the pipe walls.
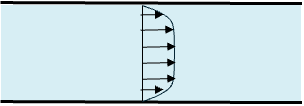
The friction on the pipe walls causes drag which slows down the fluid flow nearest to it. As the flow continues down the pipe, the next layer away from the pipe wall is slowed down slightly less. And so on until the effect of the pipe wall friction no longer affects the velocity. This is called the boundary layer effect and is created whenever flow passes over a surface. Notice the shape of the Figure 3 profile in turbulent flow is different than the shape in Figure 1. Laminar flow has a characteristic “bullet” shaped profile and turbulent has a flatter shape.
Well-developed flow is created when the boundary layer is fully established without disturbances. Put another way, well developed flow will not change its profile as it moves down the pipe. In the industrial flow measurement world, it’s also the definition of good flow and is very important in understanding flow through an orifice.
Power law estimation
When comparing whether a flow profile is well developed or not, a useful tool is the power law estimation. The power law gives a numerical estimation of a well-developed profile. The power law equation is:
u/umax = (1-r/R)1/n
u = velocity at measurement point
umax = max velocity in pipe
r = radius at measurement point
R = pipe radius
n = power
A value of n = 7 is typically used to fit the velocity profile for fully developed, turbulent flows. A higher value of n creates a flatter profile. A lower value creates a more bullet shape profile associated with laminar flow. A power law curve where
n = 7 is shown in Figure 4.
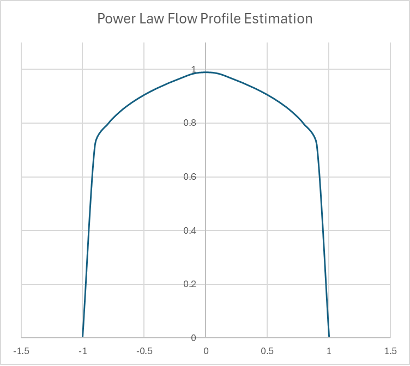
As flow is disturbed with the addition of pipe elements, the flow profile will change. For example, flow through a single elbow creates a skewed profile. The high velocity “core” of the pipe will be pushed to the opposite wall of the pipe, creating an asymmetry where the maximum velocity is no longer in the middle of the pipe. Single elbows and other elements can create asymmetry in the flow profile which is shown well in Figure 5.
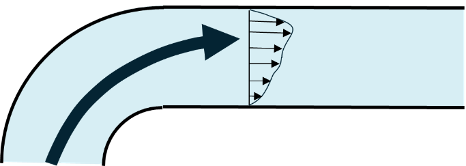
Swirling flow
The flow profile does not capture another type of flow disturbance called swirling flow. Swirling flow is when the flow has a crossflow element. Without swirl the flow will run straight down the pipe, with 0° in relation to the centerline of the pipe. If crossflow is present, the flow streams can have a swirl angle, up to 20° in severe cases.
There are two general types of swirl disturbances, Type 1 and Type 2 swirls. Type 1 swirl moves in one directional rotation across the pipe. This is also known as whole body swirl, Figure 6. Close coupled double elbows out of plane are a common cause of Type 1 swirl, along with headers, pumps and compressors. Type 2 swirl introduces two counter rotating swirls rotating in opposite directions, Figure 7. This is usually created after single elbows.
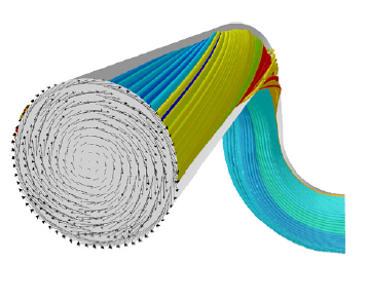
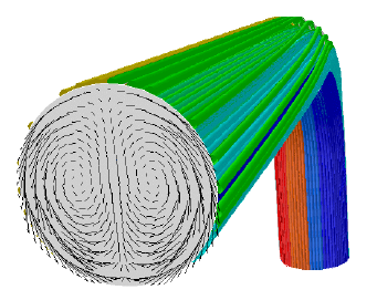
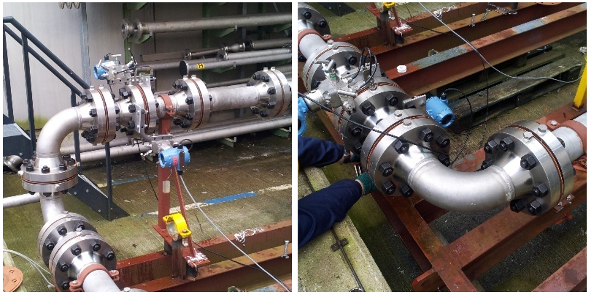
Orifice plate flow measurements
Orifice plates measurement have a century-long track record of continuous use and improvement in industrial applications. No other flow technology has the international volume of understanding and acceptance as orifice plates. Orifice plates are often described as “a hole in a plate” and often ridiculed for that simplicity. Yet it is the simplicity of an orifice plate that makes it so elegant. Leonardo da Vinci once said, “Simplicity is the ultimate sophistication”. The design of the orifice plate makes it possible to manufacture with precision and repeatability. Making one orifice plate measure the same as the next one with matching dimensions. A dimensional inspection is all that is needed to “calibrate” an orifice plate.
Knowing that two identical orifice plates will measure the same (within known uncertainties) is one of the reasons why they are the most widely used industrial flow technology even after 100 years. In today’s world, a user can replace an orifice plate and know the uncertainty of the measurement will not change, even without a flow calibration – something no other flow technology can match!
This also means that a flow calibration once done on a known orifice plate size, can be applied to all other matching orifice plates. Over the decades a massive database of traceable orifice calibrations was completed and used to create the de facto standards for orifice flow measurement. The American standards are the AGA Report No 3 and API 14.3 standards for natural measurement using an orifice plate. The international standard for orifice plates is ISO 5167.
The orifice performance in that technical database (which includes over 30,000 data points!) was tested in well-developed flow conditions. The standards confirm that measurement in matching conditions and dimensions will perform at custody transfer levels of accuracy. And since all the data points were tested in well-developed flow conditions, the standards require the same for accurate measurement.
Effect of flow disturbances on orifice measurement
If a user’s flow conditions are not well developed, with asymmetric or swirling flow, the accuracy will be affected. The effect on accuracy will depend on several factors, including the type of disturbance and the relative distance of the disturbance to the orifice location.
As the distance from the disturbance to the orifice plate increases, the flow will naturally return to a well-developed state due to the turbulence in the flow (turbulence helps us here). The distance needed to return to well-developed flow depends mostly on the type of disturbance. The AGA/API standards recommend up to 44 pipe diameters of straight pipe after double elbow to achieve well developed flow.
Shown below are two sets of flow calibration data from Mattingly and Yeh measuring three different orifice bore sizes (beta ratios) at various distances from a disturbance. Figure 8 shows single elbow effects.Figure 9 shows effects from close coupled, double elbows out of plane.
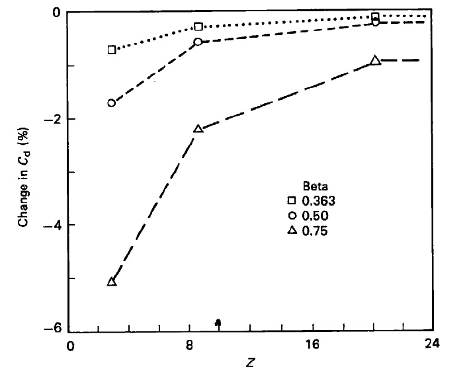
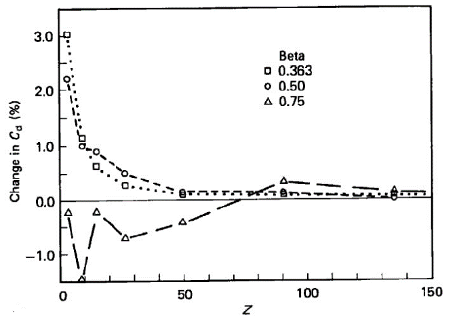
The effect of the disturbance diminishes with distance, approaching zero effect. Notice the effects on accuracy of the orifice plate measurement can be up to 5% after a single elbow using a high beta ratio. The effect lessens using smaller beta ratios. Also notice the x-axis scale of the double elbows chart is much larger than the single elbow chart. This confirms that Type 1 swirl has a much longer lasting impact on flow measurement than Type 2 swirl.
Improving flow conditions
A user can make a determination about their installation knowing the above information. They have three options available to them:
- The user could plan the measurement point as far as possible from the disturbance. The more distance means the more likely the flow is well developed at that point. Some users may have plenty of straight pipe in their system and can meet the minimum requirements in the standards. For most users, creating the necessary straight inlet piping will come with additional expense.
- The user can accept the additional uncertainty that comes with a bad installation. This might be a fine solution in applications with low accuracy requirements. But most industrial applications cannot accept accuracy shifts on the order of ±5%.
- The user could follow the most common practice in the industry: use a flow conditioner.
Flow conditioners
The user of flow conditioners is an industry best practice for ensuring optimal flow measurement with an orifice plate. Flow conditioners come in a variety of designs but have one common goal: to condition the flow to well-developed conditions ahead of an orifice flow measurement point regardless of the disturbance ahead of it.
In the AGA Report No. 3, Section 2.3.1.7 “Flow Conditioners” classifies flow conditioners into two categories: straighteners and isolating flow conditioners.
“Flow straighteners are devices that effectively remove or reduce the swirl component of a flowing stream but may have limited ability to produce the flow conditions necessary to accurately replicate the orifice plate coefficient of discharge database values. Isolating flow conditioners are devices that effectively remove the swirl component from the flowing stream while redistributing the stream to produce the flow conditions that accurately replicate the orifice plate coefficient of discharge database values.”
Flow straighteners
Flow straighteners are low blockage, swirling reducing flow conditioners. Common examples of flow straighteners are tube bundles, example shown in Figure 10 and fin-type straightening vanes, example shown in Figure 11. Tube bundles can be designed with 19 or 7 tubes concentrically grouped in the pipe. The terminology around these can be confusing as tube bundles are sometimes sold as straightening vanes, but both fall into the category of flow straightener as described in AGA 3.
These types of flow conditioners are designed to remove swirl with their elongated dimensions. But since they are low blockages, they do very little to correct he asymmetry in the flow profile. In fact, Mattingly and Yeh also showed that flow straighteners can actually make asymmetry a more persistent flow disturbance, lasting much longer in terms of distance. This is because the flow straighteners will capture the asymmetry entering each tube and reduce the type 2 swirl. By reducing the type 2 swirl, the natural turbulence is diminished and the asymmetry does not break down as quickly.
In short, flow straighteners are not recommended for orifice plate measurement.
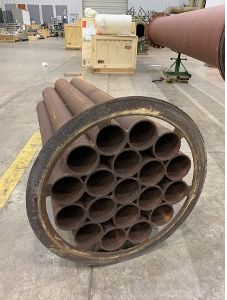

Isolating flow conditioners
Isolating flow conditioners have a blockage factor that forces the flow profile to redistribute as it passes through. This redistribution controls both the asymmetry and swirl disturbances. The design is typically a perforated plate with multiple holes designed to create a well-developed flow profile as soon as possible after the plate.
The search for the ideal pattern of holes to do this job was the subject of much research in the 1990’s as the need for flow conditioning became more and more relevant. A summary of the research from researchers such as Laws, Karnik, Zanker, Gallagher and others is fascinating but outside the scope of this paper. The most widely accepted design of this research was developed by Laws and has become known as the NOVA 50E design.
The NOVA 50E design, Figure 12, is a multi-hole flow conditioner with concentric rings of openings. 16 smaller holes around 8 midsized holes around one large central opening. The size and position of each hole is meant to stimulate the formation of a well-developed flow profile regardless of upstream disturbances. The “50” designation indicates that the plate has approximately a 50% blockage area in the flow path. The success of this design is the balance of three factors: 1) enough blockage to redistribute the flow profile, 2) large enough holes to allow passage of particles and 3) enough opening to reduce the pressure loss across the plate as much as possible. The NOVA design meets the requirements of AGA 3 Section 2.5.5 and APPENDIX 2-D.
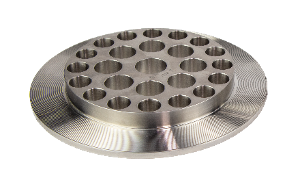
The design is universal for all flow conditions and disturbances. This advantage means a user can have one design flow conditioner for various pipeline installations and conditions. And it gives the user the assurance that most flow disturbances will be removed prior to flow measurement. For as much testing and research has been done of the effects of flow disturbances in a pipe, a user does not know the flow regime and development of their flow profile. Having a flow conditioner improves orifice plate measurement in all standard applications.
Conclusion
The use of a flow conditioner is recommended for all high accuracy orifice plate measurements. The recommended type of flow conditioner is the NOVA 50E design to remove most flow disturbances such as asymmetry and swirl. And users will benefit from the assurance that a well-designed flow conditioner will remove any unknown flow disturbances and problems that could diminish their measurement accuracy.
[1] Effects of pipe elbows and tube bundles onselected types of flowmeters, G.E. Mattingly, T.T. Yeh, Flow Measurement Instrumentation, Vol 2, January 1991
[2] US Patent 5,341,848 “Flow Conditioner”, 1994
Abstract
This paper discusses the effects of poor installations on orifice measurement and the best practices to achieve highest accuracy and performance. Flow disturbances are everywhere in pipelines and industrial applications. Knowing the types of disturbances, their effect on orifice measurement and how to correct those errors is valuable for anyone interested in accurate orifice flow measurement.
What is “Good” Flow
Most flowmeters are affected by the flow that they are trying to measure, orifice plate flowmeters included. Orifice plates measure best in “good” flow conditions and lose accuracy in “bad” conditions. There are several methods to describe and characterize good vs. bad flow conditions. When asked to describe good flow conditions, many users will use the term Laminar. This is a common yet minor misconception in flow engineering.
Laminar vs. Turbulent Flow
Laminar is a flow regime where the flow follows relatively straight lines down a pipe, Figure 1. If you were to follow a particle in the flow, it would go in a straight path and not cross paths with other particles flowing next to it. This is a regime with no turbulence. Laminar flow will happen in low flow and/or high viscous applications. In other words, the momentum forces are low and/or the viscous forces are high. Inherently this makes sense as higher velocities will encourage turbulence and higher viscosities will do the opposite.
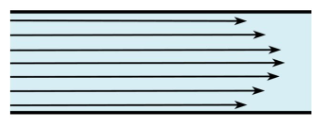
As useful tool is the Reynolds number, which is a dimensionless number used to quantify whether a flow application is in laminar flow. The Reynolds number equations is a follows:
Re=VρD/μ
Re = Reynolds number, dimensionless
V = flow velocity, ft/s
ρ = density, lbm/ft3
μ = dynamic viscosity, lbm/s·ft
The numerator of this equation combines the momentum forces in the flow, velocity, density and size. While the denominator are the inertial forces, viscosity. This follows the logic described earlier. The lower the Reynolds number, the more likely the flow regime is in a laminar state. Laminar flow is more likely to exist where the velocity, density or size is small, and/or where the viscosity is high. The commonly accepted value of laminar flow is Re < 4000. As the Reynolds number increases, the flow regime enters a transition phase between 4000 and 10,000. Above 10,000, the flow regime is considered to be turbulent.
Reynolds number - Flow regime
0 – 4,000 - Laminar
4000 – 10,000 - Transition
>10,000 - Turbulent
Turbulent flow, Figure 2, is the opposite of laminar flow in that the flow streams do not follow a straight or regular pattern. In turbulent flow the flow streams cross, small eddies occur, and mixing is more common. The word “turbulent” rightfully has negative connotations. No one wants to be on an airplane and fly through turbulence.
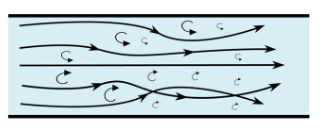
So why is Laminar the incorrect term to describe good flow? It’s not. It’s just not the world in which our flowmeters live. The vast majority of industrial pipelines are in the turbulent flow regime. Virtually all gas flows are turbulent due to the high velocities and low viscosities. Even most liquid flows are turbulent, except for some high viscosity products such as crude oil. Turbulent flow is better for orifice measurement because orifice plates were designed to measure it and their performance is well understood in those conditions.
A side note: Reynolds number is a very helpful in flow measurement. Since it is a dimensionless number, Reynolds can use a single number to describe a flow application. And that number can be used across applications. If the Reynolds number for an application is below 4000, that application is in the laminar flow regime, regardless of the size for example. Reynolds number is used when calibrating a flowmeter. Since the Reynolds number describes the flow in a single number, users can calibrate on one fluid and use the flowmeter in another fluid, knowing the performance will match at equal Reynolds numbers.
Flow profile
A better way to describe understand good vs. bad flow is the presence or absence of flow disturbances. Long, straight, unobstructed pipe will create undisturbed flow. The addition of common pipe elements will create disturbances. Common pipe elements can include single elbows, tees, two elbows in series, partially closed valves, pipe reductions or expansions, thermowells, and many more.
Just like the Reynolds number is a tool to understand the flow regime, the flow profile is a tool to visualize whether flow is disturbed or not. The flow profile attempts to show the velocity at difference points across the diameter of a flowing pipe. This can be physically measured in several ways such as with a single point Pitot tube sensor or with more complex tools such as laser doppler velocimetry. Typically, the view is across a full diameter, crossing through the midpoint of the pipe. A typical flow profile looks like Figure 3 for turbulent flow. Each arrow represents the velocity at points across a diameter of the pipe. The velocities are higher in the center of the pipe and lower near the pipe walls.
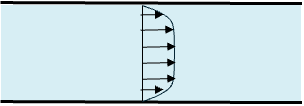
The friction on the pipe walls causes drag which slows down the fluid flow nearest to it. As the flow continues down the pipe, the next layer away from the pipe wall is slowed down slightly less. And so on until the effect of the pipe wall friction no longer affects the velocity. This is called the boundary layer effect and is created whenever flow passes over a surface. Notice the shape of the Figure 3 profile in turbulent flow is different than the shape in Figure 1. Laminar flow has a characteristic “bullet” shaped profile and turbulent has a flatter shape.
Well-developed flow is created when the boundary layer is fully established without disturbances. Put another way, well developed flow will not change its profile as it moves down the pipe. In the industrial flow measurement world, it’s also the definition of good flow and is very important in understanding flow through an orifice.
Power law estimation
When comparing whether a flow profile is well developed or not, a useful tool is the power law estimation. The power law gives a numerical estimation of a well-developed profile. The power law equation is:
u/umax = (1-r/R)1/n
u = velocity at measurement point
umax = max velocity in pipe
r = radius at measurement point
R = pipe radius
n = power
A value of n = 7 is typically used to fit the velocity profile for fully developed, turbulent flows. A higher value of n creates a flatter profile. A lower value creates a more bullet shape profile associated with laminar flow. A power law curve where
n = 7 is shown in Figure 4.
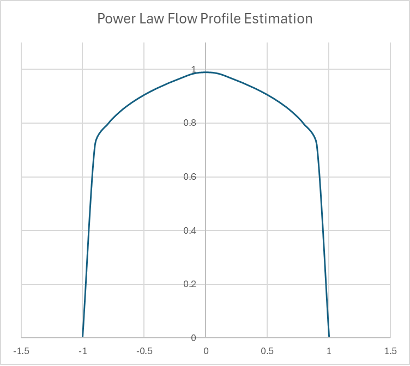
As flow is disturbed with the addition of pipe elements, the flow profile will change. For example, flow through a single elbow creates a skewed profile. The high velocity “core” of the pipe will be pushed to the opposite wall of the pipe, creating an asymmetry where the maximum velocity is no longer in the middle of the pipe. Single elbows and other elements can create asymmetry in the flow profile which is shown well in Figure 5.
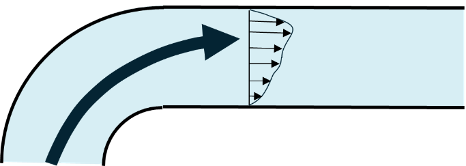
Swirling flow
The flow profile does not capture another type of flow disturbance called swirling flow. Swirling flow is when the flow has a crossflow element. Without swirl the flow will run straight down the pipe, with 0° in relation to the centerline of the pipe. If crossflow is present, the flow streams can have a swirl angle, up to 20° in severe cases.
There are two general types of swirl disturbances, Type 1 and Type 2 swirls. Type 1 swirl moves in one directional rotation across the pipe. This is also known as whole body swirl, Figure 6. Close coupled double elbows out of plane are a common cause of Type 1 swirl, along with headers, pumps and compressors. Type 2 swirl introduces two counter rotating swirls rotating in opposite directions, Figure 7. This is usually created after single elbows.
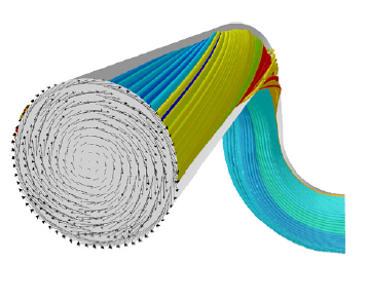
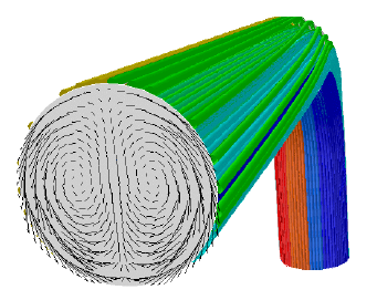
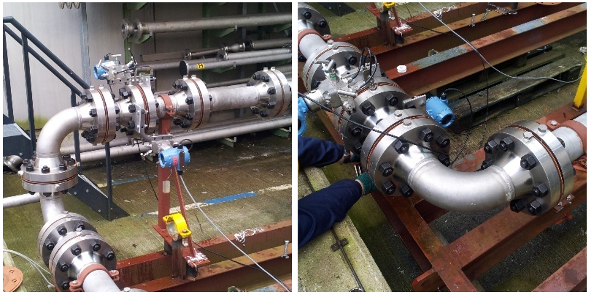
Orifice plate flow measurements
Orifice plates measurement have a century-long track record of continuous use and improvement in industrial applications. No other flow technology has the international volume of understanding and acceptance as orifice plates. Orifice plates are often described as “a hole in a plate” and often ridiculed for that simplicity. Yet it is the simplicity of an orifice plate that makes it so elegant. Leonardo da Vinci once said, “Simplicity is the ultimate sophistication”. The design of the orifice plate makes it possible to manufacture with precision and repeatability. Making one orifice plate measure the same as the next one with matching dimensions. A dimensional inspection is all that is needed to “calibrate” an orifice plate.
Knowing that two identical orifice plates will measure the same (within known uncertainties) is one of the reasons why they are the most widely used industrial flow technology even after 100 years. In today’s world, a user can replace an orifice plate and know the uncertainty of the measurement will not change, even without a flow calibration – something no other flow technology can match!
This also means that a flow calibration once done on a known orifice plate size, can be applied to all other matching orifice plates. Over the decades a massive database of traceable orifice calibrations was completed and used to create the de facto standards for orifice flow measurement. The American standards are the AGA Report No 3 and API 14.3 standards for natural measurement using an orifice plate. The international standard for orifice plates is ISO 5167.
The orifice performance in that technical database (which includes over 30,000 data points!) was tested in well-developed flow conditions. The standards confirm that measurement in matching conditions and dimensions will perform at custody transfer levels of accuracy. And since all the data points were tested in well-developed flow conditions, the standards require the same for accurate measurement.
Effect of flow disturbances on orifice measurement
If a user’s flow conditions are not well developed, with asymmetric or swirling flow, the accuracy will be affected. The effect on accuracy will depend on several factors, including the type of disturbance and the relative distance of the disturbance to the orifice location.
As the distance from the disturbance to the orifice plate increases, the flow will naturally return to a well-developed state due to the turbulence in the flow (turbulence helps us here). The distance needed to return to well-developed flow depends mostly on the type of disturbance. The AGA/API standards recommend up to 44 pipe diameters of straight pipe after double elbow to achieve well developed flow.
Shown below are two sets of flow calibration data from Mattingly and Yeh measuring three different orifice bore sizes (beta ratios) at various distances from a disturbance. Figure 8 shows single elbow effects.Figure 9 shows effects from close coupled, double elbows out of plane.
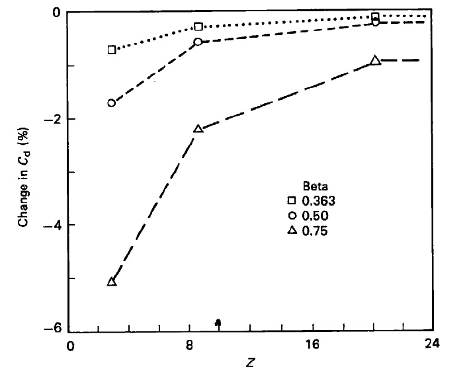
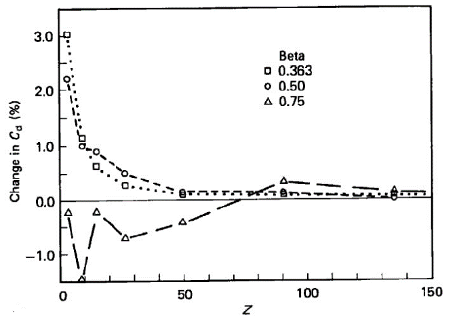
The effect of the disturbance diminishes with distance, approaching zero effect. Notice the effects on accuracy of the orifice plate measurement can be up to 5% after a single elbow using a high beta ratio. The effect lessens using smaller beta ratios. Also notice the x-axis scale of the double elbows chart is much larger than the single elbow chart. This confirms that Type 1 swirl has a much longer lasting impact on flow measurement than Type 2 swirl.
Improving flow conditions
A user can make a determination about their installation knowing the above information. They have three options available to them:
- The user could plan the measurement point as far as possible from the disturbance. The more distance means the more likely the flow is well developed at that point. Some users may have plenty of straight pipe in their system and can meet the minimum requirements in the standards. For most users, creating the necessary straight inlet piping will come with additional expense.
- The user can accept the additional uncertainty that comes with a bad installation. This might be a fine solution in applications with low accuracy requirements. But most industrial applications cannot accept accuracy shifts on the order of ±5%.
- The user could follow the most common practice in the industry: use a flow conditioner.
Flow conditioners
The user of flow conditioners is an industry best practice for ensuring optimal flow measurement with an orifice plate. Flow conditioners come in a variety of designs but have one common goal: to condition the flow to well-developed conditions ahead of an orifice flow measurement point regardless of the disturbance ahead of it.
In the AGA Report No. 3, Section 2.3.1.7 “Flow Conditioners” classifies flow conditioners into two categories: straighteners and isolating flow conditioners.
“Flow straighteners are devices that effectively remove or reduce the swirl component of a flowing stream but may have limited ability to produce the flow conditions necessary to accurately replicate the orifice plate coefficient of discharge database values. Isolating flow conditioners are devices that effectively remove the swirl component from the flowing stream while redistributing the stream to produce the flow conditions that accurately replicate the orifice plate coefficient of discharge database values.”
Flow straighteners
Flow straighteners are low blockage, swirling reducing flow conditioners. Common examples of flow straighteners are tube bundles, example shown in Figure 10 and fin-type straightening vanes, example shown in Figure 11. Tube bundles can be designed with 19 or 7 tubes concentrically grouped in the pipe. The terminology around these can be confusing as tube bundles are sometimes sold as straightening vanes, but both fall into the category of flow straightener as described in AGA 3.
These types of flow conditioners are designed to remove swirl with their elongated dimensions. But since they are low blockages, they do very little to correct he asymmetry in the flow profile. In fact, Mattingly and Yeh also showed that flow straighteners can actually make asymmetry a more persistent flow disturbance, lasting much longer in terms of distance. This is because the flow straighteners will capture the asymmetry entering each tube and reduce the type 2 swirl. By reducing the type 2 swirl, the natural turbulence is diminished and the asymmetry does not break down as quickly.
In short, flow straighteners are not recommended for orifice plate measurement.
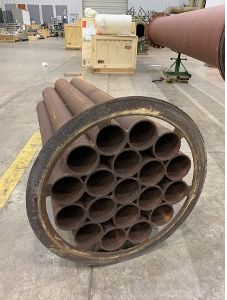

Isolating flow conditioners
Isolating flow conditioners have a blockage factor that forces the flow profile to redistribute as it passes through. This redistribution controls both the asymmetry and swirl disturbances. The design is typically a perforated plate with multiple holes designed to create a well-developed flow profile as soon as possible after the plate.
The search for the ideal pattern of holes to do this job was the subject of much research in the 1990’s as the need for flow conditioning became more and more relevant. A summary of the research from researchers such as Laws, Karnik, Zanker, Gallagher and others is fascinating but outside the scope of this paper. The most widely accepted design of this research was developed by Laws and has become known as the NOVA 50E design.
The NOVA 50E design, Figure 12, is a multi-hole flow conditioner with concentric rings of openings. 16 smaller holes around 8 midsized holes around one large central opening. The size and position of each hole is meant to stimulate the formation of a well-developed flow profile regardless of upstream disturbances. The “50” designation indicates that the plate has approximately a 50% blockage area in the flow path. The success of this design is the balance of three factors: 1) enough blockage to redistribute the flow profile, 2) large enough holes to allow passage of particles and 3) enough opening to reduce the pressure loss across the plate as much as possible. The NOVA design meets the requirements of AGA 3 Section 2.5.5 and APPENDIX 2-D.
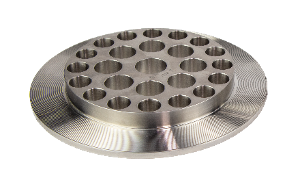
The design is universal for all flow conditions and disturbances. This advantage means a user can have one design flow conditioner for various pipeline installations and conditions. And it gives the user the assurance that most flow disturbances will be removed prior to flow measurement. For as much testing and research has been done of the effects of flow disturbances in a pipe, a user does not know the flow regime and development of their flow profile. Having a flow conditioner improves orifice plate measurement in all standard applications.
Conclusion
The use of a flow conditioner is recommended for all high accuracy orifice plate measurements. The recommended type of flow conditioner is the NOVA 50E design to remove most flow disturbances such as asymmetry and swirl. And users will benefit from the assurance that a well-designed flow conditioner will remove any unknown flow disturbances and problems that could diminish their measurement accuracy.
[1] Effects of pipe elbows and tube bundles onselected types of flowmeters, G.E. Mattingly, T.T. Yeh, Flow Measurement Instrumentation, Vol 2, January 1991
[2] US Patent 5,341,848 “Flow Conditioner”, 1994
Abstract
This paper discusses the effects of poor installations on orifice measurement and the best practices to achieve highest accuracy and performance. Flow disturbances are everywhere in pipelines and industrial applications. Knowing the types of disturbances, their effect on orifice measurement and how to correct those errors is valuable for anyone interested in accurate orifice flow measurement.
What is “Good” Flow
Most flowmeters are affected by the flow that they are trying to measure, orifice plate flowmeters included. Orifice plates measure best in “good” flow conditions and lose accuracy in “bad” conditions. There are several methods to describe and characterize good vs. bad flow conditions. When asked to describe good flow conditions, many users will use the term Laminar. This is a common yet minor misconception in flow engineering.
Laminar vs. Turbulent Flow
Laminar is a flow regime where the flow follows relatively straight lines down a pipe, Figure 1. If you were to follow a particle in the flow, it would go in a straight path and not cross paths with other particles flowing next to it. This is a regime with no turbulence. Laminar flow will happen in low flow and/or high viscous applications. In other words, the momentum forces are low and/or the viscous forces are high. Inherently this makes sense as higher velocities will encourage turbulence and higher viscosities will do the opposite.
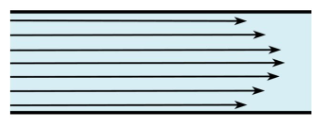
As useful tool is the Reynolds number, which is a dimensionless number used to quantify whether a flow application is in laminar flow. The Reynolds number equations is a follows:
Re=VρD/μ
Re = Reynolds number, dimensionless
V = flow velocity, ft/s
ρ = density, lbm/ft3
μ = dynamic viscosity, lbm/s·ft
The numerator of this equation combines the momentum forces in the flow, velocity, density and size. While the denominator are the inertial forces, viscosity. This follows the logic described earlier. The lower the Reynolds number, the more likely the flow regime is in a laminar state. Laminar flow is more likely to exist where the velocity, density or size is small, and/or where the viscosity is high. The commonly accepted value of laminar flow is Re < 4000. As the Reynolds number increases, the flow regime enters a transition phase between 4000 and 10,000. Above 10,000, the flow regime is considered to be turbulent.
Reynolds number - Flow regime
0 – 4,000 - Laminar
4000 – 10,000 - Transition
>10,000 - Turbulent
Turbulent flow, Figure 2, is the opposite of laminar flow in that the flow streams do not follow a straight or regular pattern. In turbulent flow the flow streams cross, small eddies occur, and mixing is more common. The word “turbulent” rightfully has negative connotations. No one wants to be on an airplane and fly through turbulence.
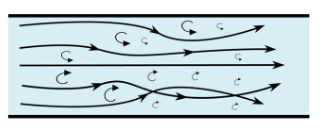
So why is Laminar the incorrect term to describe good flow? It’s not. It’s just not the world in which our flowmeters live. The vast majority of industrial pipelines are in the turbulent flow regime. Virtually all gas flows are turbulent due to the high velocities and low viscosities. Even most liquid flows are turbulent, except for some high viscosity products such as crude oil. Turbulent flow is better for orifice measurement because orifice plates were designed to measure it and their performance is well understood in those conditions.
A side note: Reynolds number is a very helpful in flow measurement. Since it is a dimensionless number, Reynolds can use a single number to describe a flow application. And that number can be used across applications. If the Reynolds number for an application is below 4000, that application is in the laminar flow regime, regardless of the size for example. Reynolds number is used when calibrating a flowmeter. Since the Reynolds number describes the flow in a single number, users can calibrate on one fluid and use the flowmeter in another fluid, knowing the performance will match at equal Reynolds numbers.
Flow profile
A better way to describe understand good vs. bad flow is the presence or absence of flow disturbances. Long, straight, unobstructed pipe will create undisturbed flow. The addition of common pipe elements will create disturbances. Common pipe elements can include single elbows, tees, two elbows in series, partially closed valves, pipe reductions or expansions, thermowells, and many more.
Just like the Reynolds number is a tool to understand the flow regime, the flow profile is a tool to visualize whether flow is disturbed or not. The flow profile attempts to show the velocity at difference points across the diameter of a flowing pipe. This can be physically measured in several ways such as with a single point Pitot tube sensor or with more complex tools such as laser doppler velocimetry. Typically, the view is across a full diameter, crossing through the midpoint of the pipe. A typical flow profile looks like Figure 3 for turbulent flow. Each arrow represents the velocity at points across a diameter of the pipe. The velocities are higher in the center of the pipe and lower near the pipe walls.
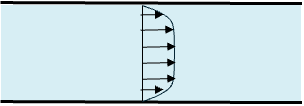
The friction on the pipe walls causes drag which slows down the fluid flow nearest to it. As the flow continues down the pipe, the next layer away from the pipe wall is slowed down slightly less. And so on until the effect of the pipe wall friction no longer affects the velocity. This is called the boundary layer effect and is created whenever flow passes over a surface. Notice the shape of the Figure 3 profile in turbulent flow is different than the shape in Figure 1. Laminar flow has a characteristic “bullet” shaped profile and turbulent has a flatter shape.
Well-developed flow is created when the boundary layer is fully established without disturbances. Put another way, well developed flow will not change its profile as it moves down the pipe. In the industrial flow measurement world, it’s also the definition of good flow and is very important in understanding flow through an orifice.
Power law estimation
When comparing whether a flow profile is well developed or not, a useful tool is the power law estimation. The power law gives a numerical estimation of a well-developed profile. The power law equation is:
u/umax = (1-r/R)1/n
u = velocity at measurement point
umax = max velocity in pipe
r = radius at measurement point
R = pipe radius
n = power
A value of n = 7 is typically used to fit the velocity profile for fully developed, turbulent flows. A higher value of n creates a flatter profile. A lower value creates a more bullet shape profile associated with laminar flow. A power law curve where
n = 7 is shown in Figure 4.
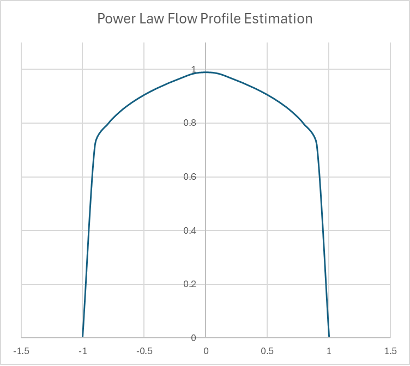
As flow is disturbed with the addition of pipe elements, the flow profile will change. For example, flow through a single elbow creates a skewed profile. The high velocity “core” of the pipe will be pushed to the opposite wall of the pipe, creating an asymmetry where the maximum velocity is no longer in the middle of the pipe. Single elbows and other elements can create asymmetry in the flow profile which is shown well in Figure 5.
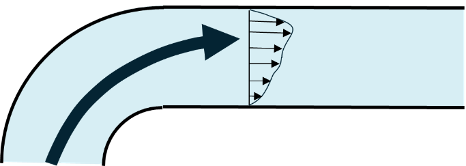
Swirling flow
The flow profile does not capture another type of flow disturbance called swirling flow. Swirling flow is when the flow has a crossflow element. Without swirl the flow will run straight down the pipe, with 0° in relation to the centerline of the pipe. If crossflow is present, the flow streams can have a swirl angle, up to 20° in severe cases.
There are two general types of swirl disturbances, Type 1 and Type 2 swirls. Type 1 swirl moves in one directional rotation across the pipe. This is also known as whole body swirl, Figure 6. Close coupled double elbows out of plane are a common cause of Type 1 swirl, along with headers, pumps and compressors. Type 2 swirl introduces two counter rotating swirls rotating in opposite directions, Figure 7. This is usually created after single elbows.
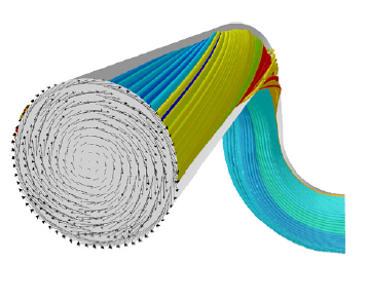
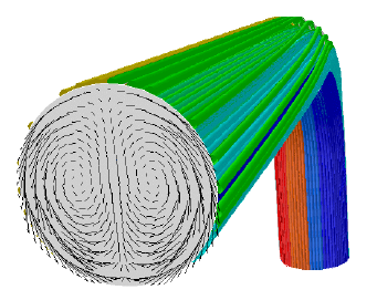
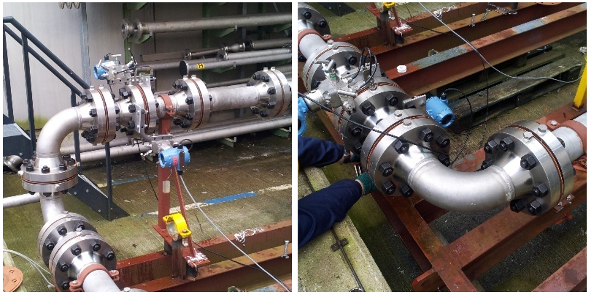
Orifice plate flow measurements
Orifice plates measurement have a century-long track record of continuous use and improvement in industrial applications. No other flow technology has the international volume of understanding and acceptance as orifice plates. Orifice plates are often described as “a hole in a plate” and often ridiculed for that simplicity. Yet it is the simplicity of an orifice plate that makes it so elegant. Leonardo da Vinci once said, “Simplicity is the ultimate sophistication”. The design of the orifice plate makes it possible to manufacture with precision and repeatability. Making one orifice plate measure the same as the next one with matching dimensions. A dimensional inspection is all that is needed to “calibrate” an orifice plate.
Knowing that two identical orifice plates will measure the same (within known uncertainties) is one of the reasons why they are the most widely used industrial flow technology even after 100 years. In today’s world, a user can replace an orifice plate and know the uncertainty of the measurement will not change, even without a flow calibration – something no other flow technology can match!
This also means that a flow calibration once done on a known orifice plate size, can be applied to all other matching orifice plates. Over the decades a massive database of traceable orifice calibrations was completed and used to create the de facto standards for orifice flow measurement. The American standards are the AGA Report No 3 and API 14.3 standards for natural measurement using an orifice plate. The international standard for orifice plates is ISO 5167.
The orifice performance in that technical database (which includes over 30,000 data points!) was tested in well-developed flow conditions. The standards confirm that measurement in matching conditions and dimensions will perform at custody transfer levels of accuracy. And since all the data points were tested in well-developed flow conditions, the standards require the same for accurate measurement.
Effect of flow disturbances on orifice measurement
If a user’s flow conditions are not well developed, with asymmetric or swirling flow, the accuracy will be affected. The effect on accuracy will depend on several factors, including the type of disturbance and the relative distance of the disturbance to the orifice location.
As the distance from the disturbance to the orifice plate increases, the flow will naturally return to a well-developed state due to the turbulence in the flow (turbulence helps us here). The distance needed to return to well-developed flow depends mostly on the type of disturbance. The AGA/API standards recommend up to 44 pipe diameters of straight pipe after double elbow to achieve well developed flow.
Shown below are two sets of flow calibration data from Mattingly and Yeh measuring three different orifice bore sizes (beta ratios) at various distances from a disturbance. Figure 8 shows single elbow effects.Figure 9 shows effects from close coupled, double elbows out of plane.
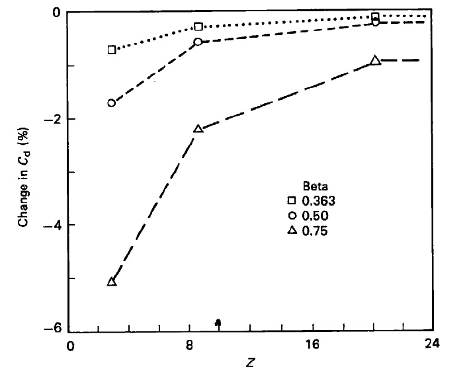
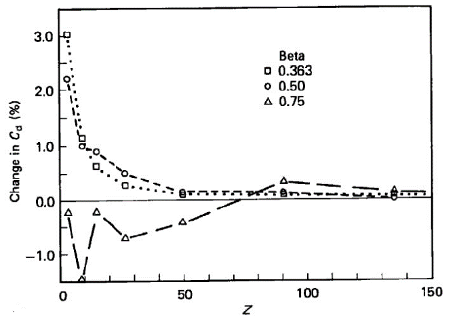
The effect of the disturbance diminishes with distance, approaching zero effect. Notice the effects on accuracy of the orifice plate measurement can be up to 5% after a single elbow using a high beta ratio. The effect lessens using smaller beta ratios. Also notice the x-axis scale of the double elbows chart is much larger than the single elbow chart. This confirms that Type 1 swirl has a much longer lasting impact on flow measurement than Type 2 swirl.
Improving flow conditions
A user can make a determination about their installation knowing the above information. They have three options available to them:
- The user could plan the measurement point as far as possible from the disturbance. The more distance means the more likely the flow is well developed at that point. Some users may have plenty of straight pipe in their system and can meet the minimum requirements in the standards. For most users, creating the necessary straight inlet piping will come with additional expense.
- The user can accept the additional uncertainty that comes with a bad installation. This might be a fine solution in applications with low accuracy requirements. But most industrial applications cannot accept accuracy shifts on the order of ±5%.
- The user could follow the most common practice in the industry: use a flow conditioner.
Flow conditioners
The user of flow conditioners is an industry best practice for ensuring optimal flow measurement with an orifice plate. Flow conditioners come in a variety of designs but have one common goal: to condition the flow to well-developed conditions ahead of an orifice flow measurement point regardless of the disturbance ahead of it.
In the AGA Report No. 3, Section 2.3.1.7 “Flow Conditioners” classifies flow conditioners into two categories: straighteners and isolating flow conditioners.
“Flow straighteners are devices that effectively remove or reduce the swirl component of a flowing stream but may have limited ability to produce the flow conditions necessary to accurately replicate the orifice plate coefficient of discharge database values. Isolating flow conditioners are devices that effectively remove the swirl component from the flowing stream while redistributing the stream to produce the flow conditions that accurately replicate the orifice plate coefficient of discharge database values.”
Flow straighteners
Flow straighteners are low blockage, swirling reducing flow conditioners. Common examples of flow straighteners are tube bundles, example shown in Figure 10 and fin-type straightening vanes, example shown in Figure 11. Tube bundles can be designed with 19 or 7 tubes concentrically grouped in the pipe. The terminology around these can be confusing as tube bundles are sometimes sold as straightening vanes, but both fall into the category of flow straightener as described in AGA 3.
These types of flow conditioners are designed to remove swirl with their elongated dimensions. But since they are low blockages, they do very little to correct he asymmetry in the flow profile. In fact, Mattingly and Yeh also showed that flow straighteners can actually make asymmetry a more persistent flow disturbance, lasting much longer in terms of distance. This is because the flow straighteners will capture the asymmetry entering each tube and reduce the type 2 swirl. By reducing the type 2 swirl, the natural turbulence is diminished and the asymmetry does not break down as quickly.
In short, flow straighteners are not recommended for orifice plate measurement.
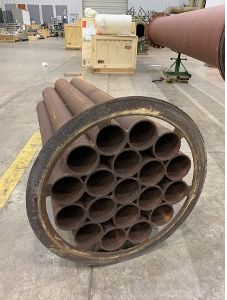

Isolating flow conditioners
Isolating flow conditioners have a blockage factor that forces the flow profile to redistribute as it passes through. This redistribution controls both the asymmetry and swirl disturbances. The design is typically a perforated plate with multiple holes designed to create a well-developed flow profile as soon as possible after the plate.
The search for the ideal pattern of holes to do this job was the subject of much research in the 1990’s as the need for flow conditioning became more and more relevant. A summary of the research from researchers such as Laws, Karnik, Zanker, Gallagher and others is fascinating but outside the scope of this paper. The most widely accepted design of this research was developed by Laws and has become known as the NOVA 50E design.
The NOVA 50E design, Figure 12, is a multi-hole flow conditioner with concentric rings of openings. 16 smaller holes around 8 midsized holes around one large central opening. The size and position of each hole is meant to stimulate the formation of a well-developed flow profile regardless of upstream disturbances. The “50” designation indicates that the plate has approximately a 50% blockage area in the flow path. The success of this design is the balance of three factors: 1) enough blockage to redistribute the flow profile, 2) large enough holes to allow passage of particles and 3) enough opening to reduce the pressure loss across the plate as much as possible. The NOVA design meets the requirements of AGA 3 Section 2.5.5 and APPENDIX 2-D.
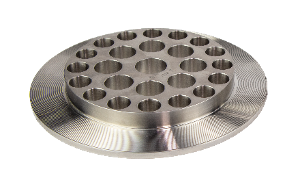
The design is universal for all flow conditions and disturbances. This advantage means a user can have one design flow conditioner for various pipeline installations and conditions. And it gives the user the assurance that most flow disturbances will be removed prior to flow measurement. For as much testing and research has been done of the effects of flow disturbances in a pipe, a user does not know the flow regime and development of their flow profile. Having a flow conditioner improves orifice plate measurement in all standard applications.
Conclusion
The use of a flow conditioner is recommended for all high accuracy orifice plate measurements. The recommended type of flow conditioner is the NOVA 50E design to remove most flow disturbances such as asymmetry and swirl. And users will benefit from the assurance that a well-designed flow conditioner will remove any unknown flow disturbances and problems that could diminish their measurement accuracy.
[1] Effects of pipe elbows and tube bundles onselected types of flowmeters, G.E. Mattingly, T.T. Yeh, Flow Measurement Instrumentation, Vol 2, January 1991
[2] US Patent 5,341,848 “Flow Conditioner”, 1994
Abstract
This paper discusses the effects of poor installations on orifice measurement and the best practices to achieve highest accuracy and performance. Flow disturbances are everywhere in pipelines and industrial applications. Knowing the types of disturbances, their effect on orifice measurement and how to correct those errors is valuable for anyone interested in accurate orifice flow measurement.
What is “Good” Flow
Most flowmeters are affected by the flow that they are trying to measure, orifice plate flowmeters included. Orifice plates measure best in “good” flow conditions and lose accuracy in “bad” conditions. There are several methods to describe and characterize good vs. bad flow conditions. When asked to describe good flow conditions, many users will use the term Laminar. This is a common yet minor misconception in flow engineering.
Laminar vs. Turbulent Flow
Laminar is a flow regime where the flow follows relatively straight lines down a pipe, Figure 1. If you were to follow a particle in the flow, it would go in a straight path and not cross paths with other particles flowing next to it. This is a regime with no turbulence. Laminar flow will happen in low flow and/or high viscous applications. In other words, the momentum forces are low and/or the viscous forces are high. Inherently this makes sense as higher velocities will encourage turbulence and higher viscosities will do the opposite.
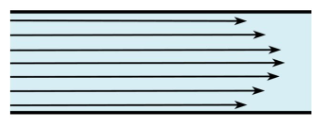
As useful tool is the Reynolds number, which is a dimensionless number used to quantify whether a flow application is in laminar flow. The Reynolds number equations is a follows:
Re=VρD/μ
Re = Reynolds number, dimensionless
V = flow velocity, ft/s
ρ = density, lbm/ft3
μ = dynamic viscosity, lbm/s·ft
The numerator of this equation combines the momentum forces in the flow, velocity, density and size. While the denominator are the inertial forces, viscosity. This follows the logic described earlier. The lower the Reynolds number, the more likely the flow regime is in a laminar state. Laminar flow is more likely to exist where the velocity, density or size is small, and/or where the viscosity is high. The commonly accepted value of laminar flow is Re < 4000. As the Reynolds number increases, the flow regime enters a transition phase between 4000 and 10,000. Above 10,000, the flow regime is considered to be turbulent.
Reynolds number - Flow regime
0 – 4,000 - Laminar
4000 – 10,000 - Transition
>10,000 - Turbulent
Turbulent flow, Figure 2, is the opposite of laminar flow in that the flow streams do not follow a straight or regular pattern. In turbulent flow the flow streams cross, small eddies occur, and mixing is more common. The word “turbulent” rightfully has negative connotations. No one wants to be on an airplane and fly through turbulence.
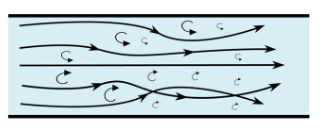
So why is Laminar the incorrect term to describe good flow? It’s not. It’s just not the world in which our flowmeters live. The vast majority of industrial pipelines are in the turbulent flow regime. Virtually all gas flows are turbulent due to the high velocities and low viscosities. Even most liquid flows are turbulent, except for some high viscosity products such as crude oil. Turbulent flow is better for orifice measurement because orifice plates were designed to measure it and their performance is well understood in those conditions.
A side note: Reynolds number is a very helpful in flow measurement. Since it is a dimensionless number, Reynolds can use a single number to describe a flow application. And that number can be used across applications. If the Reynolds number for an application is below 4000, that application is in the laminar flow regime, regardless of the size for example. Reynolds number is used when calibrating a flowmeter. Since the Reynolds number describes the flow in a single number, users can calibrate on one fluid and use the flowmeter in another fluid, knowing the performance will match at equal Reynolds numbers.
Flow profile
A better way to describe understand good vs. bad flow is the presence or absence of flow disturbances. Long, straight, unobstructed pipe will create undisturbed flow. The addition of common pipe elements will create disturbances. Common pipe elements can include single elbows, tees, two elbows in series, partially closed valves, pipe reductions or expansions, thermowells, and many more.
Just like the Reynolds number is a tool to understand the flow regime, the flow profile is a tool to visualize whether flow is disturbed or not. The flow profile attempts to show the velocity at difference points across the diameter of a flowing pipe. This can be physically measured in several ways such as with a single point Pitot tube sensor or with more complex tools such as laser doppler velocimetry. Typically, the view is across a full diameter, crossing through the midpoint of the pipe. A typical flow profile looks like Figure 3 for turbulent flow. Each arrow represents the velocity at points across a diameter of the pipe. The velocities are higher in the center of the pipe and lower near the pipe walls.
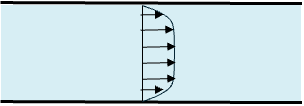
The friction on the pipe walls causes drag which slows down the fluid flow nearest to it. As the flow continues down the pipe, the next layer away from the pipe wall is slowed down slightly less. And so on until the effect of the pipe wall friction no longer affects the velocity. This is called the boundary layer effect and is created whenever flow passes over a surface. Notice the shape of the Figure 3 profile in turbulent flow is different than the shape in Figure 1. Laminar flow has a characteristic “bullet” shaped profile and turbulent has a flatter shape.
Well-developed flow is created when the boundary layer is fully established without disturbances. Put another way, well developed flow will not change its profile as it moves down the pipe. In the industrial flow measurement world, it’s also the definition of good flow and is very important in understanding flow through an orifice.
Power law estimation
When comparing whether a flow profile is well developed or not, a useful tool is the power law estimation. The power law gives a numerical estimation of a well-developed profile. The power law equation is:
u/umax = (1-r/R)1/n
u = velocity at measurement point
umax = max velocity in pipe
r = radius at measurement point
R = pipe radius
n = power
A value of n = 7 is typically used to fit the velocity profile for fully developed, turbulent flows. A higher value of n creates a flatter profile. A lower value creates a more bullet shape profile associated with laminar flow. A power law curve where
n = 7 is shown in Figure 4.
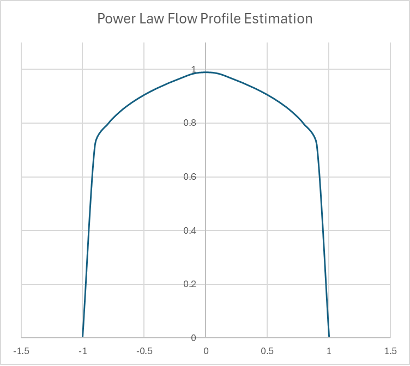
As flow is disturbed with the addition of pipe elements, the flow profile will change. For example, flow through a single elbow creates a skewed profile. The high velocity “core” of the pipe will be pushed to the opposite wall of the pipe, creating an asymmetry where the maximum velocity is no longer in the middle of the pipe. Single elbows and other elements can create asymmetry in the flow profile which is shown well in Figure 5.
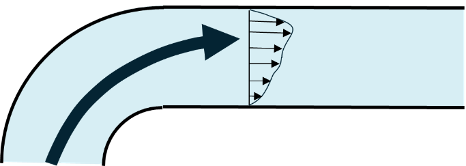
Swirling flow
The flow profile does not capture another type of flow disturbance called swirling flow. Swirling flow is when the flow has a crossflow element. Without swirl the flow will run straight down the pipe, with 0° in relation to the centerline of the pipe. If crossflow is present, the flow streams can have a swirl angle, up to 20° in severe cases.
There are two general types of swirl disturbances, Type 1 and Type 2 swirls. Type 1 swirl moves in one directional rotation across the pipe. This is also known as whole body swirl, Figure 6. Close coupled double elbows out of plane are a common cause of Type 1 swirl, along with headers, pumps and compressors. Type 2 swirl introduces two counter rotating swirls rotating in opposite directions, Figure 7. This is usually created after single elbows.
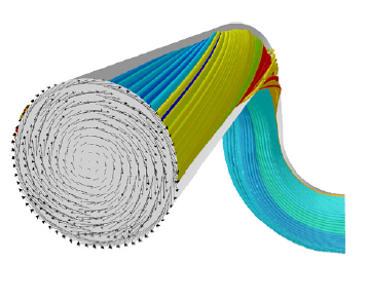
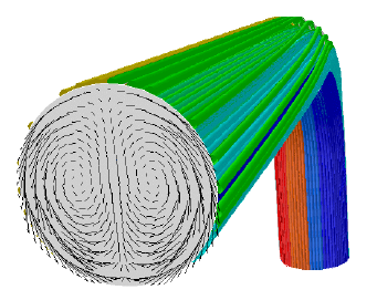
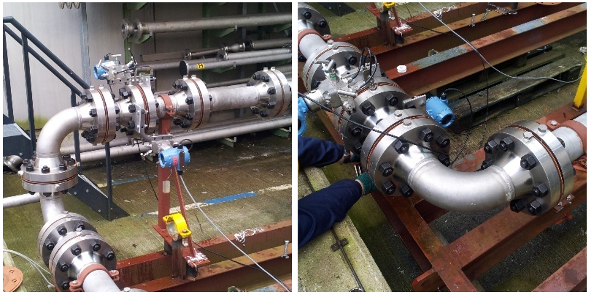
Orifice plate flow measurements
Orifice plates measurement have a century-long track record of continuous use and improvement in industrial applications. No other flow technology has the international volume of understanding and acceptance as orifice plates. Orifice plates are often described as “a hole in a plate” and often ridiculed for that simplicity. Yet it is the simplicity of an orifice plate that makes it so elegant. Leonardo da Vinci once said, “Simplicity is the ultimate sophistication”. The design of the orifice plate makes it possible to manufacture with precision and repeatability. Making one orifice plate measure the same as the next one with matching dimensions. A dimensional inspection is all that is needed to “calibrate” an orifice plate.
Knowing that two identical orifice plates will measure the same (within known uncertainties) is one of the reasons why they are the most widely used industrial flow technology even after 100 years. In today’s world, a user can replace an orifice plate and know the uncertainty of the measurement will not change, even without a flow calibration – something no other flow technology can match!
This also means that a flow calibration once done on a known orifice plate size, can be applied to all other matching orifice plates. Over the decades a massive database of traceable orifice calibrations was completed and used to create the de facto standards for orifice flow measurement. The American standards are the AGA Report No 3 and API 14.3 standards for natural measurement using an orifice plate. The international standard for orifice plates is ISO 5167.
The orifice performance in that technical database (which includes over 30,000 data points!) was tested in well-developed flow conditions. The standards confirm that measurement in matching conditions and dimensions will perform at custody transfer levels of accuracy. And since all the data points were tested in well-developed flow conditions, the standards require the same for accurate measurement.
Effect of flow disturbances on orifice measurement
If a user’s flow conditions are not well developed, with asymmetric or swirling flow, the accuracy will be affected. The effect on accuracy will depend on several factors, including the type of disturbance and the relative distance of the disturbance to the orifice location.
As the distance from the disturbance to the orifice plate increases, the flow will naturally return to a well-developed state due to the turbulence in the flow (turbulence helps us here). The distance needed to return to well-developed flow depends mostly on the type of disturbance. The AGA/API standards recommend up to 44 pipe diameters of straight pipe after double elbow to achieve well developed flow.
Shown below are two sets of flow calibration data from Mattingly and Yeh measuring three different orifice bore sizes (beta ratios) at various distances from a disturbance. Figure 8 shows single elbow effects.Figure 9 shows effects from close coupled, double elbows out of plane.
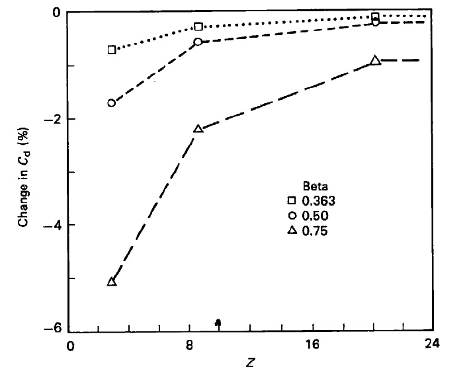
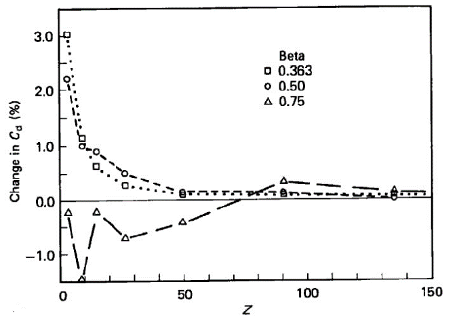
The effect of the disturbance diminishes with distance, approaching zero effect. Notice the effects on accuracy of the orifice plate measurement can be up to 5% after a single elbow using a high beta ratio. The effect lessens using smaller beta ratios. Also notice the x-axis scale of the double elbows chart is much larger than the single elbow chart. This confirms that Type 1 swirl has a much longer lasting impact on flow measurement than Type 2 swirl.
Improving flow conditions
A user can make a determination about their installation knowing the above information. They have three options available to them:
- The user could plan the measurement point as far as possible from the disturbance. The more distance means the more likely the flow is well developed at that point. Some users may have plenty of straight pipe in their system and can meet the minimum requirements in the standards. For most users, creating the necessary straight inlet piping will come with additional expense.
- The user can accept the additional uncertainty that comes with a bad installation. This might be a fine solution in applications with low accuracy requirements. But most industrial applications cannot accept accuracy shifts on the order of ±5%.
- The user could follow the most common practice in the industry: use a flow conditioner.
Flow conditioners
The user of flow conditioners is an industry best practice for ensuring optimal flow measurement with an orifice plate. Flow conditioners come in a variety of designs but have one common goal: to condition the flow to well-developed conditions ahead of an orifice flow measurement point regardless of the disturbance ahead of it.
In the AGA Report No. 3, Section 2.3.1.7 “Flow Conditioners” classifies flow conditioners into two categories: straighteners and isolating flow conditioners.
“Flow straighteners are devices that effectively remove or reduce the swirl component of a flowing stream but may have limited ability to produce the flow conditions necessary to accurately replicate the orifice plate coefficient of discharge database values. Isolating flow conditioners are devices that effectively remove the swirl component from the flowing stream while redistributing the stream to produce the flow conditions that accurately replicate the orifice plate coefficient of discharge database values.”
Flow straighteners
Flow straighteners are low blockage, swirling reducing flow conditioners. Common examples of flow straighteners are tube bundles, example shown in Figure 10 and fin-type straightening vanes, example shown in Figure 11. Tube bundles can be designed with 19 or 7 tubes concentrically grouped in the pipe. The terminology around these can be confusing as tube bundles are sometimes sold as straightening vanes, but both fall into the category of flow straightener as described in AGA 3.
These types of flow conditioners are designed to remove swirl with their elongated dimensions. But since they are low blockages, they do very little to correct he asymmetry in the flow profile. In fact, Mattingly and Yeh also showed that flow straighteners can actually make asymmetry a more persistent flow disturbance, lasting much longer in terms of distance. This is because the flow straighteners will capture the asymmetry entering each tube and reduce the type 2 swirl. By reducing the type 2 swirl, the natural turbulence is diminished and the asymmetry does not break down as quickly.
In short, flow straighteners are not recommended for orifice plate measurement.
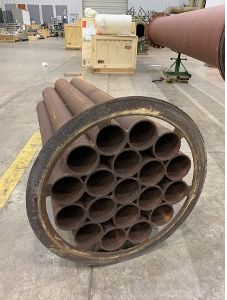

Isolating flow conditioners
Isolating flow conditioners have a blockage factor that forces the flow profile to redistribute as it passes through. This redistribution controls both the asymmetry and swirl disturbances. The design is typically a perforated plate with multiple holes designed to create a well-developed flow profile as soon as possible after the plate.
The search for the ideal pattern of holes to do this job was the subject of much research in the 1990’s as the need for flow conditioning became more and more relevant. A summary of the research from researchers such as Laws, Karnik, Zanker, Gallagher and others is fascinating but outside the scope of this paper. The most widely accepted design of this research was developed by Laws and has become known as the NOVA 50E design.
The NOVA 50E design, Figure 12, is a multi-hole flow conditioner with concentric rings of openings. 16 smaller holes around 8 midsized holes around one large central opening. The size and position of each hole is meant to stimulate the formation of a well-developed flow profile regardless of upstream disturbances. The “50” designation indicates that the plate has approximately a 50% blockage area in the flow path. The success of this design is the balance of three factors: 1) enough blockage to redistribute the flow profile, 2) large enough holes to allow passage of particles and 3) enough opening to reduce the pressure loss across the plate as much as possible. The NOVA design meets the requirements of AGA 3 Section 2.5.5 and APPENDIX 2-D.
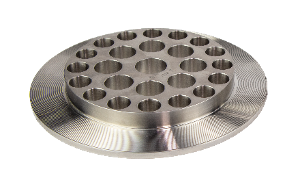
The design is universal for all flow conditions and disturbances. This advantage means a user can have one design flow conditioner for various pipeline installations and conditions. And it gives the user the assurance that most flow disturbances will be removed prior to flow measurement. For as much testing and research has been done of the effects of flow disturbances in a pipe, a user does not know the flow regime and development of their flow profile. Having a flow conditioner improves orifice plate measurement in all standard applications.
Conclusion
The use of a flow conditioner is recommended for all high accuracy orifice plate measurements. The recommended type of flow conditioner is the NOVA 50E design to remove most flow disturbances such as asymmetry and swirl. And users will benefit from the assurance that a well-designed flow conditioner will remove any unknown flow disturbances and problems that could diminish their measurement accuracy.
[1] Effects of pipe elbows and tube bundles onselected types of flowmeters, G.E. Mattingly, T.T. Yeh, Flow Measurement Instrumentation, Vol 2, January 1991
[2] US Patent 5,341,848 “Flow Conditioner”, 1994
Abstract
This paper discusses the effects of poor installations on orifice measurement and the best practices to achieve highest accuracy and performance. Flow disturbances are everywhere in pipelines and industrial applications. Knowing the types of disturbances, their effect on orifice measurement and how to correct those errors is valuable for anyone interested in accurate orifice flow measurement.
What is “Good” Flow
Most flowmeters are affected by the flow that they are trying to measure, orifice plate flowmeters included. Orifice plates measure best in “good” flow conditions and lose accuracy in “bad” conditions. There are several methods to describe and characterize good vs. bad flow conditions. When asked to describe good flow conditions, many users will use the term Laminar. This is a common yet minor misconception in flow engineering.
Laminar vs. Turbulent Flow
Laminar is a flow regime where the flow follows relatively straight lines down a pipe, Figure 1. If you were to follow a particle in the flow, it would go in a straight path and not cross paths with other particles flowing next to it. This is a regime with no turbulence. Laminar flow will happen in low flow and/or high viscous applications. In other words, the momentum forces are low and/or the viscous forces are high. Inherently this makes sense as higher velocities will encourage turbulence and higher viscosities will do the opposite.
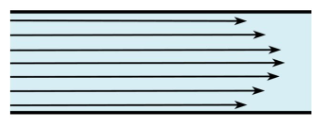
As useful tool is the Reynolds number, which is a dimensionless number used to quantify whether a flow application is in laminar flow. The Reynolds number equations is a follows:
Re=VρD/μ
Re = Reynolds number, dimensionless
V = flow velocity, ft/s
ρ = density, lbm/ft3
μ = dynamic viscosity, lbm/s·ft
The numerator of this equation combines the momentum forces in the flow, velocity, density and size. While the denominator are the inertial forces, viscosity. This follows the logic described earlier. The lower the Reynolds number, the more likely the flow regime is in a laminar state. Laminar flow is more likely to exist where the velocity, density or size is small, and/or where the viscosity is high. The commonly accepted value of laminar flow is Re < 4000. As the Reynolds number increases, the flow regime enters a transition phase between 4000 and 10,000. Above 10,000, the flow regime is considered to be turbulent.
Reynolds number - Flow regime
0 – 4,000 - Laminar
4000 – 10,000 - Transition
>10,000 - Turbulent
Turbulent flow, Figure 2, is the opposite of laminar flow in that the flow streams do not follow a straight or regular pattern. In turbulent flow the flow streams cross, small eddies occur, and mixing is more common. The word “turbulent” rightfully has negative connotations. No one wants to be on an airplane and fly through turbulence.
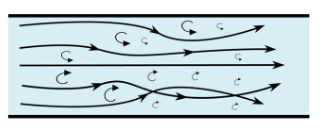
So why is Laminar the incorrect term to describe good flow? It’s not. It’s just not the world in which our flowmeters live. The vast majority of industrial pipelines are in the turbulent flow regime. Virtually all gas flows are turbulent due to the high velocities and low viscosities. Even most liquid flows are turbulent, except for some high viscosity products such as crude oil. Turbulent flow is better for orifice measurement because orifice plates were designed to measure it and their performance is well understood in those conditions.
A side note: Reynolds number is a very helpful in flow measurement. Since it is a dimensionless number, Reynolds can use a single number to describe a flow application. And that number can be used across applications. If the Reynolds number for an application is below 4000, that application is in the laminar flow regime, regardless of the size for example. Reynolds number is used when calibrating a flowmeter. Since the Reynolds number describes the flow in a single number, users can calibrate on one fluid and use the flowmeter in another fluid, knowing the performance will match at equal Reynolds numbers.
Flow profile
A better way to describe understand good vs. bad flow is the presence or absence of flow disturbances. Long, straight, unobstructed pipe will create undisturbed flow. The addition of common pipe elements will create disturbances. Common pipe elements can include single elbows, tees, two elbows in series, partially closed valves, pipe reductions or expansions, thermowells, and many more.
Just like the Reynolds number is a tool to understand the flow regime, the flow profile is a tool to visualize whether flow is disturbed or not. The flow profile attempts to show the velocity at difference points across the diameter of a flowing pipe. This can be physically measured in several ways such as with a single point Pitot tube sensor or with more complex tools such as laser doppler velocimetry. Typically, the view is across a full diameter, crossing through the midpoint of the pipe. A typical flow profile looks like Figure 3 for turbulent flow. Each arrow represents the velocity at points across a diameter of the pipe. The velocities are higher in the center of the pipe and lower near the pipe walls.
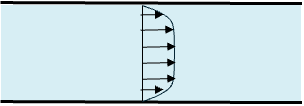
The friction on the pipe walls causes drag which slows down the fluid flow nearest to it. As the flow continues down the pipe, the next layer away from the pipe wall is slowed down slightly less. And so on until the effect of the pipe wall friction no longer affects the velocity. This is called the boundary layer effect and is created whenever flow passes over a surface. Notice the shape of the Figure 3 profile in turbulent flow is different than the shape in Figure 1. Laminar flow has a characteristic “bullet” shaped profile and turbulent has a flatter shape.
Well-developed flow is created when the boundary layer is fully established without disturbances. Put another way, well developed flow will not change its profile as it moves down the pipe. In the industrial flow measurement world, it’s also the definition of good flow and is very important in understanding flow through an orifice.
Power law estimation
When comparing whether a flow profile is well developed or not, a useful tool is the power law estimation. The power law gives a numerical estimation of a well-developed profile. The power law equation is:
u/umax = (1-r/R)1/n
u = velocity at measurement point
umax = max velocity in pipe
r = radius at measurement point
R = pipe radius
n = power
A value of n = 7 is typically used to fit the velocity profile for fully developed, turbulent flows. A higher value of n creates a flatter profile. A lower value creates a more bullet shape profile associated with laminar flow. A power law curve where
n = 7 is shown in Figure 4.
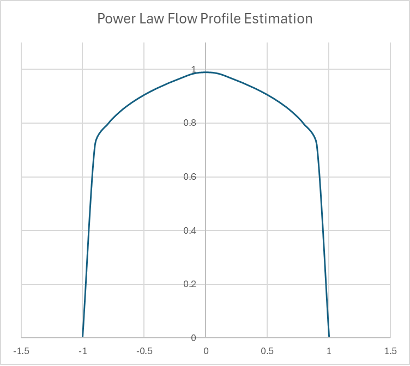
As flow is disturbed with the addition of pipe elements, the flow profile will change. For example, flow through a single elbow creates a skewed profile. The high velocity “core” of the pipe will be pushed to the opposite wall of the pipe, creating an asymmetry where the maximum velocity is no longer in the middle of the pipe. Single elbows and other elements can create asymmetry in the flow profile which is shown well in Figure 5.
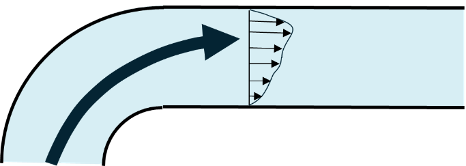
Swirling flow
The flow profile does not capture another type of flow disturbance called swirling flow. Swirling flow is when the flow has a crossflow element. Without swirl the flow will run straight down the pipe, with 0° in relation to the centerline of the pipe. If crossflow is present, the flow streams can have a swirl angle, up to 20° in severe cases.
There are two general types of swirl disturbances, Type 1 and Type 2 swirls. Type 1 swirl moves in one directional rotation across the pipe. This is also known as whole body swirl, Figure 6. Close coupled double elbows out of plane are a common cause of Type 1 swirl, along with headers, pumps and compressors. Type 2 swirl introduces two counter rotating swirls rotating in opposite directions, Figure 7. This is usually created after single elbows.
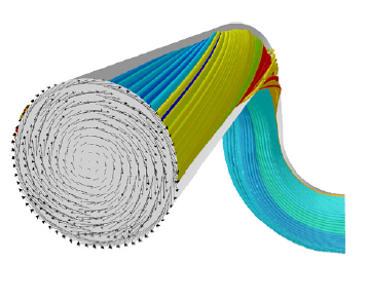
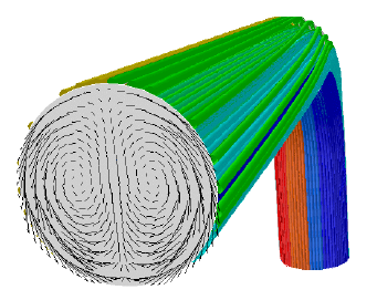
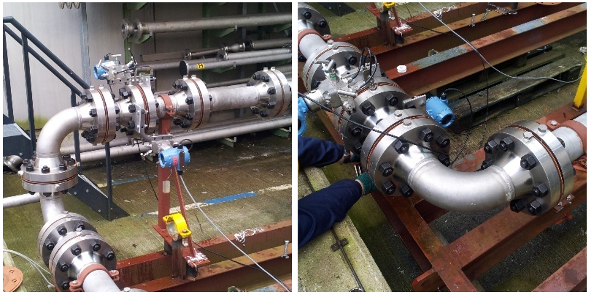
Orifice plate flow measurements
Orifice plates measurement have a century-long track record of continuous use and improvement in industrial applications. No other flow technology has the international volume of understanding and acceptance as orifice plates. Orifice plates are often described as “a hole in a plate” and often ridiculed for that simplicity. Yet it is the simplicity of an orifice plate that makes it so elegant. Leonardo da Vinci once said, “Simplicity is the ultimate sophistication”. The design of the orifice plate makes it possible to manufacture with precision and repeatability. Making one orifice plate measure the same as the next one with matching dimensions. A dimensional inspection is all that is needed to “calibrate” an orifice plate.
Knowing that two identical orifice plates will measure the same (within known uncertainties) is one of the reasons why they are the most widely used industrial flow technology even after 100 years. In today’s world, a user can replace an orifice plate and know the uncertainty of the measurement will not change, even without a flow calibration – something no other flow technology can match!
This also means that a flow calibration once done on a known orifice plate size, can be applied to all other matching orifice plates. Over the decades a massive database of traceable orifice calibrations was completed and used to create the de facto standards for orifice flow measurement. The American standards are the AGA Report No 3 and API 14.3 standards for natural measurement using an orifice plate. The international standard for orifice plates is ISO 5167.
The orifice performance in that technical database (which includes over 30,000 data points!) was tested in well-developed flow conditions. The standards confirm that measurement in matching conditions and dimensions will perform at custody transfer levels of accuracy. And since all the data points were tested in well-developed flow conditions, the standards require the same for accurate measurement.
Effect of flow disturbances on orifice measurement
If a user’s flow conditions are not well developed, with asymmetric or swirling flow, the accuracy will be affected. The effect on accuracy will depend on several factors, including the type of disturbance and the relative distance of the disturbance to the orifice location.
As the distance from the disturbance to the orifice plate increases, the flow will naturally return to a well-developed state due to the turbulence in the flow (turbulence helps us here). The distance needed to return to well-developed flow depends mostly on the type of disturbance. The AGA/API standards recommend up to 44 pipe diameters of straight pipe after double elbow to achieve well developed flow.
Shown below are two sets of flow calibration data from Mattingly and Yeh measuring three different orifice bore sizes (beta ratios) at various distances from a disturbance. Figure 8 shows single elbow effects.Figure 9 shows effects from close coupled, double elbows out of plane.
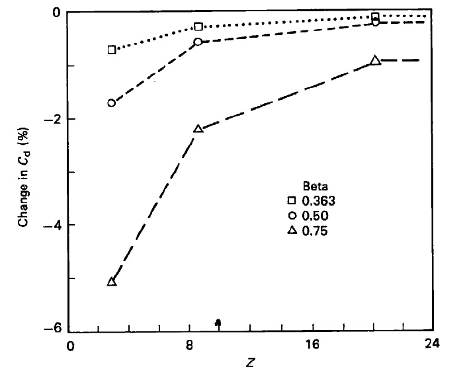
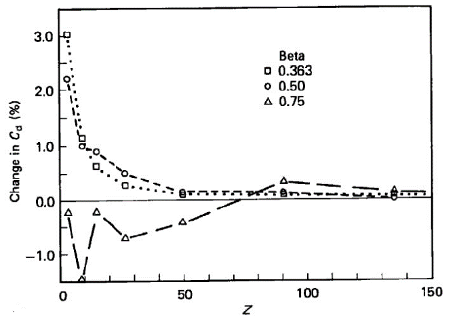
The effect of the disturbance diminishes with distance, approaching zero effect. Notice the effects on accuracy of the orifice plate measurement can be up to 5% after a single elbow using a high beta ratio. The effect lessens using smaller beta ratios. Also notice the x-axis scale of the double elbows chart is much larger than the single elbow chart. This confirms that Type 1 swirl has a much longer lasting impact on flow measurement than Type 2 swirl.
Improving flow conditions
A user can make a determination about their installation knowing the above information. They have three options available to them:
- The user could plan the measurement point as far as possible from the disturbance. The more distance means the more likely the flow is well developed at that point. Some users may have plenty of straight pipe in their system and can meet the minimum requirements in the standards. For most users, creating the necessary straight inlet piping will come with additional expense.
- The user can accept the additional uncertainty that comes with a bad installation. This might be a fine solution in applications with low accuracy requirements. But most industrial applications cannot accept accuracy shifts on the order of ±5%.
- The user could follow the most common practice in the industry: use a flow conditioner.
Flow conditioners
The user of flow conditioners is an industry best practice for ensuring optimal flow measurement with an orifice plate. Flow conditioners come in a variety of designs but have one common goal: to condition the flow to well-developed conditions ahead of an orifice flow measurement point regardless of the disturbance ahead of it.
In the AGA Report No. 3, Section 2.3.1.7 “Flow Conditioners” classifies flow conditioners into two categories: straighteners and isolating flow conditioners.
“Flow straighteners are devices that effectively remove or reduce the swirl component of a flowing stream but may have limited ability to produce the flow conditions necessary to accurately replicate the orifice plate coefficient of discharge database values. Isolating flow conditioners are devices that effectively remove the swirl component from the flowing stream while redistributing the stream to produce the flow conditions that accurately replicate the orifice plate coefficient of discharge database values.”
Flow straighteners
Flow straighteners are low blockage, swirling reducing flow conditioners. Common examples of flow straighteners are tube bundles, example shown in Figure 10 and fin-type straightening vanes, example shown in Figure 11. Tube bundles can be designed with 19 or 7 tubes concentrically grouped in the pipe. The terminology around these can be confusing as tube bundles are sometimes sold as straightening vanes, but both fall into the category of flow straightener as described in AGA 3.
These types of flow conditioners are designed to remove swirl with their elongated dimensions. But since they are low blockages, they do very little to correct he asymmetry in the flow profile. In fact, Mattingly and Yeh also showed that flow straighteners can actually make asymmetry a more persistent flow disturbance, lasting much longer in terms of distance. This is because the flow straighteners will capture the asymmetry entering each tube and reduce the type 2 swirl. By reducing the type 2 swirl, the natural turbulence is diminished and the asymmetry does not break down as quickly.
In short, flow straighteners are not recommended for orifice plate measurement.
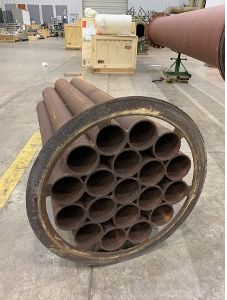

Isolating flow conditioners
Isolating flow conditioners have a blockage factor that forces the flow profile to redistribute as it passes through. This redistribution controls both the asymmetry and swirl disturbances. The design is typically a perforated plate with multiple holes designed to create a well-developed flow profile as soon as possible after the plate.
The search for the ideal pattern of holes to do this job was the subject of much research in the 1990’s as the need for flow conditioning became more and more relevant. A summary of the research from researchers such as Laws, Karnik, Zanker, Gallagher and others is fascinating but outside the scope of this paper. The most widely accepted design of this research was developed by Laws and has become known as the NOVA 50E design.
The NOVA 50E design, Figure 12, is a multi-hole flow conditioner with concentric rings of openings. 16 smaller holes around 8 midsized holes around one large central opening. The size and position of each hole is meant to stimulate the formation of a well-developed flow profile regardless of upstream disturbances. The “50” designation indicates that the plate has approximately a 50% blockage area in the flow path. The success of this design is the balance of three factors: 1) enough blockage to redistribute the flow profile, 2) large enough holes to allow passage of particles and 3) enough opening to reduce the pressure loss across the plate as much as possible. The NOVA design meets the requirements of AGA 3 Section 2.5.5 and APPENDIX 2-D.
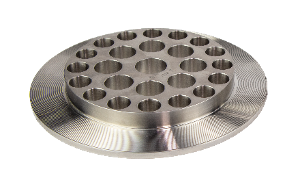
The design is universal for all flow conditions and disturbances. This advantage means a user can have one design flow conditioner for various pipeline installations and conditions. And it gives the user the assurance that most flow disturbances will be removed prior to flow measurement. For as much testing and research has been done of the effects of flow disturbances in a pipe, a user does not know the flow regime and development of their flow profile. Having a flow conditioner improves orifice plate measurement in all standard applications.
Conclusion
The use of a flow conditioner is recommended for all high accuracy orifice plate measurements. The recommended type of flow conditioner is the NOVA 50E design to remove most flow disturbances such as asymmetry and swirl. And users will benefit from the assurance that a well-designed flow conditioner will remove any unknown flow disturbances and problems that could diminish their measurement accuracy.
[1] Effects of pipe elbows and tube bundles onselected types of flowmeters, G.E. Mattingly, T.T. Yeh, Flow Measurement Instrumentation, Vol 2, January 1991
[2] US Patent 5,341,848 “Flow Conditioner”, 1994
Abstract
This paper discusses the effects of poor installations on orifice measurement and the best practices to achieve highest accuracy and performance. Flow disturbances are everywhere in pipelines and industrial applications. Knowing the types of disturbances, their effect on orifice measurement and how to correct those errors is valuable for anyone interested in accurate orifice flow measurement.
What is “Good” Flow
Most flowmeters are affected by the flow that they are trying to measure, orifice plate flowmeters included. Orifice plates measure best in “good” flow conditions and lose accuracy in “bad” conditions. There are several methods to describe and characterize good vs. bad flow conditions. When asked to describe good flow conditions, many users will use the term Laminar. This is a common yet minor misconception in flow engineering.
Laminar vs. Turbulent Flow
Laminar is a flow regime where the flow follows relatively straight lines down a pipe, Figure 1. If you were to follow a particle in the flow, it would go in a straight path and not cross paths with other particles flowing next to it. This is a regime with no turbulence. Laminar flow will happen in low flow and/or high viscous applications. In other words, the momentum forces are low and/or the viscous forces are high. Inherently this makes sense as higher velocities will encourage turbulence and higher viscosities will do the opposite.
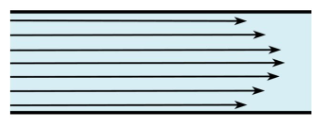
As useful tool is the Reynolds number, which is a dimensionless number used to quantify whether a flow application is in laminar flow. The Reynolds number equations is a follows:
Re=VρD/μ
Re = Reynolds number, dimensionless
V = flow velocity, ft/s
ρ = density, lbm/ft3
μ = dynamic viscosity, lbm/s·ft
The numerator of this equation combines the momentum forces in the flow, velocity, density and size. While the denominator are the inertial forces, viscosity. This follows the logic described earlier. The lower the Reynolds number, the more likely the flow regime is in a laminar state. Laminar flow is more likely to exist where the velocity, density or size is small, and/or where the viscosity is high. The commonly accepted value of laminar flow is Re < 4000. As the Reynolds number increases, the flow regime enters a transition phase between 4000 and 10,000. Above 10,000, the flow regime is considered to be turbulent.
Reynolds number - Flow regime
0 – 4,000 - Laminar
4000 – 10,000 - Transition
>10,000 - Turbulent
Turbulent flow, Figure 2, is the opposite of laminar flow in that the flow streams do not follow a straight or regular pattern. In turbulent flow the flow streams cross, small eddies occur, and mixing is more common. The word “turbulent” rightfully has negative connotations. No one wants to be on an airplane and fly through turbulence.
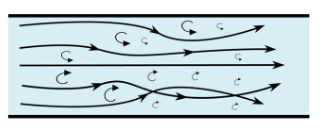
So why is Laminar the incorrect term to describe good flow? It’s not. It’s just not the world in which our flowmeters live. The vast majority of industrial pipelines are in the turbulent flow regime. Virtually all gas flows are turbulent due to the high velocities and low viscosities. Even most liquid flows are turbulent, except for some high viscosity products such as crude oil. Turbulent flow is better for orifice measurement because orifice plates were designed to measure it and their performance is well understood in those conditions.
A side note: Reynolds number is a very helpful in flow measurement. Since it is a dimensionless number, Reynolds can use a single number to describe a flow application. And that number can be used across applications. If the Reynolds number for an application is below 4000, that application is in the laminar flow regime, regardless of the size for example. Reynolds number is used when calibrating a flowmeter. Since the Reynolds number describes the flow in a single number, users can calibrate on one fluid and use the flowmeter in another fluid, knowing the performance will match at equal Reynolds numbers.
Flow profile
A better way to describe understand good vs. bad flow is the presence or absence of flow disturbances. Long, straight, unobstructed pipe will create undisturbed flow. The addition of common pipe elements will create disturbances. Common pipe elements can include single elbows, tees, two elbows in series, partially closed valves, pipe reductions or expansions, thermowells, and many more.
Just like the Reynolds number is a tool to understand the flow regime, the flow profile is a tool to visualize whether flow is disturbed or not. The flow profile attempts to show the velocity at difference points across the diameter of a flowing pipe. This can be physically measured in several ways such as with a single point Pitot tube sensor or with more complex tools such as laser doppler velocimetry. Typically, the view is across a full diameter, crossing through the midpoint of the pipe. A typical flow profile looks like Figure 3 for turbulent flow. Each arrow represents the velocity at points across a diameter of the pipe. The velocities are higher in the center of the pipe and lower near the pipe walls.
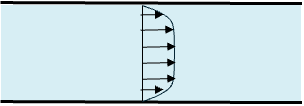
The friction on the pipe walls causes drag which slows down the fluid flow nearest to it. As the flow continues down the pipe, the next layer away from the pipe wall is slowed down slightly less. And so on until the effect of the pipe wall friction no longer affects the velocity. This is called the boundary layer effect and is created whenever flow passes over a surface. Notice the shape of the Figure 3 profile in turbulent flow is different than the shape in Figure 1. Laminar flow has a characteristic “bullet” shaped profile and turbulent has a flatter shape.
Well-developed flow is created when the boundary layer is fully established without disturbances. Put another way, well developed flow will not change its profile as it moves down the pipe. In the industrial flow measurement world, it’s also the definition of good flow and is very important in understanding flow through an orifice.
Power law estimation
When comparing whether a flow profile is well developed or not, a useful tool is the power law estimation. The power law gives a numerical estimation of a well-developed profile. The power law equation is:
u/umax = (1-r/R)1/n
u = velocity at measurement point
umax = max velocity in pipe
r = radius at measurement point
R = pipe radius
n = power
A value of n = 7 is typically used to fit the velocity profile for fully developed, turbulent flows. A higher value of n creates a flatter profile. A lower value creates a more bullet shape profile associated with laminar flow. A power law curve where
n = 7 is shown in Figure 4.
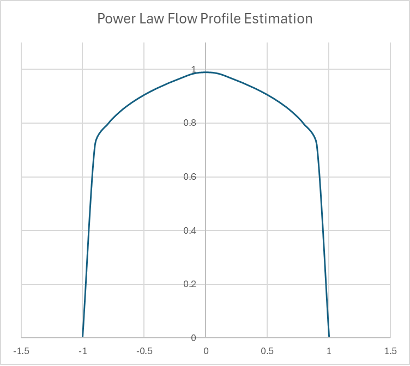
As flow is disturbed with the addition of pipe elements, the flow profile will change. For example, flow through a single elbow creates a skewed profile. The high velocity “core” of the pipe will be pushed to the opposite wall of the pipe, creating an asymmetry where the maximum velocity is no longer in the middle of the pipe. Single elbows and other elements can create asymmetry in the flow profile which is shown well in Figure 5.
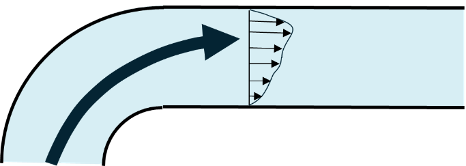
Swirling flow
The flow profile does not capture another type of flow disturbance called swirling flow. Swirling flow is when the flow has a crossflow element. Without swirl the flow will run straight down the pipe, with 0° in relation to the centerline of the pipe. If crossflow is present, the flow streams can have a swirl angle, up to 20° in severe cases.
There are two general types of swirl disturbances, Type 1 and Type 2 swirls. Type 1 swirl moves in one directional rotation across the pipe. This is also known as whole body swirl, Figure 6. Close coupled double elbows out of plane are a common cause of Type 1 swirl, along with headers, pumps and compressors. Type 2 swirl introduces two counter rotating swirls rotating in opposite directions, Figure 7. This is usually created after single elbows.
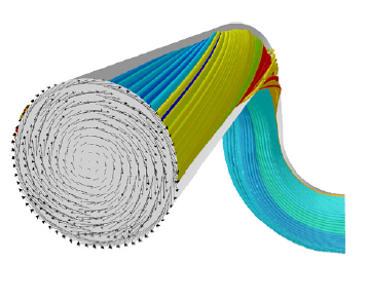
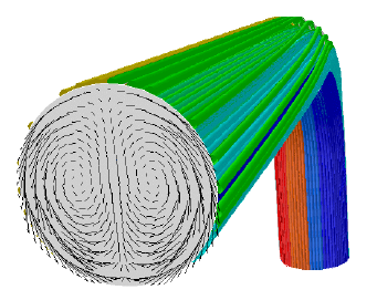
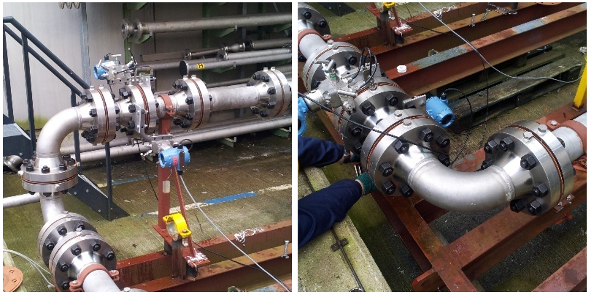
Orifice plate flow measurements
Orifice plates measurement have a century-long track record of continuous use and improvement in industrial applications. No other flow technology has the international volume of understanding and acceptance as orifice plates. Orifice plates are often described as “a hole in a plate” and often ridiculed for that simplicity. Yet it is the simplicity of an orifice plate that makes it so elegant. Leonardo da Vinci once said, “Simplicity is the ultimate sophistication”. The design of the orifice plate makes it possible to manufacture with precision and repeatability. Making one orifice plate measure the same as the next one with matching dimensions. A dimensional inspection is all that is needed to “calibrate” an orifice plate.
Knowing that two identical orifice plates will measure the same (within known uncertainties) is one of the reasons why they are the most widely used industrial flow technology even after 100 years. In today’s world, a user can replace an orifice plate and know the uncertainty of the measurement will not change, even without a flow calibration – something no other flow technology can match!
This also means that a flow calibration once done on a known orifice plate size, can be applied to all other matching orifice plates. Over the decades a massive database of traceable orifice calibrations was completed and used to create the de facto standards for orifice flow measurement. The American standards are the AGA Report No 3 and API 14.3 standards for natural measurement using an orifice plate. The international standard for orifice plates is ISO 5167.
The orifice performance in that technical database (which includes over 30,000 data points!) was tested in well-developed flow conditions. The standards confirm that measurement in matching conditions and dimensions will perform at custody transfer levels of accuracy. And since all the data points were tested in well-developed flow conditions, the standards require the same for accurate measurement.
Effect of flow disturbances on orifice measurement
If a user’s flow conditions are not well developed, with asymmetric or swirling flow, the accuracy will be affected. The effect on accuracy will depend on several factors, including the type of disturbance and the relative distance of the disturbance to the orifice location.
As the distance from the disturbance to the orifice plate increases, the flow will naturally return to a well-developed state due to the turbulence in the flow (turbulence helps us here). The distance needed to return to well-developed flow depends mostly on the type of disturbance. The AGA/API standards recommend up to 44 pipe diameters of straight pipe after double elbow to achieve well developed flow.
Shown below are two sets of flow calibration data from Mattingly and Yeh measuring three different orifice bore sizes (beta ratios) at various distances from a disturbance. Figure 8 shows single elbow effects.Figure 9 shows effects from close coupled, double elbows out of plane.
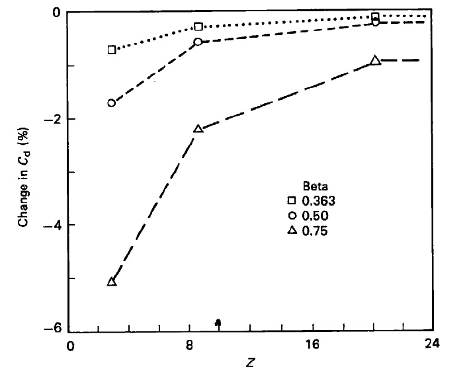
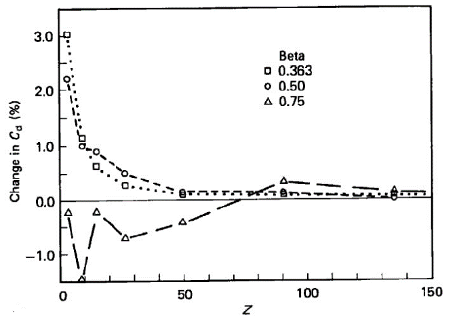
The effect of the disturbance diminishes with distance, approaching zero effect. Notice the effects on accuracy of the orifice plate measurement can be up to 5% after a single elbow using a high beta ratio. The effect lessens using smaller beta ratios. Also notice the x-axis scale of the double elbows chart is much larger than the single elbow chart. This confirms that Type 1 swirl has a much longer lasting impact on flow measurement than Type 2 swirl.
Improving flow conditions
A user can make a determination about their installation knowing the above information. They have three options available to them:
- The user could plan the measurement point as far as possible from the disturbance. The more distance means the more likely the flow is well developed at that point. Some users may have plenty of straight pipe in their system and can meet the minimum requirements in the standards. For most users, creating the necessary straight inlet piping will come with additional expense.
- The user can accept the additional uncertainty that comes with a bad installation. This might be a fine solution in applications with low accuracy requirements. But most industrial applications cannot accept accuracy shifts on the order of ±5%.
- The user could follow the most common practice in the industry: use a flow conditioner.
Flow conditioners
The user of flow conditioners is an industry best practice for ensuring optimal flow measurement with an orifice plate. Flow conditioners come in a variety of designs but have one common goal: to condition the flow to well-developed conditions ahead of an orifice flow measurement point regardless of the disturbance ahead of it.
In the AGA Report No. 3, Section 2.3.1.7 “Flow Conditioners” classifies flow conditioners into two categories: straighteners and isolating flow conditioners.
“Flow straighteners are devices that effectively remove or reduce the swirl component of a flowing stream but may have limited ability to produce the flow conditions necessary to accurately replicate the orifice plate coefficient of discharge database values. Isolating flow conditioners are devices that effectively remove the swirl component from the flowing stream while redistributing the stream to produce the flow conditions that accurately replicate the orifice plate coefficient of discharge database values.”
Flow straighteners
Flow straighteners are low blockage, swirling reducing flow conditioners. Common examples of flow straighteners are tube bundles, example shown in Figure 10 and fin-type straightening vanes, example shown in Figure 11. Tube bundles can be designed with 19 or 7 tubes concentrically grouped in the pipe. The terminology around these can be confusing as tube bundles are sometimes sold as straightening vanes, but both fall into the category of flow straightener as described in AGA 3.
These types of flow conditioners are designed to remove swirl with their elongated dimensions. But since they are low blockages, they do very little to correct he asymmetry in the flow profile. In fact, Mattingly and Yeh also showed that flow straighteners can actually make asymmetry a more persistent flow disturbance, lasting much longer in terms of distance. This is because the flow straighteners will capture the asymmetry entering each tube and reduce the type 2 swirl. By reducing the type 2 swirl, the natural turbulence is diminished and the asymmetry does not break down as quickly.
In short, flow straighteners are not recommended for orifice plate measurement.
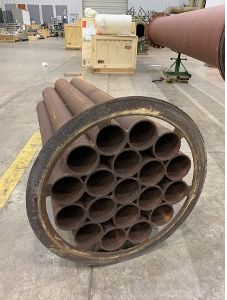

Isolating flow conditioners
Isolating flow conditioners have a blockage factor that forces the flow profile to redistribute as it passes through. This redistribution controls both the asymmetry and swirl disturbances. The design is typically a perforated plate with multiple holes designed to create a well-developed flow profile as soon as possible after the plate.
The search for the ideal pattern of holes to do this job was the subject of much research in the 1990’s as the need for flow conditioning became more and more relevant. A summary of the research from researchers such as Laws, Karnik, Zanker, Gallagher and others is fascinating but outside the scope of this paper. The most widely accepted design of this research was developed by Laws and has become known as the NOVA 50E design.
The NOVA 50E design, Figure 12, is a multi-hole flow conditioner with concentric rings of openings. 16 smaller holes around 8 midsized holes around one large central opening. The size and position of each hole is meant to stimulate the formation of a well-developed flow profile regardless of upstream disturbances. The “50” designation indicates that the plate has approximately a 50% blockage area in the flow path. The success of this design is the balance of three factors: 1) enough blockage to redistribute the flow profile, 2) large enough holes to allow passage of particles and 3) enough opening to reduce the pressure loss across the plate as much as possible. The NOVA design meets the requirements of AGA 3 Section 2.5.5 and APPENDIX 2-D.
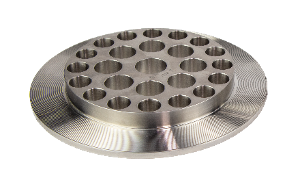
The design is universal for all flow conditions and disturbances. This advantage means a user can have one design flow conditioner for various pipeline installations and conditions. And it gives the user the assurance that most flow disturbances will be removed prior to flow measurement. For as much testing and research has been done of the effects of flow disturbances in a pipe, a user does not know the flow regime and development of their flow profile. Having a flow conditioner improves orifice plate measurement in all standard applications.
Conclusion
The use of a flow conditioner is recommended for all high accuracy orifice plate measurements. The recommended type of flow conditioner is the NOVA 50E design to remove most flow disturbances such as asymmetry and swirl. And users will benefit from the assurance that a well-designed flow conditioner will remove any unknown flow disturbances and problems that could diminish their measurement accuracy.
[1] Effects of pipe elbows and tube bundles onselected types of flowmeters, G.E. Mattingly, T.T. Yeh, Flow Measurement Instrumentation, Vol 2, January 1991
[2] US Patent 5,341,848 “Flow Conditioner”, 1994
Abstract
This paper discusses the effects of poor installations on orifice measurement and the best practices to achieve highest accuracy and performance. Flow disturbances are everywhere in pipelines and industrial applications. Knowing the types of disturbances, their effect on orifice measurement and how to correct those errors is valuable for anyone interested in accurate orifice flow measurement.
What is “Good” Flow
Most flowmeters are affected by the flow that they are trying to measure, orifice plate flowmeters included. Orifice plates measure best in “good” flow conditions and lose accuracy in “bad” conditions. There are several methods to describe and characterize good vs. bad flow conditions. When asked to describe good flow conditions, many users will use the term Laminar. This is a common yet minor misconception in flow engineering.
Laminar vs. Turbulent Flow
Laminar is a flow regime where the flow follows relatively straight lines down a pipe, Figure 1. If you were to follow a particle in the flow, it would go in a straight path and not cross paths with other particles flowing next to it. This is a regime with no turbulence. Laminar flow will happen in low flow and/or high viscous applications. In other words, the momentum forces are low and/or the viscous forces are high. Inherently this makes sense as higher velocities will encourage turbulence and higher viscosities will do the opposite.
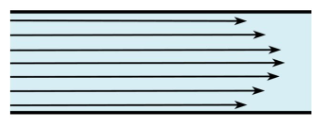
As useful tool is the Reynolds number, which is a dimensionless number used to quantify whether a flow application is in laminar flow. The Reynolds number equations is a follows:
Re=VρD/μ
Re = Reynolds number, dimensionless
V = flow velocity, ft/s
ρ = density, lbm/ft3
μ = dynamic viscosity, lbm/s·ft
The numerator of this equation combines the momentum forces in the flow, velocity, density and size. While the denominator are the inertial forces, viscosity. This follows the logic described earlier. The lower the Reynolds number, the more likely the flow regime is in a laminar state. Laminar flow is more likely to exist where the velocity, density or size is small, and/or where the viscosity is high. The commonly accepted value of laminar flow is Re < 4000. As the Reynolds number increases, the flow regime enters a transition phase between 4000 and 10,000. Above 10,000, the flow regime is considered to be turbulent.
Reynolds number - Flow regime
0 – 4,000 - Laminar
4000 – 10,000 - Transition
>10,000 - Turbulent
Turbulent flow, Figure 2, is the opposite of laminar flow in that the flow streams do not follow a straight or regular pattern. In turbulent flow the flow streams cross, small eddies occur, and mixing is more common. The word “turbulent” rightfully has negative connotations. No one wants to be on an airplane and fly through turbulence.
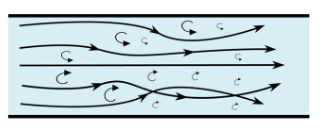
So why is Laminar the incorrect term to describe good flow? It’s not. It’s just not the world in which our flowmeters live. The vast majority of industrial pipelines are in the turbulent flow regime. Virtually all gas flows are turbulent due to the high velocities and low viscosities. Even most liquid flows are turbulent, except for some high viscosity products such as crude oil. Turbulent flow is better for orifice measurement because orifice plates were designed to measure it and their performance is well understood in those conditions.
A side note: Reynolds number is a very helpful in flow measurement. Since it is a dimensionless number, Reynolds can use a single number to describe a flow application. And that number can be used across applications. If the Reynolds number for an application is below 4000, that application is in the laminar flow regime, regardless of the size for example. Reynolds number is used when calibrating a flowmeter. Since the Reynolds number describes the flow in a single number, users can calibrate on one fluid and use the flowmeter in another fluid, knowing the performance will match at equal Reynolds numbers.
Flow profile
A better way to describe understand good vs. bad flow is the presence or absence of flow disturbances. Long, straight, unobstructed pipe will create undisturbed flow. The addition of common pipe elements will create disturbances. Common pipe elements can include single elbows, tees, two elbows in series, partially closed valves, pipe reductions or expansions, thermowells, and many more.
Just like the Reynolds number is a tool to understand the flow regime, the flow profile is a tool to visualize whether flow is disturbed or not. The flow profile attempts to show the velocity at difference points across the diameter of a flowing pipe. This can be physically measured in several ways such as with a single point Pitot tube sensor or with more complex tools such as laser doppler velocimetry. Typically, the view is across a full diameter, crossing through the midpoint of the pipe. A typical flow profile looks like Figure 3 for turbulent flow. Each arrow represents the velocity at points across a diameter of the pipe. The velocities are higher in the center of the pipe and lower near the pipe walls.
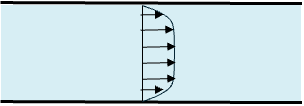
The friction on the pipe walls causes drag which slows down the fluid flow nearest to it. As the flow continues down the pipe, the next layer away from the pipe wall is slowed down slightly less. And so on until the effect of the pipe wall friction no longer affects the velocity. This is called the boundary layer effect and is created whenever flow passes over a surface. Notice the shape of the Figure 3 profile in turbulent flow is different than the shape in Figure 1. Laminar flow has a characteristic “bullet” shaped profile and turbulent has a flatter shape.
Well-developed flow is created when the boundary layer is fully established without disturbances. Put another way, well developed flow will not change its profile as it moves down the pipe. In the industrial flow measurement world, it’s also the definition of good flow and is very important in understanding flow through an orifice.
Power law estimation
When comparing whether a flow profile is well developed or not, a useful tool is the power law estimation. The power law gives a numerical estimation of a well-developed profile. The power law equation is:
u/umax = (1-r/R)1/n
u = velocity at measurement point
umax = max velocity in pipe
r = radius at measurement point
R = pipe radius
n = power
A value of n = 7 is typically used to fit the velocity profile for fully developed, turbulent flows. A higher value of n creates a flatter profile. A lower value creates a more bullet shape profile associated with laminar flow. A power law curve where
n = 7 is shown in Figure 4.
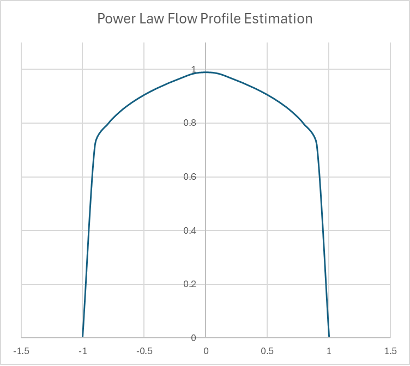
As flow is disturbed with the addition of pipe elements, the flow profile will change. For example, flow through a single elbow creates a skewed profile. The high velocity “core” of the pipe will be pushed to the opposite wall of the pipe, creating an asymmetry where the maximum velocity is no longer in the middle of the pipe. Single elbows and other elements can create asymmetry in the flow profile which is shown well in Figure 5.
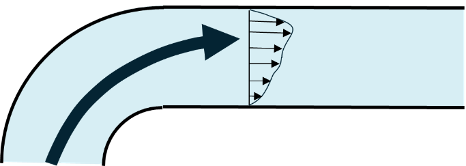
Swirling flow
The flow profile does not capture another type of flow disturbance called swirling flow. Swirling flow is when the flow has a crossflow element. Without swirl the flow will run straight down the pipe, with 0° in relation to the centerline of the pipe. If crossflow is present, the flow streams can have a swirl angle, up to 20° in severe cases.
There are two general types of swirl disturbances, Type 1 and Type 2 swirls. Type 1 swirl moves in one directional rotation across the pipe. This is also known as whole body swirl, Figure 6. Close coupled double elbows out of plane are a common cause of Type 1 swirl, along with headers, pumps and compressors. Type 2 swirl introduces two counter rotating swirls rotating in opposite directions, Figure 7. This is usually created after single elbows.
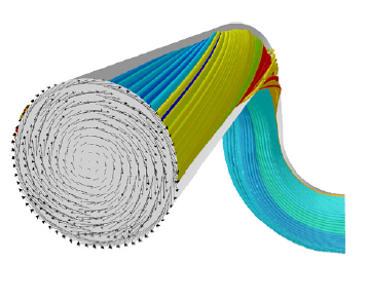
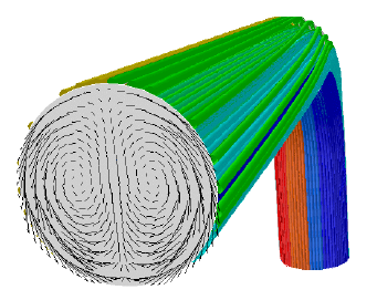
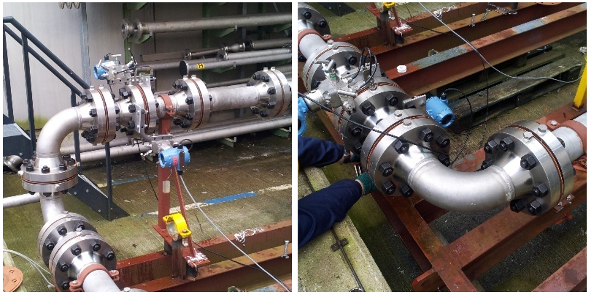
Orifice plate flow measurements
Orifice plates measurement have a century-long track record of continuous use and improvement in industrial applications. No other flow technology has the international volume of understanding and acceptance as orifice plates. Orifice plates are often described as “a hole in a plate” and often ridiculed for that simplicity. Yet it is the simplicity of an orifice plate that makes it so elegant. Leonardo da Vinci once said, “Simplicity is the ultimate sophistication”. The design of the orifice plate makes it possible to manufacture with precision and repeatability. Making one orifice plate measure the same as the next one with matching dimensions. A dimensional inspection is all that is needed to “calibrate” an orifice plate.
Knowing that two identical orifice plates will measure the same (within known uncertainties) is one of the reasons why they are the most widely used industrial flow technology even after 100 years. In today’s world, a user can replace an orifice plate and know the uncertainty of the measurement will not change, even without a flow calibration – something no other flow technology can match!
This also means that a flow calibration once done on a known orifice plate size, can be applied to all other matching orifice plates. Over the decades a massive database of traceable orifice calibrations was completed and used to create the de facto standards for orifice flow measurement. The American standards are the AGA Report No 3 and API 14.3 standards for natural measurement using an orifice plate. The international standard for orifice plates is ISO 5167.
The orifice performance in that technical database (which includes over 30,000 data points!) was tested in well-developed flow conditions. The standards confirm that measurement in matching conditions and dimensions will perform at custody transfer levels of accuracy. And since all the data points were tested in well-developed flow conditions, the standards require the same for accurate measurement.
Effect of flow disturbances on orifice measurement
If a user’s flow conditions are not well developed, with asymmetric or swirling flow, the accuracy will be affected. The effect on accuracy will depend on several factors, including the type of disturbance and the relative distance of the disturbance to the orifice location.
As the distance from the disturbance to the orifice plate increases, the flow will naturally return to a well-developed state due to the turbulence in the flow (turbulence helps us here). The distance needed to return to well-developed flow depends mostly on the type of disturbance. The AGA/API standards recommend up to 44 pipe diameters of straight pipe after double elbow to achieve well developed flow.
Shown below are two sets of flow calibration data from Mattingly and Yeh measuring three different orifice bore sizes (beta ratios) at various distances from a disturbance. Figure 8 shows single elbow effects.Figure 9 shows effects from close coupled, double elbows out of plane.
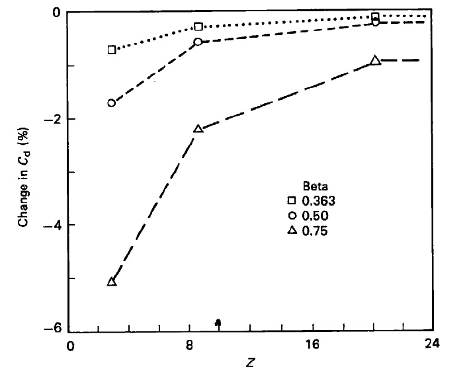
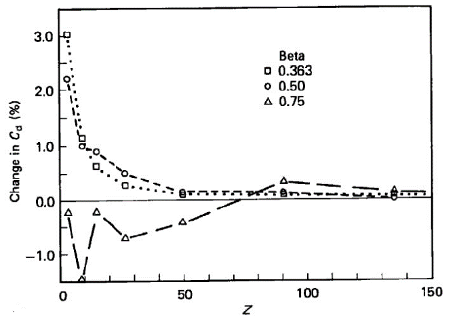
The effect of the disturbance diminishes with distance, approaching zero effect. Notice the effects on accuracy of the orifice plate measurement can be up to 5% after a single elbow using a high beta ratio. The effect lessens using smaller beta ratios. Also notice the x-axis scale of the double elbows chart is much larger than the single elbow chart. This confirms that Type 1 swirl has a much longer lasting impact on flow measurement than Type 2 swirl.
Improving flow conditions
A user can make a determination about their installation knowing the above information. They have three options available to them:
- The user could plan the measurement point as far as possible from the disturbance. The more distance means the more likely the flow is well developed at that point. Some users may have plenty of straight pipe in their system and can meet the minimum requirements in the standards. For most users, creating the necessary straight inlet piping will come with additional expense.
- The user can accept the additional uncertainty that comes with a bad installation. This might be a fine solution in applications with low accuracy requirements. But most industrial applications cannot accept accuracy shifts on the order of ±5%.
- The user could follow the most common practice in the industry: use a flow conditioner.
Flow conditioners
The user of flow conditioners is an industry best practice for ensuring optimal flow measurement with an orifice plate. Flow conditioners come in a variety of designs but have one common goal: to condition the flow to well-developed conditions ahead of an orifice flow measurement point regardless of the disturbance ahead of it.
In the AGA Report No. 3, Section 2.3.1.7 “Flow Conditioners” classifies flow conditioners into two categories: straighteners and isolating flow conditioners.
“Flow straighteners are devices that effectively remove or reduce the swirl component of a flowing stream but may have limited ability to produce the flow conditions necessary to accurately replicate the orifice plate coefficient of discharge database values. Isolating flow conditioners are devices that effectively remove the swirl component from the flowing stream while redistributing the stream to produce the flow conditions that accurately replicate the orifice plate coefficient of discharge database values.”
Flow straighteners
Flow straighteners are low blockage, swirling reducing flow conditioners. Common examples of flow straighteners are tube bundles, example shown in Figure 10 and fin-type straightening vanes, example shown in Figure 11. Tube bundles can be designed with 19 or 7 tubes concentrically grouped in the pipe. The terminology around these can be confusing as tube bundles are sometimes sold as straightening vanes, but both fall into the category of flow straightener as described in AGA 3.
These types of flow conditioners are designed to remove swirl with their elongated dimensions. But since they are low blockages, they do very little to correct he asymmetry in the flow profile. In fact, Mattingly and Yeh also showed that flow straighteners can actually make asymmetry a more persistent flow disturbance, lasting much longer in terms of distance. This is because the flow straighteners will capture the asymmetry entering each tube and reduce the type 2 swirl. By reducing the type 2 swirl, the natural turbulence is diminished and the asymmetry does not break down as quickly.
In short, flow straighteners are not recommended for orifice plate measurement.
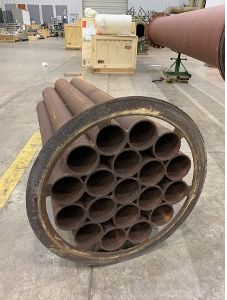

Isolating flow conditioners
Isolating flow conditioners have a blockage factor that forces the flow profile to redistribute as it passes through. This redistribution controls both the asymmetry and swirl disturbances. The design is typically a perforated plate with multiple holes designed to create a well-developed flow profile as soon as possible after the plate.
The search for the ideal pattern of holes to do this job was the subject of much research in the 1990’s as the need for flow conditioning became more and more relevant. A summary of the research from researchers such as Laws, Karnik, Zanker, Gallagher and others is fascinating but outside the scope of this paper. The most widely accepted design of this research was developed by Laws and has become known as the NOVA 50E design.
The NOVA 50E design, Figure 12, is a multi-hole flow conditioner with concentric rings of openings. 16 smaller holes around 8 midsized holes around one large central opening. The size and position of each hole is meant to stimulate the formation of a well-developed flow profile regardless of upstream disturbances. The “50” designation indicates that the plate has approximately a 50% blockage area in the flow path. The success of this design is the balance of three factors: 1) enough blockage to redistribute the flow profile, 2) large enough holes to allow passage of particles and 3) enough opening to reduce the pressure loss across the plate as much as possible. The NOVA design meets the requirements of AGA 3 Section 2.5.5 and APPENDIX 2-D.
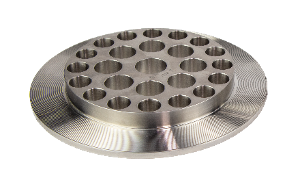
The design is universal for all flow conditions and disturbances. This advantage means a user can have one design flow conditioner for various pipeline installations and conditions. And it gives the user the assurance that most flow disturbances will be removed prior to flow measurement. For as much testing and research has been done of the effects of flow disturbances in a pipe, a user does not know the flow regime and development of their flow profile. Having a flow conditioner improves orifice plate measurement in all standard applications.
Conclusion
The use of a flow conditioner is recommended for all high accuracy orifice plate measurements. The recommended type of flow conditioner is the NOVA 50E design to remove most flow disturbances such as asymmetry and swirl. And users will benefit from the assurance that a well-designed flow conditioner will remove any unknown flow disturbances and problems that could diminish their measurement accuracy.
[1] Effects of pipe elbows and tube bundles onselected types of flowmeters, G.E. Mattingly, T.T. Yeh, Flow Measurement Instrumentation, Vol 2, January 1991
[2] US Patent 5,341,848 “Flow Conditioner”, 1994
Abstract
This paper discusses the effects of poor installations on orifice measurement and the best practices to achieve highest accuracy and performance. Flow disturbances are everywhere in pipelines and industrial applications. Knowing the types of disturbances, their effect on orifice measurement and how to correct those errors is valuable for anyone interested in accurate orifice flow measurement.
What is “Good” Flow
Most flowmeters are affected by the flow that they are trying to measure, orifice plate flowmeters included. Orifice plates measure best in “good” flow conditions and lose accuracy in “bad” conditions. There are several methods to describe and characterize good vs. bad flow conditions. When asked to describe good flow conditions, many users will use the term Laminar. This is a common yet minor misconception in flow engineering.
Laminar vs. Turbulent Flow
Laminar is a flow regime where the flow follows relatively straight lines down a pipe, Figure 1. If you were to follow a particle in the flow, it would go in a straight path and not cross paths with other particles flowing next to it. This is a regime with no turbulence. Laminar flow will happen in low flow and/or high viscous applications. In other words, the momentum forces are low and/or the viscous forces are high. Inherently this makes sense as higher velocities will encourage turbulence and higher viscosities will do the opposite.
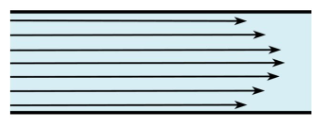
As useful tool is the Reynolds number, which is a dimensionless number used to quantify whether a flow application is in laminar flow. The Reynolds number equations is a follows:
Re=VρD/μ
Re = Reynolds number, dimensionless
V = flow velocity, ft/s
ρ = density, lbm/ft3
μ = dynamic viscosity, lbm/s·ft
The numerator of this equation combines the momentum forces in the flow, velocity, density and size. While the denominator are the inertial forces, viscosity. This follows the logic described earlier. The lower the Reynolds number, the more likely the flow regime is in a laminar state. Laminar flow is more likely to exist where the velocity, density or size is small, and/or where the viscosity is high. The commonly accepted value of laminar flow is Re < 4000. As the Reynolds number increases, the flow regime enters a transition phase between 4000 and 10,000. Above 10,000, the flow regime is considered to be turbulent.
Reynolds number - Flow regime
0 – 4,000 - Laminar
4000 – 10,000 - Transition
>10,000 - Turbulent
Turbulent flow, Figure 2, is the opposite of laminar flow in that the flow streams do not follow a straight or regular pattern. In turbulent flow the flow streams cross, small eddies occur, and mixing is more common. The word “turbulent” rightfully has negative connotations. No one wants to be on an airplane and fly through turbulence.
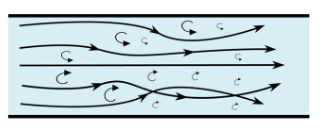
So why is Laminar the incorrect term to describe good flow? It’s not. It’s just not the world in which our flowmeters live. The vast majority of industrial pipelines are in the turbulent flow regime. Virtually all gas flows are turbulent due to the high velocities and low viscosities. Even most liquid flows are turbulent, except for some high viscosity products such as crude oil. Turbulent flow is better for orifice measurement because orifice plates were designed to measure it and their performance is well understood in those conditions.
A side note: Reynolds number is a very helpful in flow measurement. Since it is a dimensionless number, Reynolds can use a single number to describe a flow application. And that number can be used across applications. If the Reynolds number for an application is below 4000, that application is in the laminar flow regime, regardless of the size for example. Reynolds number is used when calibrating a flowmeter. Since the Reynolds number describes the flow in a single number, users can calibrate on one fluid and use the flowmeter in another fluid, knowing the performance will match at equal Reynolds numbers.
Flow profile
A better way to describe understand good vs. bad flow is the presence or absence of flow disturbances. Long, straight, unobstructed pipe will create undisturbed flow. The addition of common pipe elements will create disturbances. Common pipe elements can include single elbows, tees, two elbows in series, partially closed valves, pipe reductions or expansions, thermowells, and many more.
Just like the Reynolds number is a tool to understand the flow regime, the flow profile is a tool to visualize whether flow is disturbed or not. The flow profile attempts to show the velocity at difference points across the diameter of a flowing pipe. This can be physically measured in several ways such as with a single point Pitot tube sensor or with more complex tools such as laser doppler velocimetry. Typically, the view is across a full diameter, crossing through the midpoint of the pipe. A typical flow profile looks like Figure 3 for turbulent flow. Each arrow represents the velocity at points across a diameter of the pipe. The velocities are higher in the center of the pipe and lower near the pipe walls.
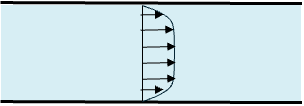
The friction on the pipe walls causes drag which slows down the fluid flow nearest to it. As the flow continues down the pipe, the next layer away from the pipe wall is slowed down slightly less. And so on until the effect of the pipe wall friction no longer affects the velocity. This is called the boundary layer effect and is created whenever flow passes over a surface. Notice the shape of the Figure 3 profile in turbulent flow is different than the shape in Figure 1. Laminar flow has a characteristic “bullet” shaped profile and turbulent has a flatter shape.
Well-developed flow is created when the boundary layer is fully established without disturbances. Put another way, well developed flow will not change its profile as it moves down the pipe. In the industrial flow measurement world, it’s also the definition of good flow and is very important in understanding flow through an orifice.
Power law estimation
When comparing whether a flow profile is well developed or not, a useful tool is the power law estimation. The power law gives a numerical estimation of a well-developed profile. The power law equation is:
u/umax = (1-r/R)1/n
u = velocity at measurement point
umax = max velocity in pipe
r = radius at measurement point
R = pipe radius
n = power
A value of n = 7 is typically used to fit the velocity profile for fully developed, turbulent flows. A higher value of n creates a flatter profile. A lower value creates a more bullet shape profile associated with laminar flow. A power law curve where
n = 7 is shown in Figure 4.
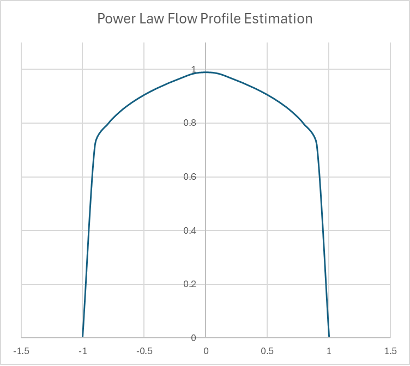
As flow is disturbed with the addition of pipe elements, the flow profile will change. For example, flow through a single elbow creates a skewed profile. The high velocity “core” of the pipe will be pushed to the opposite wall of the pipe, creating an asymmetry where the maximum velocity is no longer in the middle of the pipe. Single elbows and other elements can create asymmetry in the flow profile which is shown well in Figure 5.
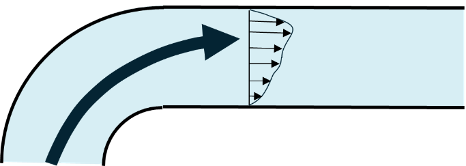
Swirling flow
The flow profile does not capture another type of flow disturbance called swirling flow. Swirling flow is when the flow has a crossflow element. Without swirl the flow will run straight down the pipe, with 0° in relation to the centerline of the pipe. If crossflow is present, the flow streams can have a swirl angle, up to 20° in severe cases.
There are two general types of swirl disturbances, Type 1 and Type 2 swirls. Type 1 swirl moves in one directional rotation across the pipe. This is also known as whole body swirl, Figure 6. Close coupled double elbows out of plane are a common cause of Type 1 swirl, along with headers, pumps and compressors. Type 2 swirl introduces two counter rotating swirls rotating in opposite directions, Figure 7. This is usually created after single elbows.
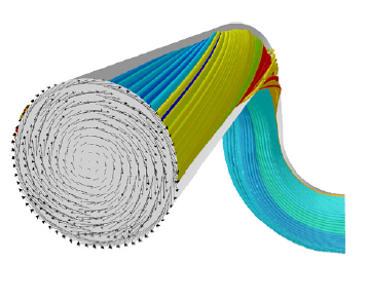
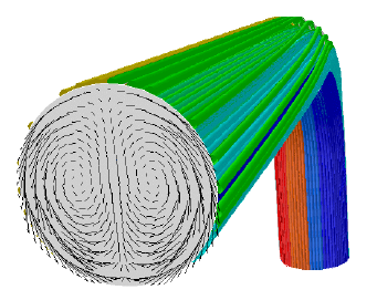
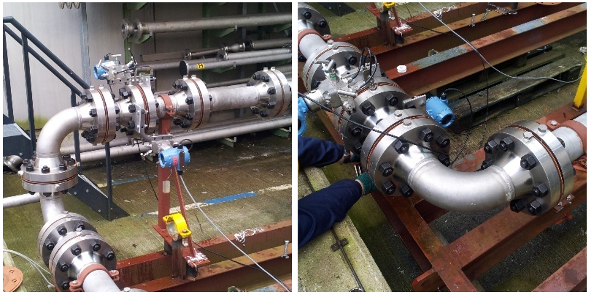
Orifice plate flow measurements
Orifice plates measurement have a century-long track record of continuous use and improvement in industrial applications. No other flow technology has the international volume of understanding and acceptance as orifice plates. Orifice plates are often described as “a hole in a plate” and often ridiculed for that simplicity. Yet it is the simplicity of an orifice plate that makes it so elegant. Leonardo da Vinci once said, “Simplicity is the ultimate sophistication”. The design of the orifice plate makes it possible to manufacture with precision and repeatability. Making one orifice plate measure the same as the next one with matching dimensions. A dimensional inspection is all that is needed to “calibrate” an orifice plate.
Knowing that two identical orifice plates will measure the same (within known uncertainties) is one of the reasons why they are the most widely used industrial flow technology even after 100 years. In today’s world, a user can replace an orifice plate and know the uncertainty of the measurement will not change, even without a flow calibration – something no other flow technology can match!
This also means that a flow calibration once done on a known orifice plate size, can be applied to all other matching orifice plates. Over the decades a massive database of traceable orifice calibrations was completed and used to create the de facto standards for orifice flow measurement. The American standards are the AGA Report No 3 and API 14.3 standards for natural measurement using an orifice plate. The international standard for orifice plates is ISO 5167.
The orifice performance in that technical database (which includes over 30,000 data points!) was tested in well-developed flow conditions. The standards confirm that measurement in matching conditions and dimensions will perform at custody transfer levels of accuracy. And since all the data points were tested in well-developed flow conditions, the standards require the same for accurate measurement.
Effect of flow disturbances on orifice measurement
If a user’s flow conditions are not well developed, with asymmetric or swirling flow, the accuracy will be affected. The effect on accuracy will depend on several factors, including the type of disturbance and the relative distance of the disturbance to the orifice location.
As the distance from the disturbance to the orifice plate increases, the flow will naturally return to a well-developed state due to the turbulence in the flow (turbulence helps us here). The distance needed to return to well-developed flow depends mostly on the type of disturbance. The AGA/API standards recommend up to 44 pipe diameters of straight pipe after double elbow to achieve well developed flow.
Shown below are two sets of flow calibration data from Mattingly and Yeh measuring three different orifice bore sizes (beta ratios) at various distances from a disturbance. Figure 8 shows single elbow effects.Figure 9 shows effects from close coupled, double elbows out of plane.
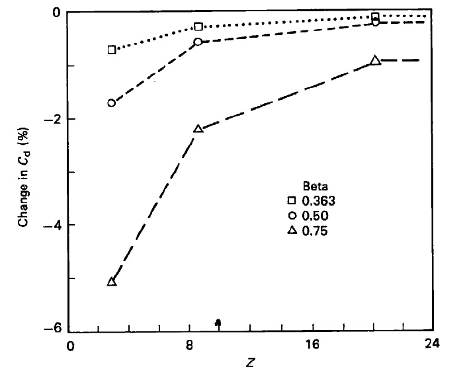
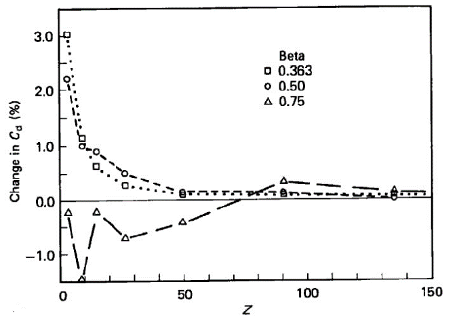
The effect of the disturbance diminishes with distance, approaching zero effect. Notice the effects on accuracy of the orifice plate measurement can be up to 5% after a single elbow using a high beta ratio. The effect lessens using smaller beta ratios. Also notice the x-axis scale of the double elbows chart is much larger than the single elbow chart. This confirms that Type 1 swirl has a much longer lasting impact on flow measurement than Type 2 swirl.
Improving flow conditions
A user can make a determination about their installation knowing the above information. They have three options available to them:
- The user could plan the measurement point as far as possible from the disturbance. The more distance means the more likely the flow is well developed at that point. Some users may have plenty of straight pipe in their system and can meet the minimum requirements in the standards. For most users, creating the necessary straight inlet piping will come with additional expense.
- The user can accept the additional uncertainty that comes with a bad installation. This might be a fine solution in applications with low accuracy requirements. But most industrial applications cannot accept accuracy shifts on the order of ±5%.
- The user could follow the most common practice in the industry: use a flow conditioner.
Flow conditioners
The user of flow conditioners is an industry best practice for ensuring optimal flow measurement with an orifice plate. Flow conditioners come in a variety of designs but have one common goal: to condition the flow to well-developed conditions ahead of an orifice flow measurement point regardless of the disturbance ahead of it.
In the AGA Report No. 3, Section 2.3.1.7 “Flow Conditioners” classifies flow conditioners into two categories: straighteners and isolating flow conditioners.
“Flow straighteners are devices that effectively remove or reduce the swirl component of a flowing stream but may have limited ability to produce the flow conditions necessary to accurately replicate the orifice plate coefficient of discharge database values. Isolating flow conditioners are devices that effectively remove the swirl component from the flowing stream while redistributing the stream to produce the flow conditions that accurately replicate the orifice plate coefficient of discharge database values.”
Flow straighteners
Flow straighteners are low blockage, swirling reducing flow conditioners. Common examples of flow straighteners are tube bundles, example shown in Figure 10 and fin-type straightening vanes, example shown in Figure 11. Tube bundles can be designed with 19 or 7 tubes concentrically grouped in the pipe. The terminology around these can be confusing as tube bundles are sometimes sold as straightening vanes, but both fall into the category of flow straightener as described in AGA 3.
These types of flow conditioners are designed to remove swirl with their elongated dimensions. But since they are low blockages, they do very little to correct he asymmetry in the flow profile. In fact, Mattingly and Yeh also showed that flow straighteners can actually make asymmetry a more persistent flow disturbance, lasting much longer in terms of distance. This is because the flow straighteners will capture the asymmetry entering each tube and reduce the type 2 swirl. By reducing the type 2 swirl, the natural turbulence is diminished and the asymmetry does not break down as quickly.
In short, flow straighteners are not recommended for orifice plate measurement.
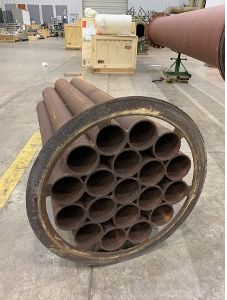

Isolating flow conditioners
Isolating flow conditioners have a blockage factor that forces the flow profile to redistribute as it passes through. This redistribution controls both the asymmetry and swirl disturbances. The design is typically a perforated plate with multiple holes designed to create a well-developed flow profile as soon as possible after the plate.
The search for the ideal pattern of holes to do this job was the subject of much research in the 1990’s as the need for flow conditioning became more and more relevant. A summary of the research from researchers such as Laws, Karnik, Zanker, Gallagher and others is fascinating but outside the scope of this paper. The most widely accepted design of this research was developed by Laws and has become known as the NOVA 50E design.
The NOVA 50E design, Figure 12, is a multi-hole flow conditioner with concentric rings of openings. 16 smaller holes around 8 midsized holes around one large central opening. The size and position of each hole is meant to stimulate the formation of a well-developed flow profile regardless of upstream disturbances. The “50” designation indicates that the plate has approximately a 50% blockage area in the flow path. The success of this design is the balance of three factors: 1) enough blockage to redistribute the flow profile, 2) large enough holes to allow passage of particles and 3) enough opening to reduce the pressure loss across the plate as much as possible. The NOVA design meets the requirements of AGA 3 Section 2.5.5 and APPENDIX 2-D.
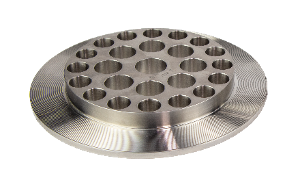
The design is universal for all flow conditions and disturbances. This advantage means a user can have one design flow conditioner for various pipeline installations and conditions. And it gives the user the assurance that most flow disturbances will be removed prior to flow measurement. For as much testing and research has been done of the effects of flow disturbances in a pipe, a user does not know the flow regime and development of their flow profile. Having a flow conditioner improves orifice plate measurement in all standard applications.
Conclusion
The use of a flow conditioner is recommended for all high accuracy orifice plate measurements. The recommended type of flow conditioner is the NOVA 50E design to remove most flow disturbances such as asymmetry and swirl. And users will benefit from the assurance that a well-designed flow conditioner will remove any unknown flow disturbances and problems that could diminish their measurement accuracy.
[1] Effects of pipe elbows and tube bundles onselected types of flowmeters, G.E. Mattingly, T.T. Yeh, Flow Measurement Instrumentation, Vol 2, January 1991
[2] US Patent 5,341,848 “Flow Conditioner”, 1994
Abstract
This paper discusses the effects of poor installations on orifice measurement and the best practices to achieve highest accuracy and performance. Flow disturbances are everywhere in pipelines and industrial applications. Knowing the types of disturbances, their effect on orifice measurement and how to correct those errors is valuable for anyone interested in accurate orifice flow measurement.
What is “Good” Flow
Most flowmeters are affected by the flow that they are trying to measure, orifice plate flowmeters included. Orifice plates measure best in “good” flow conditions and lose accuracy in “bad” conditions. There are several methods to describe and characterize good vs. bad flow conditions. When asked to describe good flow conditions, many users will use the term Laminar. This is a common yet minor misconception in flow engineering.
Laminar vs. Turbulent Flow
Laminar is a flow regime where the flow follows relatively straight lines down a pipe, Figure 1. If you were to follow a particle in the flow, it would go in a straight path and not cross paths with other particles flowing next to it. This is a regime with no turbulence. Laminar flow will happen in low flow and/or high viscous applications. In other words, the momentum forces are low and/or the viscous forces are high. Inherently this makes sense as higher velocities will encourage turbulence and higher viscosities will do the opposite.
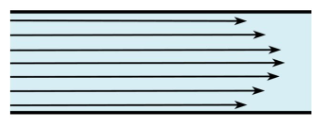
As useful tool is the Reynolds number, which is a dimensionless number used to quantify whether a flow application is in laminar flow. The Reynolds number equations is a follows:
Re=VρD/μ
Re = Reynolds number, dimensionless
V = flow velocity, ft/s
ρ = density, lbm/ft3
μ = dynamic viscosity, lbm/s·ft
The numerator of this equation combines the momentum forces in the flow, velocity, density and size. While the denominator are the inertial forces, viscosity. This follows the logic described earlier. The lower the Reynolds number, the more likely the flow regime is in a laminar state. Laminar flow is more likely to exist where the velocity, density or size is small, and/or where the viscosity is high. The commonly accepted value of laminar flow is Re < 4000. As the Reynolds number increases, the flow regime enters a transition phase between 4000 and 10,000. Above 10,000, the flow regime is considered to be turbulent.
Reynolds number - Flow regime
0 – 4,000 - Laminar
4000 – 10,000 - Transition
>10,000 - Turbulent
Turbulent flow, Figure 2, is the opposite of laminar flow in that the flow streams do not follow a straight or regular pattern. In turbulent flow the flow streams cross, small eddies occur, and mixing is more common. The word “turbulent” rightfully has negative connotations. No one wants to be on an airplane and fly through turbulence.
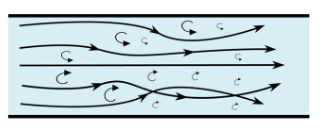
So why is Laminar the incorrect term to describe good flow? It’s not. It’s just not the world in which our flowmeters live. The vast majority of industrial pipelines are in the turbulent flow regime. Virtually all gas flows are turbulent due to the high velocities and low viscosities. Even most liquid flows are turbulent, except for some high viscosity products such as crude oil. Turbulent flow is better for orifice measurement because orifice plates were designed to measure it and their performance is well understood in those conditions.
A side note: Reynolds number is a very helpful in flow measurement. Since it is a dimensionless number, Reynolds can use a single number to describe a flow application. And that number can be used across applications. If the Reynolds number for an application is below 4000, that application is in the laminar flow regime, regardless of the size for example. Reynolds number is used when calibrating a flowmeter. Since the Reynolds number describes the flow in a single number, users can calibrate on one fluid and use the flowmeter in another fluid, knowing the performance will match at equal Reynolds numbers.
Flow profile
A better way to describe understand good vs. bad flow is the presence or absence of flow disturbances. Long, straight, unobstructed pipe will create undisturbed flow. The addition of common pipe elements will create disturbances. Common pipe elements can include single elbows, tees, two elbows in series, partially closed valves, pipe reductions or expansions, thermowells, and many more.
Just like the Reynolds number is a tool to understand the flow regime, the flow profile is a tool to visualize whether flow is disturbed or not. The flow profile attempts to show the velocity at difference points across the diameter of a flowing pipe. This can be physically measured in several ways such as with a single point Pitot tube sensor or with more complex tools such as laser doppler velocimetry. Typically, the view is across a full diameter, crossing through the midpoint of the pipe. A typical flow profile looks like Figure 3 for turbulent flow. Each arrow represents the velocity at points across a diameter of the pipe. The velocities are higher in the center of the pipe and lower near the pipe walls.
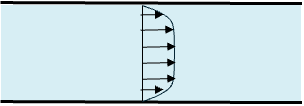
The friction on the pipe walls causes drag which slows down the fluid flow nearest to it. As the flow continues down the pipe, the next layer away from the pipe wall is slowed down slightly less. And so on until the effect of the pipe wall friction no longer affects the velocity. This is called the boundary layer effect and is created whenever flow passes over a surface. Notice the shape of the Figure 3 profile in turbulent flow is different than the shape in Figure 1. Laminar flow has a characteristic “bullet” shaped profile and turbulent has a flatter shape.
Well-developed flow is created when the boundary layer is fully established without disturbances. Put another way, well developed flow will not change its profile as it moves down the pipe. In the industrial flow measurement world, it’s also the definition of good flow and is very important in understanding flow through an orifice.
Power law estimation
When comparing whether a flow profile is well developed or not, a useful tool is the power law estimation. The power law gives a numerical estimation of a well-developed profile. The power law equation is:
u/umax = (1-r/R)1/n
u = velocity at measurement point
umax = max velocity in pipe
r = radius at measurement point
R = pipe radius
n = power
A value of n = 7 is typically used to fit the velocity profile for fully developed, turbulent flows. A higher value of n creates a flatter profile. A lower value creates a more bullet shape profile associated with laminar flow. A power law curve where
n = 7 is shown in Figure 4.
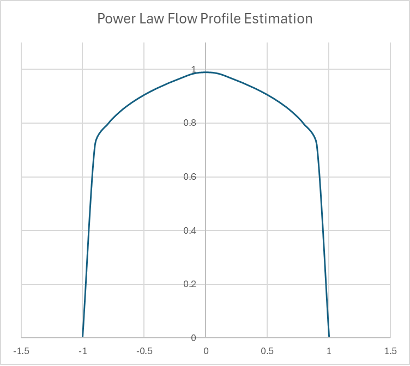
As flow is disturbed with the addition of pipe elements, the flow profile will change. For example, flow through a single elbow creates a skewed profile. The high velocity “core” of the pipe will be pushed to the opposite wall of the pipe, creating an asymmetry where the maximum velocity is no longer in the middle of the pipe. Single elbows and other elements can create asymmetry in the flow profile which is shown well in Figure 5.
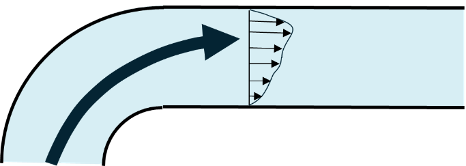
Swirling flow
The flow profile does not capture another type of flow disturbance called swirling flow. Swirling flow is when the flow has a crossflow element. Without swirl the flow will run straight down the pipe, with 0° in relation to the centerline of the pipe. If crossflow is present, the flow streams can have a swirl angle, up to 20° in severe cases.
There are two general types of swirl disturbances, Type 1 and Type 2 swirls. Type 1 swirl moves in one directional rotation across the pipe. This is also known as whole body swirl, Figure 6. Close coupled double elbows out of plane are a common cause of Type 1 swirl, along with headers, pumps and compressors. Type 2 swirl introduces two counter rotating swirls rotating in opposite directions, Figure 7. This is usually created after single elbows.
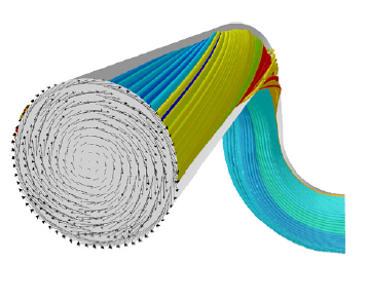
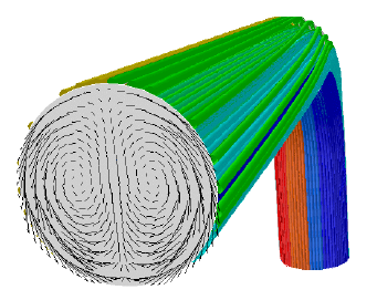
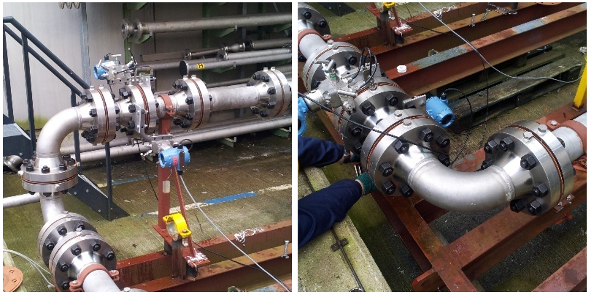
Orifice plate flow measurements
Orifice plates measurement have a century-long track record of continuous use and improvement in industrial applications. No other flow technology has the international volume of understanding and acceptance as orifice plates. Orifice plates are often described as “a hole in a plate” and often ridiculed for that simplicity. Yet it is the simplicity of an orifice plate that makes it so elegant. Leonardo da Vinci once said, “Simplicity is the ultimate sophistication”. The design of the orifice plate makes it possible to manufacture with precision and repeatability. Making one orifice plate measure the same as the next one with matching dimensions. A dimensional inspection is all that is needed to “calibrate” an orifice plate.
Knowing that two identical orifice plates will measure the same (within known uncertainties) is one of the reasons why they are the most widely used industrial flow technology even after 100 years. In today’s world, a user can replace an orifice plate and know the uncertainty of the measurement will not change, even without a flow calibration – something no other flow technology can match!
This also means that a flow calibration once done on a known orifice plate size, can be applied to all other matching orifice plates. Over the decades a massive database of traceable orifice calibrations was completed and used to create the de facto standards for orifice flow measurement. The American standards are the AGA Report No 3 and API 14.3 standards for natural measurement using an orifice plate. The international standard for orifice plates is ISO 5167.
The orifice performance in that technical database (which includes over 30,000 data points!) was tested in well-developed flow conditions. The standards confirm that measurement in matching conditions and dimensions will perform at custody transfer levels of accuracy. And since all the data points were tested in well-developed flow conditions, the standards require the same for accurate measurement.
Effect of flow disturbances on orifice measurement
If a user’s flow conditions are not well developed, with asymmetric or swirling flow, the accuracy will be affected. The effect on accuracy will depend on several factors, including the type of disturbance and the relative distance of the disturbance to the orifice location.
As the distance from the disturbance to the orifice plate increases, the flow will naturally return to a well-developed state due to the turbulence in the flow (turbulence helps us here). The distance needed to return to well-developed flow depends mostly on the type of disturbance. The AGA/API standards recommend up to 44 pipe diameters of straight pipe after double elbow to achieve well developed flow.
Shown below are two sets of flow calibration data from Mattingly and Yeh measuring three different orifice bore sizes (beta ratios) at various distances from a disturbance. Figure 8 shows single elbow effects.Figure 9 shows effects from close coupled, double elbows out of plane.
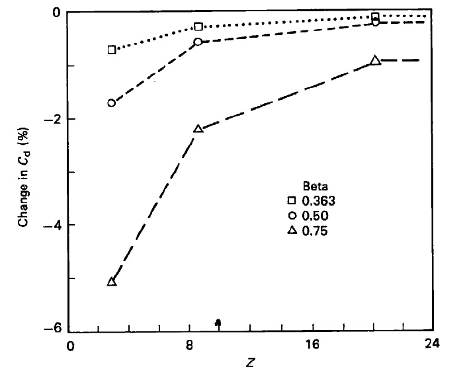
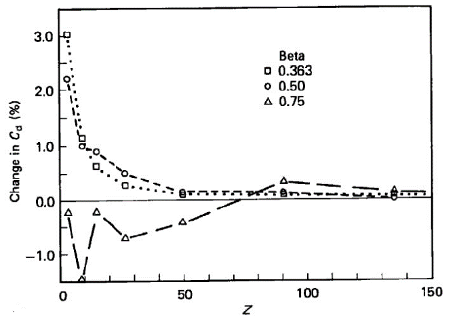
The effect of the disturbance diminishes with distance, approaching zero effect. Notice the effects on accuracy of the orifice plate measurement can be up to 5% after a single elbow using a high beta ratio. The effect lessens using smaller beta ratios. Also notice the x-axis scale of the double elbows chart is much larger than the single elbow chart. This confirms that Type 1 swirl has a much longer lasting impact on flow measurement than Type 2 swirl.
Improving flow conditions
A user can make a determination about their installation knowing the above information. They have three options available to them:
- The user could plan the measurement point as far as possible from the disturbance. The more distance means the more likely the flow is well developed at that point. Some users may have plenty of straight pipe in their system and can meet the minimum requirements in the standards. For most users, creating the necessary straight inlet piping will come with additional expense.
- The user can accept the additional uncertainty that comes with a bad installation. This might be a fine solution in applications with low accuracy requirements. But most industrial applications cannot accept accuracy shifts on the order of ±5%.
- The user could follow the most common practice in the industry: use a flow conditioner.
Flow conditioners
The user of flow conditioners is an industry best practice for ensuring optimal flow measurement with an orifice plate. Flow conditioners come in a variety of designs but have one common goal: to condition the flow to well-developed conditions ahead of an orifice flow measurement point regardless of the disturbance ahead of it.
In the AGA Report No. 3, Section 2.3.1.7 “Flow Conditioners” classifies flow conditioners into two categories: straighteners and isolating flow conditioners.
“Flow straighteners are devices that effectively remove or reduce the swirl component of a flowing stream but may have limited ability to produce the flow conditions necessary to accurately replicate the orifice plate coefficient of discharge database values. Isolating flow conditioners are devices that effectively remove the swirl component from the flowing stream while redistributing the stream to produce the flow conditions that accurately replicate the orifice plate coefficient of discharge database values.”
Flow straighteners
Flow straighteners are low blockage, swirling reducing flow conditioners. Common examples of flow straighteners are tube bundles, example shown in Figure 10 and fin-type straightening vanes, example shown in Figure 11. Tube bundles can be designed with 19 or 7 tubes concentrically grouped in the pipe. The terminology around these can be confusing as tube bundles are sometimes sold as straightening vanes, but both fall into the category of flow straightener as described in AGA 3.
These types of flow conditioners are designed to remove swirl with their elongated dimensions. But since they are low blockages, they do very little to correct he asymmetry in the flow profile. In fact, Mattingly and Yeh also showed that flow straighteners can actually make asymmetry a more persistent flow disturbance, lasting much longer in terms of distance. This is because the flow straighteners will capture the asymmetry entering each tube and reduce the type 2 swirl. By reducing the type 2 swirl, the natural turbulence is diminished and the asymmetry does not break down as quickly.
In short, flow straighteners are not recommended for orifice plate measurement.
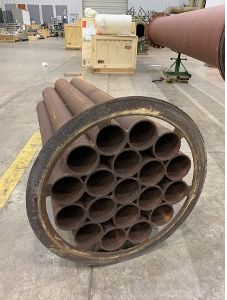

Isolating flow conditioners
Isolating flow conditioners have a blockage factor that forces the flow profile to redistribute as it passes through. This redistribution controls both the asymmetry and swirl disturbances. The design is typically a perforated plate with multiple holes designed to create a well-developed flow profile as soon as possible after the plate.
The search for the ideal pattern of holes to do this job was the subject of much research in the 1990’s as the need for flow conditioning became more and more relevant. A summary of the research from researchers such as Laws, Karnik, Zanker, Gallagher and others is fascinating but outside the scope of this paper. The most widely accepted design of this research was developed by Laws and has become known as the NOVA 50E design.
The NOVA 50E design, Figure 12, is a multi-hole flow conditioner with concentric rings of openings. 16 smaller holes around 8 midsized holes around one large central opening. The size and position of each hole is meant to stimulate the formation of a well-developed flow profile regardless of upstream disturbances. The “50” designation indicates that the plate has approximately a 50% blockage area in the flow path. The success of this design is the balance of three factors: 1) enough blockage to redistribute the flow profile, 2) large enough holes to allow passage of particles and 3) enough opening to reduce the pressure loss across the plate as much as possible. The NOVA design meets the requirements of AGA 3 Section 2.5.5 and APPENDIX 2-D.
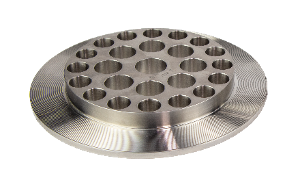
The design is universal for all flow conditions and disturbances. This advantage means a user can have one design flow conditioner for various pipeline installations and conditions. And it gives the user the assurance that most flow disturbances will be removed prior to flow measurement. For as much testing and research has been done of the effects of flow disturbances in a pipe, a user does not know the flow regime and development of their flow profile. Having a flow conditioner improves orifice plate measurement in all standard applications.
Conclusion
The use of a flow conditioner is recommended for all high accuracy orifice plate measurements. The recommended type of flow conditioner is the NOVA 50E design to remove most flow disturbances such as asymmetry and swirl. And users will benefit from the assurance that a well-designed flow conditioner will remove any unknown flow disturbances and problems that could diminish their measurement accuracy.
[1] Effects of pipe elbows and tube bundles onselected types of flowmeters, G.E. Mattingly, T.T. Yeh, Flow Measurement Instrumentation, Vol 2, January 1991
[2] US Patent 5,341,848 “Flow Conditioner”, 1994
Abstract
This paper discusses the effects of poor installations on orifice measurement and the best practices to achieve highest accuracy and performance. Flow disturbances are everywhere in pipelines and industrial applications. Knowing the types of disturbances, their effect on orifice measurement and how to correct those errors is valuable for anyone interested in accurate orifice flow measurement.
What is “Good” Flow
Most flowmeters are affected by the flow that they are trying to measure, orifice plate flowmeters included. Orifice plates measure best in “good” flow conditions and lose accuracy in “bad” conditions. There are several methods to describe and characterize good vs. bad flow conditions. When asked to describe good flow conditions, many users will use the term Laminar. This is a common yet minor misconception in flow engineering.
Laminar vs. Turbulent Flow
Laminar is a flow regime where the flow follows relatively straight lines down a pipe, Figure 1. If you were to follow a particle in the flow, it would go in a straight path and not cross paths with other particles flowing next to it. This is a regime with no turbulence. Laminar flow will happen in low flow and/or high viscous applications. In other words, the momentum forces are low and/or the viscous forces are high. Inherently this makes sense as higher velocities will encourage turbulence and higher viscosities will do the opposite.
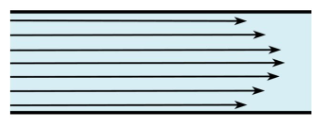
As useful tool is the Reynolds number, which is a dimensionless number used to quantify whether a flow application is in laminar flow. The Reynolds number equations is a follows:
Re=VρD/μ
Re = Reynolds number, dimensionless
V = flow velocity, ft/s
ρ = density, lbm/ft3
μ = dynamic viscosity, lbm/s·ft
The numerator of this equation combines the momentum forces in the flow, velocity, density and size. While the denominator are the inertial forces, viscosity. This follows the logic described earlier. The lower the Reynolds number, the more likely the flow regime is in a laminar state. Laminar flow is more likely to exist where the velocity, density or size is small, and/or where the viscosity is high. The commonly accepted value of laminar flow is Re < 4000. As the Reynolds number increases, the flow regime enters a transition phase between 4000 and 10,000. Above 10,000, the flow regime is considered to be turbulent.
Reynolds number - Flow regime
0 – 4,000 - Laminar
4000 – 10,000 - Transition
>10,000 - Turbulent
Turbulent flow, Figure 2, is the opposite of laminar flow in that the flow streams do not follow a straight or regular pattern. In turbulent flow the flow streams cross, small eddies occur, and mixing is more common. The word “turbulent” rightfully has negative connotations. No one wants to be on an airplane and fly through turbulence.
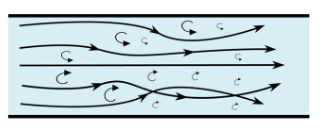
So why is Laminar the incorrect term to describe good flow? It’s not. It’s just not the world in which our flowmeters live. The vast majority of industrial pipelines are in the turbulent flow regime. Virtually all gas flows are turbulent due to the high velocities and low viscosities. Even most liquid flows are turbulent, except for some high viscosity products such as crude oil. Turbulent flow is better for orifice measurement because orifice plates were designed to measure it and their performance is well understood in those conditions.
A side note: Reynolds number is a very helpful in flow measurement. Since it is a dimensionless number, Reynolds can use a single number to describe a flow application. And that number can be used across applications. If the Reynolds number for an application is below 4000, that application is in the laminar flow regime, regardless of the size for example. Reynolds number is used when calibrating a flowmeter. Since the Reynolds number describes the flow in a single number, users can calibrate on one fluid and use the flowmeter in another fluid, knowing the performance will match at equal Reynolds numbers.
Flow profile
A better way to describe understand good vs. bad flow is the presence or absence of flow disturbances. Long, straight, unobstructed pipe will create undisturbed flow. The addition of common pipe elements will create disturbances. Common pipe elements can include single elbows, tees, two elbows in series, partially closed valves, pipe reductions or expansions, thermowells, and many more.
Just like the Reynolds number is a tool to understand the flow regime, the flow profile is a tool to visualize whether flow is disturbed or not. The flow profile attempts to show the velocity at difference points across the diameter of a flowing pipe. This can be physically measured in several ways such as with a single point Pitot tube sensor or with more complex tools such as laser doppler velocimetry. Typically, the view is across a full diameter, crossing through the midpoint of the pipe. A typical flow profile looks like Figure 3 for turbulent flow. Each arrow represents the velocity at points across a diameter of the pipe. The velocities are higher in the center of the pipe and lower near the pipe walls.
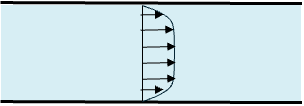
The friction on the pipe walls causes drag which slows down the fluid flow nearest to it. As the flow continues down the pipe, the next layer away from the pipe wall is slowed down slightly less. And so on until the effect of the pipe wall friction no longer affects the velocity. This is called the boundary layer effect and is created whenever flow passes over a surface. Notice the shape of the Figure 3 profile in turbulent flow is different than the shape in Figure 1. Laminar flow has a characteristic “bullet” shaped profile and turbulent has a flatter shape.
Well-developed flow is created when the boundary layer is fully established without disturbances. Put another way, well developed flow will not change its profile as it moves down the pipe. In the industrial flow measurement world, it’s also the definition of good flow and is very important in understanding flow through an orifice.
Power law estimation
When comparing whether a flow profile is well developed or not, a useful tool is the power law estimation. The power law gives a numerical estimation of a well-developed profile. The power law equation is:
u/umax = (1-r/R)1/n
u = velocity at measurement point
umax = max velocity in pipe
r = radius at measurement point
R = pipe radius
n = power
A value of n = 7 is typically used to fit the velocity profile for fully developed, turbulent flows. A higher value of n creates a flatter profile. A lower value creates a more bullet shape profile associated with laminar flow. A power law curve where
n = 7 is shown in Figure 4.
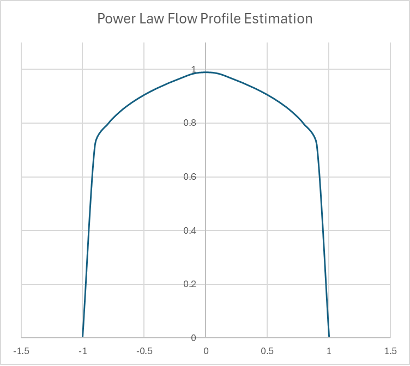
As flow is disturbed with the addition of pipe elements, the flow profile will change. For example, flow through a single elbow creates a skewed profile. The high velocity “core” of the pipe will be pushed to the opposite wall of the pipe, creating an asymmetry where the maximum velocity is no longer in the middle of the pipe. Single elbows and other elements can create asymmetry in the flow profile which is shown well in Figure 5.
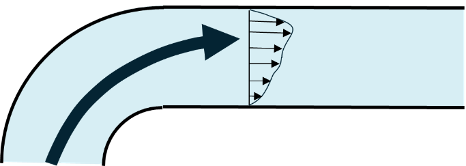
Swirling flow
The flow profile does not capture another type of flow disturbance called swirling flow. Swirling flow is when the flow has a crossflow element. Without swirl the flow will run straight down the pipe, with 0° in relation to the centerline of the pipe. If crossflow is present, the flow streams can have a swirl angle, up to 20° in severe cases.
There are two general types of swirl disturbances, Type 1 and Type 2 swirls. Type 1 swirl moves in one directional rotation across the pipe. This is also known as whole body swirl, Figure 6. Close coupled double elbows out of plane are a common cause of Type 1 swirl, along with headers, pumps and compressors. Type 2 swirl introduces two counter rotating swirls rotating in opposite directions, Figure 7. This is usually created after single elbows.
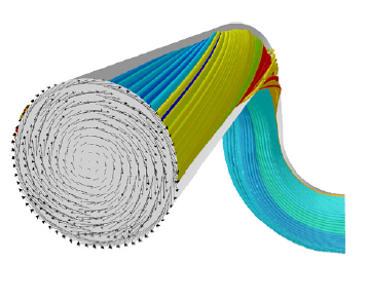
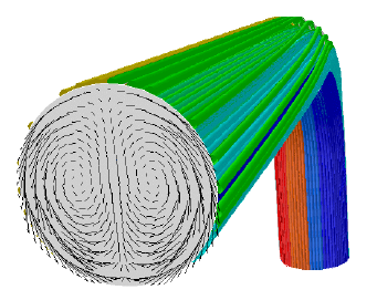
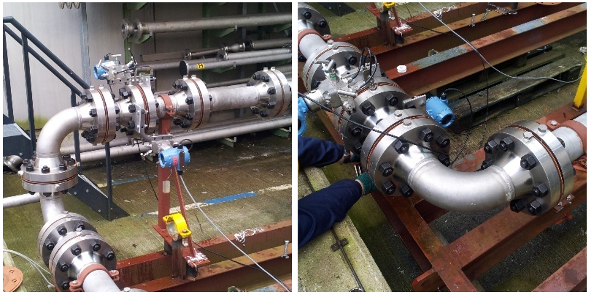
Orifice plate flow measurements
Orifice plates measurement have a century-long track record of continuous use and improvement in industrial applications. No other flow technology has the international volume of understanding and acceptance as orifice plates. Orifice plates are often described as “a hole in a plate” and often ridiculed for that simplicity. Yet it is the simplicity of an orifice plate that makes it so elegant. Leonardo da Vinci once said, “Simplicity is the ultimate sophistication”. The design of the orifice plate makes it possible to manufacture with precision and repeatability. Making one orifice plate measure the same as the next one with matching dimensions. A dimensional inspection is all that is needed to “calibrate” an orifice plate.
Knowing that two identical orifice plates will measure the same (within known uncertainties) is one of the reasons why they are the most widely used industrial flow technology even after 100 years. In today’s world, a user can replace an orifice plate and know the uncertainty of the measurement will not change, even without a flow calibration – something no other flow technology can match!
This also means that a flow calibration once done on a known orifice plate size, can be applied to all other matching orifice plates. Over the decades a massive database of traceable orifice calibrations was completed and used to create the de facto standards for orifice flow measurement. The American standards are the AGA Report No 3 and API 14.3 standards for natural measurement using an orifice plate. The international standard for orifice plates is ISO 5167.
The orifice performance in that technical database (which includes over 30,000 data points!) was tested in well-developed flow conditions. The standards confirm that measurement in matching conditions and dimensions will perform at custody transfer levels of accuracy. And since all the data points were tested in well-developed flow conditions, the standards require the same for accurate measurement.
Effect of flow disturbances on orifice measurement
If a user’s flow conditions are not well developed, with asymmetric or swirling flow, the accuracy will be affected. The effect on accuracy will depend on several factors, including the type of disturbance and the relative distance of the disturbance to the orifice location.
As the distance from the disturbance to the orifice plate increases, the flow will naturally return to a well-developed state due to the turbulence in the flow (turbulence helps us here). The distance needed to return to well-developed flow depends mostly on the type of disturbance. The AGA/API standards recommend up to 44 pipe diameters of straight pipe after double elbow to achieve well developed flow.
Shown below are two sets of flow calibration data from Mattingly and Yeh measuring three different orifice bore sizes (beta ratios) at various distances from a disturbance. Figure 8 shows single elbow effects.Figure 9 shows effects from close coupled, double elbows out of plane.
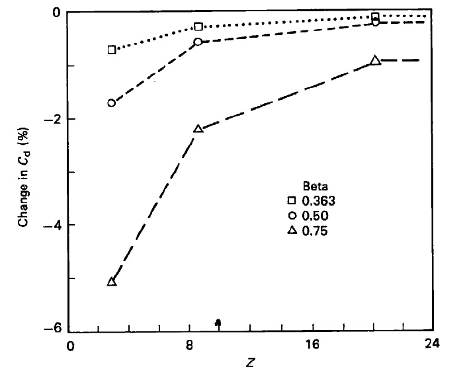
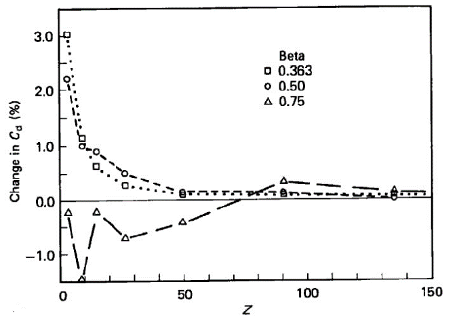
The effect of the disturbance diminishes with distance, approaching zero effect. Notice the effects on accuracy of the orifice plate measurement can be up to 5% after a single elbow using a high beta ratio. The effect lessens using smaller beta ratios. Also notice the x-axis scale of the double elbows chart is much larger than the single elbow chart. This confirms that Type 1 swirl has a much longer lasting impact on flow measurement than Type 2 swirl.
Improving flow conditions
A user can make a determination about their installation knowing the above information. They have three options available to them:
- The user could plan the measurement point as far as possible from the disturbance. The more distance means the more likely the flow is well developed at that point. Some users may have plenty of straight pipe in their system and can meet the minimum requirements in the standards. For most users, creating the necessary straight inlet piping will come with additional expense.
- The user can accept the additional uncertainty that comes with a bad installation. This might be a fine solution in applications with low accuracy requirements. But most industrial applications cannot accept accuracy shifts on the order of ±5%.
- The user could follow the most common practice in the industry: use a flow conditioner.
Flow conditioners
The user of flow conditioners is an industry best practice for ensuring optimal flow measurement with an orifice plate. Flow conditioners come in a variety of designs but have one common goal: to condition the flow to well-developed conditions ahead of an orifice flow measurement point regardless of the disturbance ahead of it.
In the AGA Report No. 3, Section 2.3.1.7 “Flow Conditioners” classifies flow conditioners into two categories: straighteners and isolating flow conditioners.
“Flow straighteners are devices that effectively remove or reduce the swirl component of a flowing stream but may have limited ability to produce the flow conditions necessary to accurately replicate the orifice plate coefficient of discharge database values. Isolating flow conditioners are devices that effectively remove the swirl component from the flowing stream while redistributing the stream to produce the flow conditions that accurately replicate the orifice plate coefficient of discharge database values.”
Flow straighteners
Flow straighteners are low blockage, swirling reducing flow conditioners. Common examples of flow straighteners are tube bundles, example shown in Figure 10 and fin-type straightening vanes, example shown in Figure 11. Tube bundles can be designed with 19 or 7 tubes concentrically grouped in the pipe. The terminology around these can be confusing as tube bundles are sometimes sold as straightening vanes, but both fall into the category of flow straightener as described in AGA 3.
These types of flow conditioners are designed to remove swirl with their elongated dimensions. But since they are low blockages, they do very little to correct he asymmetry in the flow profile. In fact, Mattingly and Yeh also showed that flow straighteners can actually make asymmetry a more persistent flow disturbance, lasting much longer in terms of distance. This is because the flow straighteners will capture the asymmetry entering each tube and reduce the type 2 swirl. By reducing the type 2 swirl, the natural turbulence is diminished and the asymmetry does not break down as quickly.
In short, flow straighteners are not recommended for orifice plate measurement.
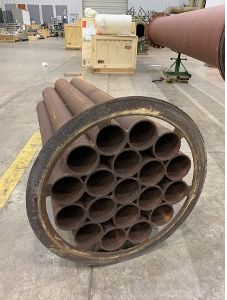

Isolating flow conditioners
Isolating flow conditioners have a blockage factor that forces the flow profile to redistribute as it passes through. This redistribution controls both the asymmetry and swirl disturbances. The design is typically a perforated plate with multiple holes designed to create a well-developed flow profile as soon as possible after the plate.
The search for the ideal pattern of holes to do this job was the subject of much research in the 1990’s as the need for flow conditioning became more and more relevant. A summary of the research from researchers such as Laws, Karnik, Zanker, Gallagher and others is fascinating but outside the scope of this paper. The most widely accepted design of this research was developed by Laws and has become known as the NOVA 50E design.
The NOVA 50E design, Figure 12, is a multi-hole flow conditioner with concentric rings of openings. 16 smaller holes around 8 midsized holes around one large central opening. The size and position of each hole is meant to stimulate the formation of a well-developed flow profile regardless of upstream disturbances. The “50” designation indicates that the plate has approximately a 50% blockage area in the flow path. The success of this design is the balance of three factors: 1) enough blockage to redistribute the flow profile, 2) large enough holes to allow passage of particles and 3) enough opening to reduce the pressure loss across the plate as much as possible. The NOVA design meets the requirements of AGA 3 Section 2.5.5 and APPENDIX 2-D.
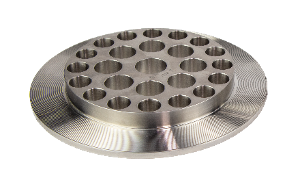
The design is universal for all flow conditions and disturbances. This advantage means a user can have one design flow conditioner for various pipeline installations and conditions. And it gives the user the assurance that most flow disturbances will be removed prior to flow measurement. For as much testing and research has been done of the effects of flow disturbances in a pipe, a user does not know the flow regime and development of their flow profile. Having a flow conditioner improves orifice plate measurement in all standard applications.
Conclusion
The use of a flow conditioner is recommended for all high accuracy orifice plate measurements. The recommended type of flow conditioner is the NOVA 50E design to remove most flow disturbances such as asymmetry and swirl. And users will benefit from the assurance that a well-designed flow conditioner will remove any unknown flow disturbances and problems that could diminish their measurement accuracy.
[1] Effects of pipe elbows and tube bundles onselected types of flowmeters, G.E. Mattingly, T.T. Yeh, Flow Measurement Instrumentation, Vol 2, January 1991
[2] US Patent 5,341,848 “Flow Conditioner”, 1994
Abstract
This paper discusses the effects of poor installations on orifice measurement and the best practices to achieve highest accuracy and performance. Flow disturbances are everywhere in pipelines and industrial applications. Knowing the types of disturbances, their effect on orifice measurement and how to correct those errors is valuable for anyone interested in accurate orifice flow measurement.
What is “Good” Flow
Most flowmeters are affected by the flow that they are trying to measure, orifice plate flowmeters included. Orifice plates measure best in “good” flow conditions and lose accuracy in “bad” conditions. There are several methods to describe and characterize good vs. bad flow conditions. When asked to describe good flow conditions, many users will use the term Laminar. This is a common yet minor misconception in flow engineering.
Laminar vs. Turbulent Flow
Laminar is a flow regime where the flow follows relatively straight lines down a pipe, Figure 1. If you were to follow a particle in the flow, it would go in a straight path and not cross paths with other particles flowing next to it. This is a regime with no turbulence. Laminar flow will happen in low flow and/or high viscous applications. In other words, the momentum forces are low and/or the viscous forces are high. Inherently this makes sense as higher velocities will encourage turbulence and higher viscosities will do the opposite.
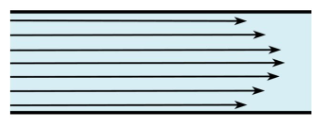
As useful tool is the Reynolds number, which is a dimensionless number used to quantify whether a flow application is in laminar flow. The Reynolds number equations is a follows:
Re=VρD/μ
Re = Reynolds number, dimensionless
V = flow velocity, ft/s
ρ = density, lbm/ft3
μ = dynamic viscosity, lbm/s·ft
The numerator of this equation combines the momentum forces in the flow, velocity, density and size. While the denominator are the inertial forces, viscosity. This follows the logic described earlier. The lower the Reynolds number, the more likely the flow regime is in a laminar state. Laminar flow is more likely to exist where the velocity, density or size is small, and/or where the viscosity is high. The commonly accepted value of laminar flow is Re < 4000. As the Reynolds number increases, the flow regime enters a transition phase between 4000 and 10,000. Above 10,000, the flow regime is considered to be turbulent.
Reynolds number - Flow regime
0 – 4,000 - Laminar
4000 – 10,000 - Transition
>10,000 - Turbulent
Turbulent flow, Figure 2, is the opposite of laminar flow in that the flow streams do not follow a straight or regular pattern. In turbulent flow the flow streams cross, small eddies occur, and mixing is more common. The word “turbulent” rightfully has negative connotations. No one wants to be on an airplane and fly through turbulence.
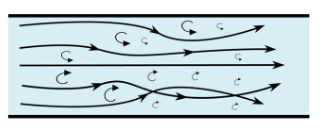
So why is Laminar the incorrect term to describe good flow? It’s not. It’s just not the world in which our flowmeters live. The vast majority of industrial pipelines are in the turbulent flow regime. Virtually all gas flows are turbulent due to the high velocities and low viscosities. Even most liquid flows are turbulent, except for some high viscosity products such as crude oil. Turbulent flow is better for orifice measurement because orifice plates were designed to measure it and their performance is well understood in those conditions.
A side note: Reynolds number is a very helpful in flow measurement. Since it is a dimensionless number, Reynolds can use a single number to describe a flow application. And that number can be used across applications. If the Reynolds number for an application is below 4000, that application is in the laminar flow regime, regardless of the size for example. Reynolds number is used when calibrating a flowmeter. Since the Reynolds number describes the flow in a single number, users can calibrate on one fluid and use the flowmeter in another fluid, knowing the performance will match at equal Reynolds numbers.
Flow profile
A better way to describe understand good vs. bad flow is the presence or absence of flow disturbances. Long, straight, unobstructed pipe will create undisturbed flow. The addition of common pipe elements will create disturbances. Common pipe elements can include single elbows, tees, two elbows in series, partially closed valves, pipe reductions or expansions, thermowells, and many more.
Just like the Reynolds number is a tool to understand the flow regime, the flow profile is a tool to visualize whether flow is disturbed or not. The flow profile attempts to show the velocity at difference points across the diameter of a flowing pipe. This can be physically measured in several ways such as with a single point Pitot tube sensor or with more complex tools such as laser doppler velocimetry. Typically, the view is across a full diameter, crossing through the midpoint of the pipe. A typical flow profile looks like Figure 3 for turbulent flow. Each arrow represents the velocity at points across a diameter of the pipe. The velocities are higher in the center of the pipe and lower near the pipe walls.
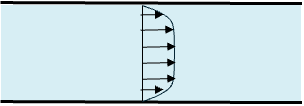
The friction on the pipe walls causes drag which slows down the fluid flow nearest to it. As the flow continues down the pipe, the next layer away from the pipe wall is slowed down slightly less. And so on until the effect of the pipe wall friction no longer affects the velocity. This is called the boundary layer effect and is created whenever flow passes over a surface. Notice the shape of the Figure 3 profile in turbulent flow is different than the shape in Figure 1. Laminar flow has a characteristic “bullet” shaped profile and turbulent has a flatter shape.
Well-developed flow is created when the boundary layer is fully established without disturbances. Put another way, well developed flow will not change its profile as it moves down the pipe. In the industrial flow measurement world, it’s also the definition of good flow and is very important in understanding flow through an orifice.
Power law estimation
When comparing whether a flow profile is well developed or not, a useful tool is the power law estimation. The power law gives a numerical estimation of a well-developed profile. The power law equation is:
u/umax = (1-r/R)1/n
u = velocity at measurement point
umax = max velocity in pipe
r = radius at measurement point
R = pipe radius
n = power
A value of n = 7 is typically used to fit the velocity profile for fully developed, turbulent flows. A higher value of n creates a flatter profile. A lower value creates a more bullet shape profile associated with laminar flow. A power law curve where
n = 7 is shown in Figure 4.
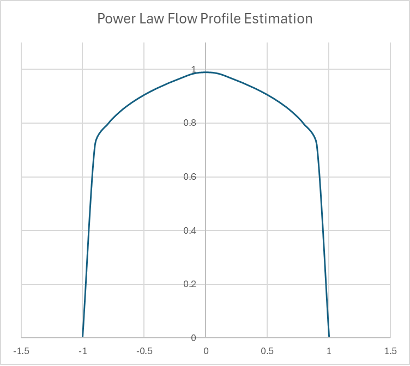
As flow is disturbed with the addition of pipe elements, the flow profile will change. For example, flow through a single elbow creates a skewed profile. The high velocity “core” of the pipe will be pushed to the opposite wall of the pipe, creating an asymmetry where the maximum velocity is no longer in the middle of the pipe. Single elbows and other elements can create asymmetry in the flow profile which is shown well in Figure 5.
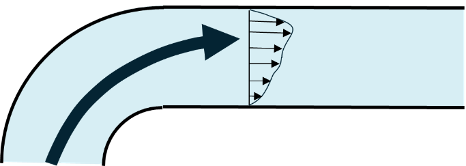
Swirling flow
The flow profile does not capture another type of flow disturbance called swirling flow. Swirling flow is when the flow has a crossflow element. Without swirl the flow will run straight down the pipe, with 0° in relation to the centerline of the pipe. If crossflow is present, the flow streams can have a swirl angle, up to 20° in severe cases.
There are two general types of swirl disturbances, Type 1 and Type 2 swirls. Type 1 swirl moves in one directional rotation across the pipe. This is also known as whole body swirl, Figure 6. Close coupled double elbows out of plane are a common cause of Type 1 swirl, along with headers, pumps and compressors. Type 2 swirl introduces two counter rotating swirls rotating in opposite directions, Figure 7. This is usually created after single elbows.
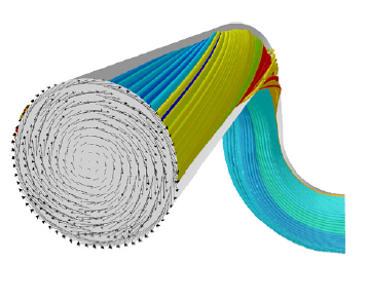
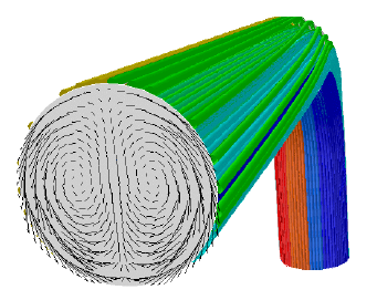
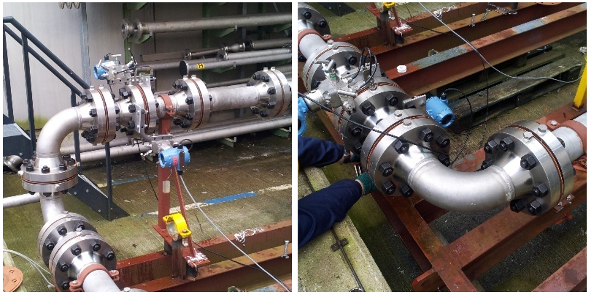
Orifice plate flow measurements
Orifice plates measurement have a century-long track record of continuous use and improvement in industrial applications. No other flow technology has the international volume of understanding and acceptance as orifice plates. Orifice plates are often described as “a hole in a plate” and often ridiculed for that simplicity. Yet it is the simplicity of an orifice plate that makes it so elegant. Leonardo da Vinci once said, “Simplicity is the ultimate sophistication”. The design of the orifice plate makes it possible to manufacture with precision and repeatability. Making one orifice plate measure the same as the next one with matching dimensions. A dimensional inspection is all that is needed to “calibrate” an orifice plate.
Knowing that two identical orifice plates will measure the same (within known uncertainties) is one of the reasons why they are the most widely used industrial flow technology even after 100 years. In today’s world, a user can replace an orifice plate and know the uncertainty of the measurement will not change, even without a flow calibration – something no other flow technology can match!
This also means that a flow calibration once done on a known orifice plate size, can be applied to all other matching orifice plates. Over the decades a massive database of traceable orifice calibrations was completed and used to create the de facto standards for orifice flow measurement. The American standards are the AGA Report No 3 and API 14.3 standards for natural measurement using an orifice plate. The international standard for orifice plates is ISO 5167.
The orifice performance in that technical database (which includes over 30,000 data points!) was tested in well-developed flow conditions. The standards confirm that measurement in matching conditions and dimensions will perform at custody transfer levels of accuracy. And since all the data points were tested in well-developed flow conditions, the standards require the same for accurate measurement.
Effect of flow disturbances on orifice measurement
If a user’s flow conditions are not well developed, with asymmetric or swirling flow, the accuracy will be affected. The effect on accuracy will depend on several factors, including the type of disturbance and the relative distance of the disturbance to the orifice location.
As the distance from the disturbance to the orifice plate increases, the flow will naturally return to a well-developed state due to the turbulence in the flow (turbulence helps us here). The distance needed to return to well-developed flow depends mostly on the type of disturbance. The AGA/API standards recommend up to 44 pipe diameters of straight pipe after double elbow to achieve well developed flow.
Shown below are two sets of flow calibration data from Mattingly and Yeh measuring three different orifice bore sizes (beta ratios) at various distances from a disturbance. Figure 8 shows single elbow effects.Figure 9 shows effects from close coupled, double elbows out of plane.
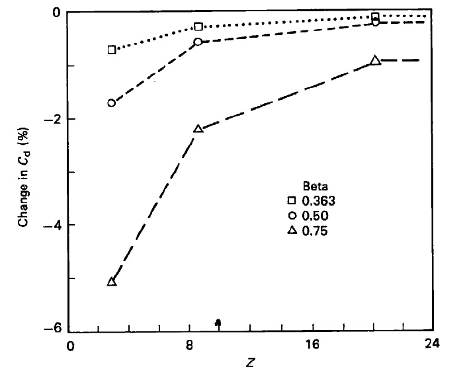
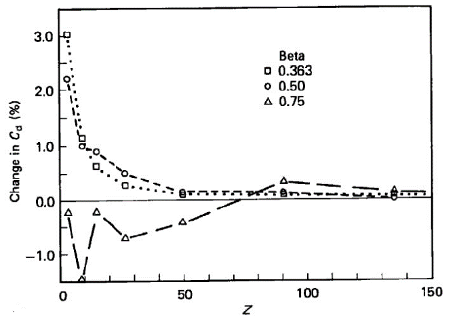
The effect of the disturbance diminishes with distance, approaching zero effect. Notice the effects on accuracy of the orifice plate measurement can be up to 5% after a single elbow using a high beta ratio. The effect lessens using smaller beta ratios. Also notice the x-axis scale of the double elbows chart is much larger than the single elbow chart. This confirms that Type 1 swirl has a much longer lasting impact on flow measurement than Type 2 swirl.
Improving flow conditions
A user can make a determination about their installation knowing the above information. They have three options available to them:
- The user could plan the measurement point as far as possible from the disturbance. The more distance means the more likely the flow is well developed at that point. Some users may have plenty of straight pipe in their system and can meet the minimum requirements in the standards. For most users, creating the necessary straight inlet piping will come with additional expense.
- The user can accept the additional uncertainty that comes with a bad installation. This might be a fine solution in applications with low accuracy requirements. But most industrial applications cannot accept accuracy shifts on the order of ±5%.
- The user could follow the most common practice in the industry: use a flow conditioner.
Flow conditioners
The user of flow conditioners is an industry best practice for ensuring optimal flow measurement with an orifice plate. Flow conditioners come in a variety of designs but have one common goal: to condition the flow to well-developed conditions ahead of an orifice flow measurement point regardless of the disturbance ahead of it.
In the AGA Report No. 3, Section 2.3.1.7 “Flow Conditioners” classifies flow conditioners into two categories: straighteners and isolating flow conditioners.
“Flow straighteners are devices that effectively remove or reduce the swirl component of a flowing stream but may have limited ability to produce the flow conditions necessary to accurately replicate the orifice plate coefficient of discharge database values. Isolating flow conditioners are devices that effectively remove the swirl component from the flowing stream while redistributing the stream to produce the flow conditions that accurately replicate the orifice plate coefficient of discharge database values.”
Flow straighteners
Flow straighteners are low blockage, swirling reducing flow conditioners. Common examples of flow straighteners are tube bundles, example shown in Figure 10 and fin-type straightening vanes, example shown in Figure 11. Tube bundles can be designed with 19 or 7 tubes concentrically grouped in the pipe. The terminology around these can be confusing as tube bundles are sometimes sold as straightening vanes, but both fall into the category of flow straightener as described in AGA 3.
These types of flow conditioners are designed to remove swirl with their elongated dimensions. But since they are low blockages, they do very little to correct he asymmetry in the flow profile. In fact, Mattingly and Yeh also showed that flow straighteners can actually make asymmetry a more persistent flow disturbance, lasting much longer in terms of distance. This is because the flow straighteners will capture the asymmetry entering each tube and reduce the type 2 swirl. By reducing the type 2 swirl, the natural turbulence is diminished and the asymmetry does not break down as quickly.
In short, flow straighteners are not recommended for orifice plate measurement.
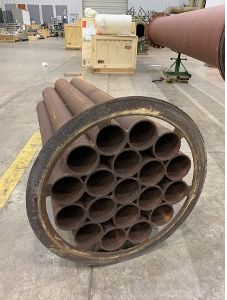

Isolating flow conditioners
Isolating flow conditioners have a blockage factor that forces the flow profile to redistribute as it passes through. This redistribution controls both the asymmetry and swirl disturbances. The design is typically a perforated plate with multiple holes designed to create a well-developed flow profile as soon as possible after the plate.
The search for the ideal pattern of holes to do this job was the subject of much research in the 1990’s as the need for flow conditioning became more and more relevant. A summary of the research from researchers such as Laws, Karnik, Zanker, Gallagher and others is fascinating but outside the scope of this paper. The most widely accepted design of this research was developed by Laws and has become known as the NOVA 50E design.
The NOVA 50E design, Figure 12, is a multi-hole flow conditioner with concentric rings of openings. 16 smaller holes around 8 midsized holes around one large central opening. The size and position of each hole is meant to stimulate the formation of a well-developed flow profile regardless of upstream disturbances. The “50” designation indicates that the plate has approximately a 50% blockage area in the flow path. The success of this design is the balance of three factors: 1) enough blockage to redistribute the flow profile, 2) large enough holes to allow passage of particles and 3) enough opening to reduce the pressure loss across the plate as much as possible. The NOVA design meets the requirements of AGA 3 Section 2.5.5 and APPENDIX 2-D.
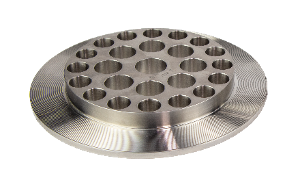
The design is universal for all flow conditions and disturbances. This advantage means a user can have one design flow conditioner for various pipeline installations and conditions. And it gives the user the assurance that most flow disturbances will be removed prior to flow measurement. For as much testing and research has been done of the effects of flow disturbances in a pipe, a user does not know the flow regime and development of their flow profile. Having a flow conditioner improves orifice plate measurement in all standard applications.
Conclusion
The use of a flow conditioner is recommended for all high accuracy orifice plate measurements. The recommended type of flow conditioner is the NOVA 50E design to remove most flow disturbances such as asymmetry and swirl. And users will benefit from the assurance that a well-designed flow conditioner will remove any unknown flow disturbances and problems that could diminish their measurement accuracy.
[1] Effects of pipe elbows and tube bundles onselected types of flowmeters, G.E. Mattingly, T.T. Yeh, Flow Measurement Instrumentation, Vol 2, January 1991
[2] US Patent 5,341,848 “Flow Conditioner”, 1994